Plastics Extrusion
Extrusion is a continuous process through which parts of a fixed cross-sectional profile are made. Material is fed through a hopper into an extruder, essentially a rotating screw surrounded by a heated barrel, where it is mixed, melted and pumped through a die. The die gives the part its shape. Types include film extrusion, sheet extrusion, pipe, profile and tubing extrusion.
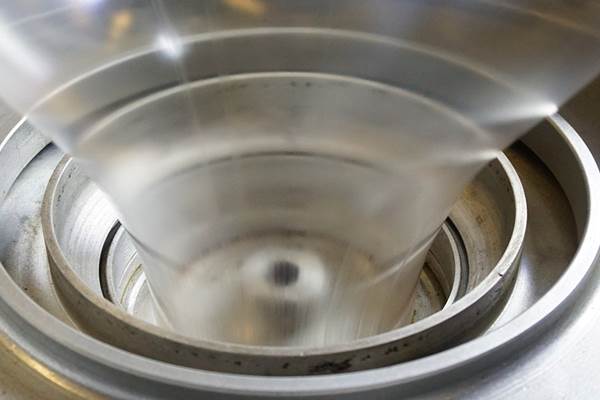
Narrow Your Extrusion Search
ESSENTIAL READING
VIEW ALLFollow These Tips to Fire Up Your Cold Blown Film Line
Firing up a cold blown-film line after a shutdown involves multiple pieces of equipment that all interact. Here’s a look at those components individually and some best practices on how to get your line up and running as quickly and safely as possible.
Read MoreHow to Select the Right Tooling for Pipe Extrusion
In pipe extrusion, selecting or building a complementary set of tooling often poses challenges due to a range of qualitative factors. Here’s some guidance to help you out.
Read MoreThe Importance of Barrel Heat and Melt Temperature
Barrel temperature may impact melting in the case of very small extruders running very slowly. Otherwise, melting is mainly the result of shear heating of the polymer.
Read MoreSingle vs. Twin-Screw Extruders: Why Mixing is Different
There have been many attempts to provide twin-screw-like mixing in singles, but except at very limited outputs none have been adequate. The odds of future success are long due to the inherent differences in the equipment types.
Read MoreTroubleshooting Screw and Barrel Wear in Extrusion
Extruder screws and barrels will wear over time. If you are seeing a reduction in specific rate and higher discharge temperatures, wear is the likely culprit.
Read MoreLooking to Run PCR on a Single Screw? Here’s What to Keep in Mind
Just drop it in and mix it up? Sorry, there’s a lot more to it than that. Here is some of what you need to consider.
Read MoreLatest Extrusion News And Updates
Simulation Software Offers More Insights into Coextrusion, Layer Incapsulation
NPE2024: Compuplast to also debut simulation tools for blow molding and thermoforming.
Read MorePutnam Adds FEP Heat Shrink Tubing to Product Mix
New product made without any processing aids, including silicone oil.
Read MoreNew Rotary Die and Cam Lock Design for Tubing
NPE2024: New design enables quick and easy assembly and disassembly of the crosshead, and eliminates the socket head cap screws.
Read MoreCrosshead Die for Elastomers Adjusts Easily
NPE2024: Mechanically actuated gum space adjustment requires only ordinary socket wrench.
Read More'Hybrid' Die Design Eliminates Weld Lines, Cuts Stagnation
NPE2024: Newest extrusion tool retains benefits of previous design and adds features to boost quality.
Read MoreBlown Film Lines Are Fully Customized
NPE2024: Systems can be furnished for single- to nine-layer for barrier applications.
Read MoreFeatured Posts
Athena Controls Emphasizes Customization: Buy Just What You Need
At NPE, 60-year-old Athena reintroduces itself as a vendor of standard control platforms customized for maximum utility and economy.
Read MoreAddex Continues to Advancing Cooling in Blown Film
NPE2024: Cooling specialist Addex debuts auto-profiling air ring for rotating dies, and new single-plenum air ring.
Read MoreGneuss Extrusion, Filtration and Measurement Technology for Recycling Applications
NPE2024: Gneuss will highlight Omni recycling systems including filtration and measurement solutions.
Read MoreThe Role Barrel Temperatures Play in Melting
You need to understand the basics of how plastic melts in an extruder to properly set your process and troubleshoot any issues. Hint: it’s not about the barrel temperature settings.
Read MoreScrew Design Tips to Boost Productivity
In this collection of articles, two of the industry’s foremost authorities on screw design — Jim Frankland and Mark Spalding — offer their sage advice on screw design...what works, what doesn’t, and what to look for when things start going wrong.
Read MoreProcessing Megatrends Drive New Product Developments at NPE2024
It’s all about sustainability and the circular economy, and it will be on display in Orlando across all the major processes. But there will be plenty to see in automation, AI and machine learning as well.
Read MoreFAQ: Extrusion
However, there are actual limits on increasing output as L/D is increased. Usually these limits are due to the inability of the feed section to deliver more polymer. On smaller-diameter screws, that limit often is determined by screw strength. On small screws you can only go so deep in screw channels before the screw is over torqued and fails. On larger extruders, the efficiency of feeding decreases as the channels get deeper until there is no further increase in output.
There are four main things to consider in selecting the correct stack for your application: the overall cooling capacity, the products to be processed, the mechanical capability, and the rolls’ internal design. Considering just the cooling capacity, the top roll is there to set the sheet thickness as well as its uniformity.
One of the most useful evaluations is the relatively simple calculation of drag flow. Drag flow is simply half the volume of one turn of the metering section per second at a specific screw rpm, which, when multiplied by a units conversion and the melt specific gravity of the polymer, is a very accurate approximation of the output in lb/hr at no head pressure.
Extrusion Supplier Categories
- Web Winders, Unwinds, Rewinds
- Single-screw Extruders
- Saws
- Orientation and Tentering Equipment (for Webs)
- Pipe Corrugators
- Slot Orifice Coaters
- Extruder Screens, Screen Packs, Screen Changers, Breaker Plates, Other Melt-Filtration Equipment
- Sheet Take-off Systems
- Film Take-off Systems
- Web Brakes, Clutches, Chucks
- Extrusion Dies
- Pipe Bellers
- Web Inspection Systems
- Pipe Take-off Systems
- Web Guides, Edge Detectors
- Wire and Cable Take-off Systems
- Pipe Thickness Measuring Equipment
- Roll Coaters
- Dispensing Equipment for Reactive Resin Systems
- Melt Pumps for Extrusion
- Curtain Coaters
- Profiles, Tubing, Hose Take-off Systems
- Calenders
- Cutoff Equipment
- Plastic Lumber Extrusion/Molding Systems
- Web Slitter/Rewinders
- Knife Coaters
- Film, Sheet, Coated Web Thickness Measuring Equipment
- Web Tension Controls
- Multiple-screw Extruders
- Web Cleaning Equipment
- Coextrusion Dies, Feedblocks
- Web Slitters
- Plasma Coating Systems
- Ram Extruders
- Air Knife Equipment
- Monofilament/Multifilament Take-Off Systems
- Rotary Screwless Extruders
- Pelletizers
- Solution Casting Equipment (for Film)
- Air Rings and Internal Bubble Cooling Units
- Profiles, Tubing, Wire Thickness Measuring Equipment