Hot Runners: Control for Hydraulic Needle Drives; Wear-Resistant Design for Abrasive Resins; and Specialized Film Insert Molding System
HRSflow has introduced a trio of developments, offering precision needle control in hydraulic systems, wear-resistant hot runners for filled resins, and a line targeting film insert molding (FIM), for the back molding capacitive films, for example.
Italian hot runner supplier HRSflow (U.S. headquarters Byron Center, Mich.) says its new HyFlow technology allows precise control of hydraulic needle drives and can be installed on a full system or select actuators, for a “hybrid” system.
HyFlow specifically targets cascade injection molding for hydraulically actuated hot runner systems, so that the opening and closing speeds, as well as the positioning of each individual pin, can be precisely adjusted via the oil flow rate.
An HRSflow spokesperson told Plastics Technology that the HyFlow can be retrofitted to existing hydraulic systems but the pockets in the tool would have to be modified, as the new cylinders are larger than the standard ones. If a customer is considering an upgrade, HRSflow notes that it has “ready” versions were a direct upgrade is possible since the pockets have been designed from the beginning to accommodate the cylinders.
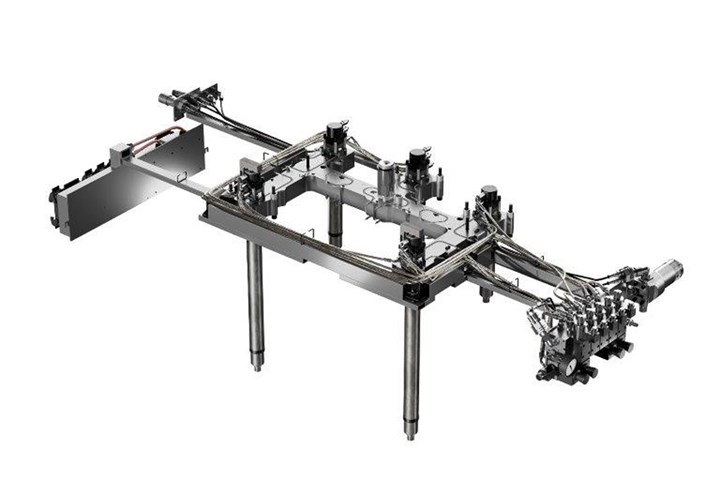
HyFlow technology allows precise control of hydraulic needle drives.
System Targets Filled Resins
HRSflow also launched the Hyper-GF series for processing abrasive thermoplastics. Targeting glass-fiber-reinforced materials, the Hyper-GF series extends the service of the hot runner according to HRSflow, even in high-volume processes. The longer service life derives from the use of special steels and an optimized flow channel design, according to the company.
Back Molding Films
In a current pilot project with a customer, HRSflow shows how its FLEXflow Evo servodriven valve-gate systems can be used when back molding sensitive films. Partnering with film manufacturer Kurz, a film featuring functional capacitive elements for touch operation and decorative elements was back-injected with a clear polycarbonate (PC) in a single step, enabling backlighting in the area of the operating elements. HRSflow says the servodriven FLEXflow Evo technology prevented the thin functional and decorative elements from showing internal stress that would be seen in conventional cascade injection molding. This was due to the evenly distributed, low-pressure spreading of the melt flow front. Damage to the film was also avoided.
Related Content
-
Improve The Cooling Performance Of Your Molds
Need to figure out your mold-cooling energy requirements for the various polymers you run? What about sizing cooling circuits so they provide adequate cooling capacity? Learn the tricks of the trade here.
-
Tunnel Gates for Mold Designers, Part 1
Of all the gate types, tunnel gates are the most misunderstood. Here’s what you need to know to choose the best design for your application.
-
Hot Runners: A View from the Bottom Up
Addressing hot-runner benefits, improvements, and everyday issues from the perspective of decades of experience with probably every brand on the market. Part 1 of 2.