Novel System Produces Color on Demand
Ampacet’s FluxQF technology features a quick-dispersion universal carrier with novel machinery that provides automated color blending in quantities down to 50 lb.
Ampacet has developed a streamlined, on-demand color-formulation business with a system that marries the company’s long-standing expertise in masterbatch formulation with unique equipment technology from its 2020 purchase of Israel's Liad Weighing and Control Systems.
The result, to be marketed by Ampacet’s CISystems (Color Integration Systems), is color-on-demand technology tradenamed FluxQF. Suited for injection molding, blow molding and sheet/profile extrusion, FlexQF teams a proprietary quick-dispersion universal color-carrier technology that is compatible with PE, PP, PET, PS, ABS, PC and PVC and a suite of Liad-developed feeding and blending equipment to automate the color-blending process so that Ampacet can make custom colors as needed in quantities from 50 to 2500 lb. Ampacet says FluxQF is a clean, quick-flow colorant in pellet form that runs like a liquid to provide a more flexible and sustainable alternative to both liquid color and standard masterbatch.
Ampacet has set up a FluxQF line at its production plant in Cartersville, Ga., about 4 miles north of Atlanta. The modular system has a significantly smaller footprint than typical pigment batch-blending systems and eliminates the need to stock hundreds of individual pigments and carrier resins. It’s also pristine, with nary a pellet nor pigment particle on the production floor, as all materials are contained and conveyed to the blending system when called for. In Cartersville, the FluxQF line operates in an environment similar to a clean room. Orders can be produced within two working days and customers receive product within four to five working days.
“The strength of Ampacet has traditionally been in white masterbatch,” notes Douglas Brownfield, commercial director for CISystems/Liad Smart. “But from supplying some of the larger brand owners over the years, it’s become clear to us that the more types of products we can offer the customer, the more value we bring, and the more integrated we become in the markets we serve.”
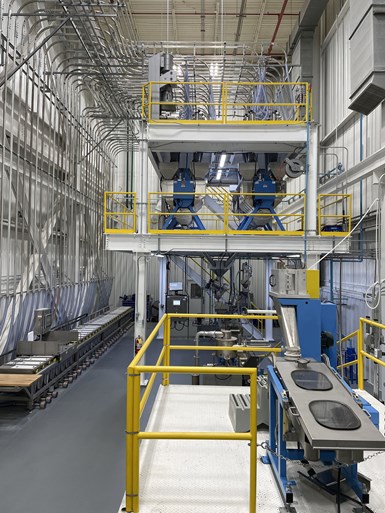
Compact, completely enclosed and clean, the FluxQF line at Ampacet’s plant in Georgia features technology that permits the company to produce colors on demand in a cleanroom-like setting. (Photos: Ampacet)
The line is furnished with a suite of feeding and blending technologies from Liad. These include the Color Save 100 Smart Feeder. This gravimetric feeder provides automatic quick purge between runs; a patented inner floating hopper and isolated load cell to ensure accuracy by negating the effects of vibration; precision weighing at letdown ratios lower than 1%; and ability to integrate with the company’s Spectra 4.0 real-time in-line color-management technology.
Also available on FluxQF is Liad’s DualSave Smart Feeder for two ingredients. This gravimetric feeder is said to provide precise integration of masterbatch, additives and regrind. It automatically adjusts colorant when using regrind, has a single control to regulate two feeders, and eliminates overdosing of expensive colorants.
The line also features Liad’s BlendSave central blending and automated material-distribution system (see Feb. ’21 Close-Up).
How it Works
With FluxQF, custom colors are matched and formulas created in advance. Color formulations are downloaded to the central FluxQF system. When an order is entered, the formulations are pulled up and the operator inputs the quantity. The appropriate FluxQF pigments are automatically selected, precisely weighed, blended and fed into the compounding extruder. This automated blending eliminates the risk of human error, material contamination and segregation, Ampacet says. Through ERP integration, the system’s control is managed digitally, virtually eliminating manual setup and daily operator interactions.
“Imagine being able to blend your own colors and feed them directly to the extruder as you produce parts.”
The setup is novel because not only is Ampacet producing materials for customers from the FluxQF line, but the system itself serves as a showcase for technology that CISystems can offer as a package to processors that might want to simply and streamline their own color-management processes. The system can be designed so that plastic processors can blend their own custom colors in their operations as opposed to buying and allocating warehouse space for hundreds of custom colors that can become obsolete.
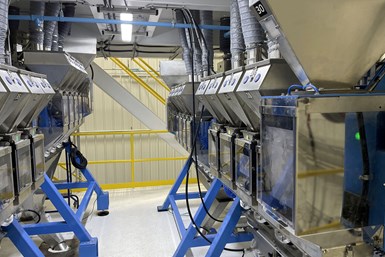
Material is contained in 40 hoppers and fed to the on-demand blending station on demand.
“The concept is similar to having a hardware-store paint shop in-house, but with a clean and pelletized material, adds Brownfield. “Imagine being able to blend your own colors and feed them directly to the extruder as you produce parts. Only 15 to 25 FluxQF pigments are needed to make any color a customer demands.”
Ampacet says FluxQF masterbatches are highly loaded to increase letdown ratios by up to 50%. Quality is said to be improved due to better distribution of color and reduced swirls and gels. The FluxQF masterbatches also are said to support sustainability goals by providing good hiding power for processors running higher percentages of PCR. Compared with applications using liquid color, cleaning costs are also reportedly minimized. FluxQF colors, whites and blacks are FDA food-grade approved.
Related Content
Automotive Awards Highlight ‘Firsts,’ Emerging Technologies
Annual SPE event recognizes sustainability as a major theme.
Read MoreAir Ring Add-On Brings Output to New Level
The Short Stack from Addex sits between the air ring and die and provides high-velocity air flow to boost output and lock in the bubble.
Read MorePurpose-Built System Enhances Capacity and Flexibility for Recycler
A Boston recycler invested in a turnkey shredding, granulation and elutriation system to expand its plastics reclaim business.
Read MoreNew Blown-Film Cooling Technologies Set to Debut at NPE2024
Cooling specialist Addex to roll out new auto-profiling air ring for rotating dies, and new single-plenum air ring.
Read MoreRead Next
Ampacet Acquires Liad Weighing and Control Systems
Ampacet’s acquisition of Israeli company Liad marks its entry into the auxiliary equipment business.
Read MorePeople 4.0 – How to Get Buy-In from Your Staff for Industry 4.0 Systems
Implementing a production monitoring system as the foundation of a ‘smart factory’ is about integrating people with new technology as much as it is about integrating machines and computers. Here are tips from a company that has gone through the process.
Read MoreBeyond Prototypes: 8 Ways the Plastics Industry Is Using 3D Printing
Plastics processors are finding applications for 3D printing around the plant and across the supply chain. Here are 8 examples to look for at NPE2024.
Read More