Understanding the Influence of Screw Geometry on Melting Rate
They are not as closely connected as most processors think. Here’s why.
Polymer processing screws have been widely used for years but their performance is still a bit of a mystery to people who use them every day. For one thing, the melting rate is not as closely related to screw geometry as many would suspect. Rather it is more closely related to the peripheral velocity of the screw, the temperature of the barrel, and the polymer’s thermal and viscosity properties.
Tadmor, Klein and others in the 1950s developed a dimensionless relationship to describe the melting rate per unit of down-channel distance. In this equation, the higher the value of F, the higher the melting rate:
F={Vbx rm[Km(Tb-Tm)+( µ÷2 Vj2)] / 2[Cs(Tm-Ts)+l] }0.5
Simplified, this equation is the square root of the heat required for melting divided by the heat supplied by the screw rotation. Notice that there are no screw geometry terms showing in this equation; most of the terms are related to the polymer properties or the barrel temperature. The only unknown is the viscosity (µ), which changes throughout the screw. This requires an assumption for the average viscosity of the melt, which introduces a variable that is hard to quantify without a lot of experience and data.
Further explained, the melting rate for the screw is proportional to the square root of one half the velocity of the barrel relative to the screw plus one quarter the viscosity of the barrel times the viscosity in the film divided by the ratio of the heat transferred from the barrel to the film and the heat transferred from the film to the solid. The latter two are generally quite low due to the poor thermal conductivity of polymers.
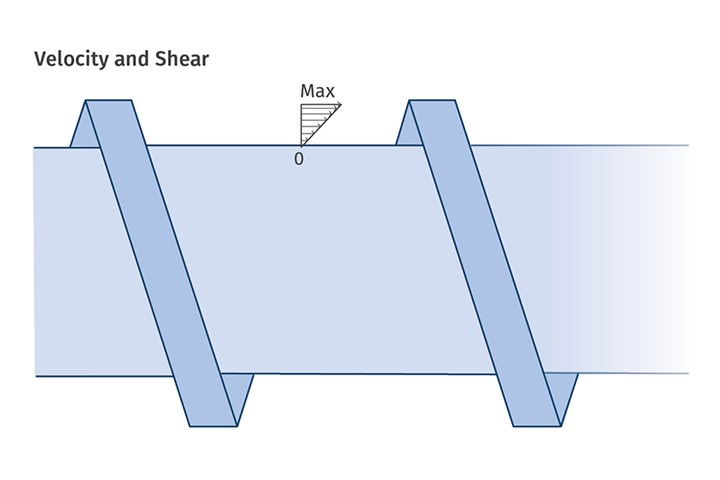
This means that the melting rate (F) is largely independent of the screw geometry for “plain” screws with no shear-type mixing sections or barrier flights. Those devices have been developed to enhance melting by simply redistributing the polymer in the channel to improve its proximity to the barrel. Essentially that is how barriers work. They reposition the melt from the channel to improve the proximity to the barrel wall for improved shear heating of the solids trapped in the continuously decreasing volume in the solids channel.
The same is true of “shear-type mixers” like the various configurations of the famous Maddock-style mixers where the solids are forced by geometry to a location near the barrel wall. Again, the closer the unmelted polymer can be relocated near the barrel wall, the greater the melting rate. The shear rate (melting rate) is maximum at the barrel wall and zero at the bottom of the channel (see illustration).
Poor thermal conductivity of polymers greatly reduces the magnitude of heat transferred to or from the barrel. Additionally, the temperature of the film at the barrel wall is generally near the barrel temperature, eliminating the temperature differential necessary for significant heat transfer. That means that most of the heat entering the film comes from the shear in the channel from the rotation of the screw.
If that weren’t true you could start your extruder up almost immediately upon turning on the barrel heat. Instead, it can take hours to reach a melt condition that will allow startup. This means that for simple flighted screws, higher melting rates require higher screw speed or longer melting sections.
Fortunately, improvements from the 1950s in various barrier designs and shear mixers that separate the melt and unmelt to selectively apply shear to the unmelt allow for more improvements in melting rates without greatly increased screw speeds or greater L/D. If you critically examine each of these devices, you will find each moves the unmelted polymer closer to the barrel wall to accomplish improved melting rates.
ABOUT THE AUTHOR: Jim Frankland is a mechanical engineer who has been involved in all types of extrusion processing for more than 50 years. He is now president of Frankland Plastics Consulting, LLC. Contact jim.frankland@comcast.net or (724)651-9196.
Related Content
The Effects of Temperature
The polymers we work with follow the same principles as the body: the hotter the environment becomes, the less performance we can expect.
Read MoreHow to Stop Flash
Flashing of a part can occur for several reasons—from variations in the process or material to tooling trouble.
Read MoreWhy (and What) You Need to Dry
Other than polyolefins, almost every other polymer exhibits some level of polarity and therefore can absorb a certain amount of moisture from the atmosphere. Here’s a look at some of these materials, and what needs to be done to dry them.
Read MoreHow to Set Barrel Zone Temps in Injection Molding
Start by picking a target melt temperature, and double-check data sheets for the resin supplier’s recommendations. Now for the rest...
Read MoreRead Next
EXTRUSION: Barrier Screws and Mixers
For some reason, there are a lot of barrier screws in operation with high-shear mixers, when a distributive mixer is usually a better choice.
Read MoreThe Role of Screw Design In Efficient Extrusion Of Medical Devices
For extruders of medical tubing, screw design plays a key role in maintaining dimensional control, physical properties, and more.
Read MoreHow to Compare Barrier Screws
When processors asked screw designer Robert Dray how to compare different types of barrier screws, he modeled melting capacity based on the biggest single factor, solids channel area. It gives a quick way to evaluate barrier-screw designs.
Read More