Reduce Downtime and Scrap in the Blown Film Industry
Sponsored ContentThe blown film sector now benefits from a tailored solution developed by Chem-Trend to preserve integrity of the bubble.
Over the years, purge compounds have demonstrated their effectiveness in substantially minimizing downtime and waste in numerous plastic industries. Plastic processors have distinct purging compound requirements, varying based on the equipment they use. The blown film sector, historically constrained by limited purge compound options due to its unique equipment needs, now benefits from a tailored solution developed by Chem-Trend to meet the specific requirements of companies in this industry.
The Blown Film Challenge
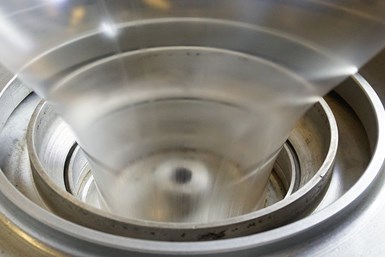
For the majority of blown film processors, preserving the integrity of “the bubble” during purging is a crucial consideration when evaluating commercial purge compounds. The collapse of the bubble can lead to a labor-intensive task of restringing the bubble resulting in substantial downtime. Historically, there were limited purging compound choices that effectively enabled companies to sustain the bubble while efficiently cleaning the extruder and die. Chem-Trend dedicated considerable research to create Ultra Purge™ C1851, specifically tailored to meet the distinctive needs of blown film processors.
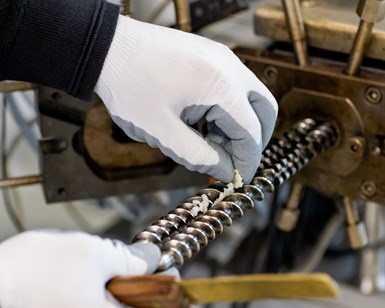
Innovative Additive
Ultra Purge C1851 stands out as a "purging additive," distinguishing itself from conventional purging compounds by being blended with production resin at a ratio similar to masterbatch. This unique characteristic allows easy dosing of C1851 with the customer's production resin through a gravimetric blender, streamlining the loading process compared to traditional purging compounds. A key advantage of Ultra Purge C1851 for blown film companies lies in its ability to preserve the bubble during purging while effectively cleaning the machine and to be able to fully recycle the scrap film generated during the purging process. Maintaining the bubble significantly reduces downtime and labor by eliminating the need to restring the bubble. In contrast, traditional ready-to-use purge compounds typically require the collapse of the bubble, a step many blown film processors prefer to avoid due to the extensive downtime it incurs. Additionally, being able to recycle the film created during the purging process that contains Ultra Purge C1851 allows the processor to complete a color change with zero scrap similarly to what is done when purging the machine with resin.
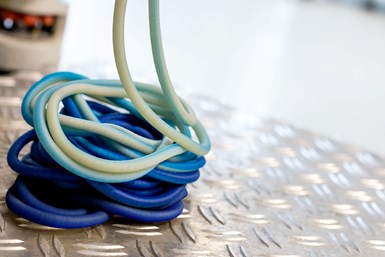
Increased Machine Uptime
The biggest advantage of using Ultra Purge C1851, proven by actual production use, is the reduction in downtime by an average of 75% compared to using resin to clean the machine for dark to light color changes. Ultra Purge C1851 excels at removing color from the screw and die. C1851 can clean the dead spots that traditional purge compounds have a difficult time cleaning. No changes are required to the processing settings of the machine while purging with the bubble up, making it an extremely easy to use purge.
No Screen Pack Change!
In addition to preserving the bubble, blown film companies benefit from another advantage when utilizing Ultra Purge C1851: there's no need to remove the screen pack during purging. The removal of the screen pack can be a time-consuming process, contributing to additional downtime and associated costs. Furthermore, avoiding the manual removal of the screen pack eliminates the risk of injury to personnel. Unlike many purge compounds on the market that necessitate pulling the screen pack during purging, Ultra Purge C1851 will flow easily through the screen pack without encountering any issues.
No Waste…Or Wasted Cost
Film-producing companies employing the blown film process commonly grind and reuse all generated scrap as a cost-saving measure. One important attribute of Ultra Purge C1851 is that is can be recycled in a closed loop system. Every pound of Ultra Purge scrap that is processed can be reintroduced with other production material scrap and made into good product to be sold, resulting in a significant savings. Additionally, Ultra Purge C1851 is safe to be used in the food packaging industry to clean equipment without concern for noxious fumes or odors when processing C1851.
In addition to its role in minimizing downtime during dark-to-light color transitions, Ultra Purge C1851 proves effective in addressing carbon contamination and expediting material changes. Employing C1851 for all dark-to-light color changes serves as a form of preventative maintenance against carbon buildup. By using this purge compound during transitions, any accumulated carbon in the machine is effectively removed. Furthermore, in instances where material changes result in prolonged downtime, C1851 can be blended with the subsequent resin to accelerate the transition process.
To determine whether Ultra Purge C1851 is the ideal solution for purging requirements, request a free sample. Chem-Trend is committed to delivering on-site technical assistance during trials. Dedicated team members will provide complimentary on-site training for all personnel involved in utilizing Ultra Purge, ensuring the proper and effective application of the product.
Request a free sample of Ultra Purge C1851 or visit Chem-Trend at booth W4188 at NPE 2024 in Orlando.