Parts Winners of SPE’s Biennial Thermoforming Conference
This year, there were 10 winners within five categories—silver and gold, for vacuum forming, pressure forming, twin sheet, 3D printed tooling, and parts produced with automation and new technology.
Several notable thermoformed applications comprised the 2021 parts competition awards which were presented at the biennial conference of the SPE Thermoforming Division held September 20-22 in Grand Rapids, Mich. There were 10 winners within five categories—silver and gold--for vacuum forming, pressure forming, twin sheet, 3D printed tooling, and parts produced with automation and new technology. The People’s Choice award was the gold winner for the latter category. Here are the highlights (look for more details and images for each part in a blog of the same name):
▪ People’s Choice Award: Plastics Unlimited, Preston, Iowa
Hagie Sprayer Rear Engine Enclosure Assembly. This enclosure assembly houses a large, sophisticated medical treatment power supply. All primary parts are twin-sheet formed to provide a highly aesthetic, structurally rigid assembly for the enclosure.
Made from a custom color pearlescent metallic acrylic/PVC blend, the material is formed on a smooth tool surface to yield a high-gloss appearance for the multipart assembly. The innovative design provides formed-in threaded inserts to receive quarter turn fasteners, allowing for easy, quick, and simple assembly by the OEM. Overall assembly time reduced OEM man hours by 75%.
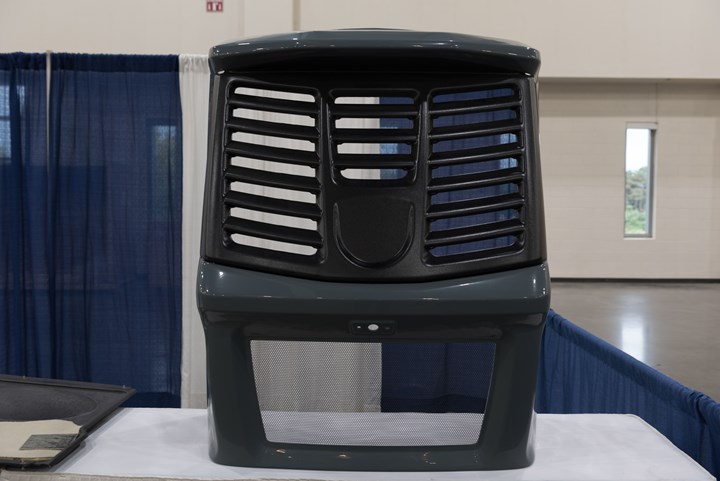
The People’s Choice Award went to Plastics Unlimited for the Hagie Sprayer rear engine enclosure assembly.
Dashboard assembly for Class A motorhomes. Base is a custom color low-gloss ABS. Decorative film is a selected brush aluminum with a polyurethane cap gloss surface. Tooling layout and design accommodates for differentiation in shrink factors for the various components. Shipped as a complete assembly as presented.
▪ Vacuum Forming – Gold: Plastique Art, Sainte-Claire, Quebec, Canada
Ventilator: This enclosure assembly of eight thermoformed parts houses a high-end intensive care unit ventilator. In response to the Covid-19 pandemic, the company’s customer was awarded a contract of 10,000 units to be manufactured urgently. The capacity of the supplier to deliver custom color sheets for prototypes under a week and on short notice for mass production was critical to the success of this project. The sheets were made from acrylic/PVC with two colors and gauges used: white 0.187 in. and grey 0.156 in.
Assembly of the enclosure has been designed to minimize the attachment points. By making the tools in-house with a staff fully dedicated to this project, Plastique Art was able to meet the 10 days lead time for 11 devices ready for certification by a health agency. Upon final approval of the device, they quickly ramped up production to make 10,000 devices in under 16 weeks. For this, multi-cavity, temperature controlled, aluminum molds were required for all parts.
▪ Pressure Forming—Silver: Profile Plastics, Lake Bluff, Ill.
Covers for automatic paint dispenser: This is a two-part project that meets the target price points of the customer and serves as a durable yet easily removable cosmetic cover for an automatic paint dispenser. The tooling is comprised of two machined aluminum tools, water cooled, with an acid etched texture. The part provided the solution for a highly price-sensitive customer who also wanted to meet functional, cosmetic, field service and durability requirements.
Color-matched material—a 0.187-in. acrylic/PVC sheet was selected to eliminate the need for a painted finish on the part, which may have been damaged from normal use in the field.
▪ Pressure Forming—Gold: Ray Products, Ontario, Calif.
Multi-part medical cart: This part includes 12 highly-aesthetic and repeatable pressure formed parts. The assembly includes a combination of molded-in color and painted parts. With the cart originally manufactured using the urethane cast process, pressure forming was able to improve part-to-part repeatability and aesthetics without impacting the overall design of the cart.
After switching to pressure forming—using color matched acrylic/PVC sheet in various thicknesses (0.187 in. and 0.250 in.) as well as a metallic color matched acrylic/PVC sheet in 0.187 in. and 0.250in., the medical device manufacturer was able to significantly reduce total project costs, improve their manufacturing speed, increase part durability, and was guaranteed part-to-part repeatability without the need of unique sets.
▪ Twin-Sheet—Silver: TriEnda Holdings, Portage, Wisc.
Battery Cell Cover: This assembly secures the inner trays filled with fragile lithium-ion batteries. Both the top and bottom clam shell pieces are twin-sheet thermoformed components that are durable, yet light weight compared to prior wooden solutions.
The material is HDPE, 0.500-in. gauge sheet formed on smooth tool surfaces with varying sheet starting gauges and different tool depths between the base and top. Two aluminum production tools ran concurrently, forming one full pack with each cycle. The total solution used additional materials and processes such as EEP foam and injection molded ABS trays. This solution is able to be utilized in many more return shipments, is fully recyclable, and is accessible to be used with both OEM robotics and manual handling as needed.
▪ Twin-Sheet – Gold: Wilbert Plastics, White Bear Lake, MN
Over-the-Road Storage Shelf for Sleeper Area. This part is a storage shelf for the sleeper area of an over-the-road truck cab which was manufactured using the twin-sheet process and completed using internal foam, hardware assembly, and electrical wiring.
The shelf body is formed using ABS sheet with the twin sheet thermoforming process. Mold surfaces are engraved with two different textures to create the customer’s styling needs. The shelf body is then edge trimmed along with mounting bracket openings, and then brackets and internal plates for structure are installed prior to foaming. The result is a structurally sound, aesthetically looking storage shelf that the customer can use as an option to replace the upper sleeping bunk in an over-the-road truck cab.
▪ 3D Printed Tooling—Silver: Plastics Unlimited, Preston, Iowa
Guard:
▪ 3D Printed Tooling—Silver: Plastics Unlimited, Preston, Iowa
Guard: This guard is used in an industrial application. The starting material is black smooth HMWPE with a starting thickness of .187”. This proved to be a great solution for the customer to decrease tooling cost and be able to meet the tight timeline. One impressive part of this project was the extremely quick turnaround. We produced about 400 parts, the tooling, and trim fixture in about one month. The design allows for hidden mounting brackets, allowing for easy and quick assembly. The thermoformed parts of this assembly are formed using production three cavity 3D printed without temperate control.
▪ 3D Printed Tooling—Gold: Catalysis Additive Tooling, Columbus, Ohio
Pallet: This 3D printed thermoforming production tool was used to form pallets, utilizing binder jet technology. The material formed over the tool was 0.250-in. HDPE sheet for 1,000+ parts.
This tool provides many benefits over traditional metal tooling. A one-to-two week manufacturing time gets the tool into the hands of customers twice as fast as a machined metal tool. This tool is half the price of a traditional metal tool. This tool manages to be porous, while also having a 100 Ra surface finish. Moreover, this tool is able to withstand thousands of parts.
▪ Parts Produced with Automation and New Technology—Silver: Plastics Unlimited, Preston, Iowa.
Hagie Sprayer Rear Engine Enclosure Assembly: See People’s Choice Award.
▪ Parts Produced with Automation and New Technology—Gold: Hagans Plastics, Grand Prairie, TX
Chinook Forward Drip Pan. This part replaces an aluminum pan due to both increased strength and weight reduction and is made using oil temperature-controlled match metal aluminum tooling. The material is a PEEK/Kevlar non-woven fiber that must be formed in excess of 500 F.
The new material is able to be formed in a multitude of ways and thicknesses. It can maintain a ridged perimeter while still having some flexibility throughout the center section of the part. This material is completely resistant to all types of POL, (petroleum, oils, lubricants) after forming. This has now been approved to be included in all new Chinook Helicopters manufactured by Boeing and spares for existing helicopters currently in use.
Related Content
All-Motor Driven Pad Printing Machine
Deco Technology now selling the new ML-500E linear & servo motor driven from microPrint of Switzerland
Read MoreOMV Technologies Gets New CEO
Kooper brings 33 years of experience in the industrial and consumer packaging industries to OMV--the closed-loop, turnkey, inline extrusion, thermoforming and tooling systems manufacturer.
Read MoreAutomation in Thermoforming on the Rise
Equipment suppliers’ latest innovations exemplify this trend driven by factors such as labor shortages, higher-speed thermoformers and tighter quality control.
Read MoreHot Wash Systems for Recycling Polyolefins
Herbold can configure wash plants for polyolefins that can produce high-quality, food-grade recyclates.
Read MoreRead Next
Beyond Prototypes: 8 Ways the Plastics Industry Is Using 3D Printing
Plastics processors are finding applications for 3D printing around the plant and across the supply chain. Here are 8 examples to look for at NPE2024.
Read MoreLead the Conversation, Change the Conversation
Coverage of single-use plastics can be both misleading and demoralizing. Here are 10 tips for changing the perception of the plastics industry at your company and in your community.
Read More