New Product ID Technologies For Industry, Retail & Recycling
Confirming material composition and manufacturing source, anti-counterfeiting, waste sorting, and retail check-out scanning may all get a boost from new ID technologies.
If you manufacture medical or automotive parts, for example, you might wish for a permanent tag that confirms whether a part that failed in the field came from your plant—or not—and was made of the material grade or level of recycle content specified by the OEM—or not. You might want that tag to provide a link to a complete record of the manufacturing conditions and date and even the precise mold cavity for that part.
And your OEM customer might wish for a quick and easy way to confirm that a plastic product carrying its brand is the real thing—or a counterfeit.
Or, if you are involved in recycling or scrap reclaim, you might wish for an easier way to sort and ID the material composition of waste plastics.
Or, if you manufacture food containers or consumer goods, you might delight your customers with a technology applied to the part or its label that provides an accurate price and inventory reading at checkout with a single swipe, eliminating the time-wasting frustration of repeatedly swiping barcodes to get a reading.
While there are already various types of barcodes and some “taggant” additives on the market to provide a permanent ID tag when mixed into plastics, two new solutions exhibited at last fall’s K 2019 show in Dusseldorf promise to extend current taggant and barcode technologies. One is an additive that can be mixed into plastics, and the other is an “invisible” marking technology that can be added to labels or molded into the surface of parts.
Parts Get an Individual ‘Fingerprint’
One new technology is a masterbatch of “micro-marker” taggant particles from Gabriel Chemie in Austria (gabriel-chemie.com), which was utilized in a molding demonstration by Wittmann Battenfeld at the show. Called TagTec, these proprietary taggant particles are distributed throughout the part, but on a micro level, the exact pattern of distribution is said to be a “fingerprint” unique to that part—and to any particular region of the part. This is a feature that distinguishes TagTec from other taggant technologies.

TagTec taggant additives reflect light, perceived by a camera with suitable software as a pattern similar to a constellation of stars at night, that is unique to a particular area of a particular part. (Photo: Wittmann Battenfeld)
In the Wittmann Battenfeld exhibit, a camera and light source were mounted on the robot arm that removed parts from the mold. The taggant particles near the surface of the part reflect light, and the camera fed data to a computer with software that “read” the precise pattern of distribution of the particles in an 11 × 11 mm sector of the part. To the camera, the illuminated sector of the part surface appears as points of light on a darker background, similar to stars in a night sky. Those points can be connected by the software to form a unique “constellation” of taggant points. That pattern can be stored with a record of the molding conditions, date, time, and other data for the part. The data can be recalled later by placing the part in a fixture so that a camera can be aimed at the same exact area of the part to recognize the taggant pattern. The camera and software were supplied by Sensor Instruments of Germany (sensorinstruments.de).
At the show, TagTec was used in molding a PP automotive seat pan with 25% post-consumer reclaim (PCR). As explained by a Wittmann Battenfeld spokesman at the show, TagTec could be helpful if, for example, that part were returned for a warranty claim. The taggant “fingerprint” could confirm whether it is a genuine OEM part, whether it came from a particular molder, and whether it was molded with the correct material. Different taggants could be blended into approved resins for different parts or parts for different OEMs. And if the part passes all those initial checks, the computer record of the molding history of the part could be used to diagnose the root cause of premature failure.
New ‘Holy Grail’ of Digital Watermarking
A second new ID technology showcased at K 2019 does not involve adding anything to the plastic, but is rather a “digital watermarking” technology that can be applied to in-mold labels (IML) or sleeve labels or molded into the surface of the part. A digital watermark is an optical code—a type of barcode—about the size of a postage stamp (2 cm2) that forms part of a label’s artwork or is engraved into the mold surface. One key to the technology is “pixel scattering” that disperses the elements of the barcode over a larger area of the label or part surface so that the code is imperceptible to the naked eye. A key enabling technology is software (from Digimarc in the U.S., digimarc.com) that can enable a smartphone, barcode scanner (fixed, handheld, or robot mounted), or retail checkout scanner to scan the label or part surface and detect and assemble the scattered pixels into the barcode—and then read that barcode to access data associated with that code in an online database. There is no need to add anything to the plastic, nor for any additional special equipment (such as is required to read RFID chips used for product ID).
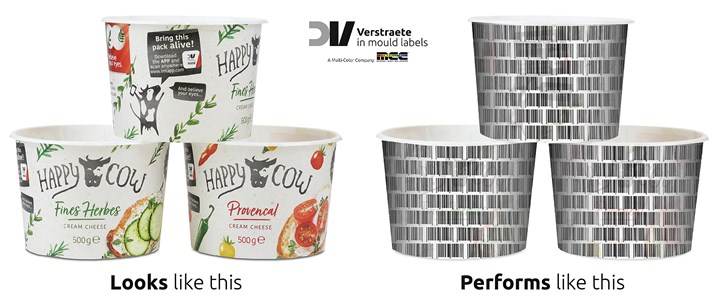
Digital watermarks are a barcode that can be applied to an in-mold or sleeve label (or the part surface) with “pixel-scattering,” which makes the code imperceptible to the naked eye, but can be read by a camera with special software. The barcode is repetitively “tiled” over the surface of the label (or part) so that it can be easily scanned from any angle. Improved sortation for recycling is just one benefit of this approach. (Photo: Verstraete in mould labels)
The same pixel-scattering approach is used to embed digital watermarks in a plastic part without a label. The code can be converted to a CAD/CAM file for mold engraving. However, for the code to be imperceptible it could be part of an overall texture on the part, so it is less suited to glossy smooth surfaces or glasslike clarity.
One further key element of the technology is that it is usually applied in a repetitively tiled fashion over the entire surface of a label or a part. That is meant to enable faster and more foolproof scanning of the label or part from any angle and at high throughputs.
This technology is already in use at the retail level by Wegmans and Walmart. But at K 2019, the emphasis was on its application to recycling by facilitating advanced automated sortation by material composition. It is expected to alleviate current limitations of sortation technology—such as difficulty reading black PET trays with infrared (IR) detectors, or false readings when a sleeve label on a container is of a different material than the container itself.
Digital watermarking potentially offers improved ability to sort all kinds of plastics for recycling, even with sleeve labels covering the container.
Last May saw the completion of the ambitiously titled “Pioneer Project HolyGrail,” which investigated digital watermarking under the auspices of the New Plastics Economy initiative of the Ellen MacArthur Foundation (see May 26, ’19 blog). The HolyGrail project included 30 partners, including Dutch IML specialist Verstraete IML and several resin companies and consumer brands, and was headed by Procter & Gamble. A successful proof-of-concept test was conducted on a prototype sorting system at recycling equipment producer Tomra of Norway last May. It showed that digital watermarks on dirty mixed waste on a conveyor belt could be “read” at 3 meters/min. The technology was also hailed as meeting key industry requirements: It is applicable to any material and multi-material products, does not compromise recyclability or existing recycling streams, can be used with all kinds of full-body labels, is compatible with existing sortation facilities, and can be used to distinguish food from nonfood packaging and compostable from non-compostable waste. (A white paper on the HolyGrail project is available at http://short.ptonline.com/HolyGrail.)
Related Content
Plastics Technology’s Most-Viewed Articles from 2022
Tips, new technologies, resin pricing, best practices and more piqued reader interest at Plastics Technology in 2022.
Read MoreNOVA’s BOPE-HD Film Resin Gains in Globally Available Flexible Food Packaging Applications
Positioned as a recyclable packaging alternative to traditional BOPET films, BOPE-HD film is now available from companies such as Inteplast, JK Materials, Oben Group, and Polivouga.
Read MoreCan Plastic Recyclates be Welded Ultrasonically?
What is possible with ultrasound? Will the result with recycled plastics material actually be worse than with standard material? Do we have to adapt our technology?
Read MoreExact Metrology Now Distributor of HandsOnMetrology.com
The new digital format was set up to share the benefits of 3D metrology with a global community.
Read MoreRead Next
Recycling Partners Collaborate to Eliminate Production Scrap Waste at NPE2024
A collaboration between show organizer PLASTICS, recycler CPR and size reduction experts WEIMA and Conair will seek to recover and recycle 100% of the parts produced at the show.
Read MoreMaking the Circular Economy a Reality
Driven by brand owner demands and new worldwide legislation, the entire supply chain is working toward the shift to circularity, with some evidence the circular economy has already begun.
Read MorePeople 4.0 – How to Get Buy-In from Your Staff for Industry 4.0 Systems
Implementing a production monitoring system as the foundation of a ‘smart factory’ is about integrating people with new technology as much as it is about integrating machines and computers. Here are tips from a company that has gone through the process.
Read More