Polyfuze Graphics Expands its Technology with “Intelligent Materials Crystals” for Reusable and Durable Plastics
The company’s unique polymer fusion labeling can now be produced with a unique tagging technology, under the name D-Tect.
A permanent labeling technology from Mold In Graphic Systems (MIGS) and sister company Polyfuze Graphics Corp. (PGC), known as Polymer Fusion Labeling Technology, has been steadily evolving and its latest development is the addition of a unique tagging technology, D-Tect, which can play a role in anti-counterfeiting measures.
MIGS/PGC’s Polymer Fusion Technology has marked over three decades in permanent labeling of rotationally molded polyolefins, and within the last decade made significant strides in the injection molding arena, as well as inroads for a broad range of low-surface-energy (LSE) polyolefin blow molded, injection molded, thermoformed and rotationally molded parts.
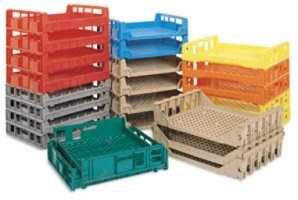
Polyfuze is the science of merging two separate polyolefin thermoplastic polymers together (polyolefin label + polyolefin product) utilizing melting point, time, and pressure, producing a singular piece of plastic without the use of adhesives, tie layers, bonding agents, or secondary surface treatments. As reported previously, the Polyfuze graphics decoration process for injection molded plastics simply requires the use of a standard hot-stamp machine and silicon die to fuse the graphic permanently into the part to become one piece. No adhesives, inks, clear coats nor surface pre-treatments are required with this unique secondary process. And while the graphics may look like a heat transfer or hot stamp foil, the polymer-based material that comprise Polyfuze graphics has been shown to outperform these traditional alternatives.
Marty Mares, v.p. of branding and commercial development, confirms that Polyfuze is compatible with the following materials: HDPE, LDPE, MDPE, flexible PVC, talc-filled PP, glass filled PP, TPO, TPV (Santoprene), TPE, TPR, and structural foam. Rather than trying to adhere to the surface of such polymers, Polyfuze labeling technology literally fuses into the products made from these materials. This process is so permanent, that the Polyfuze label will actually expand and contract with the part during the hottest days of summer or the coldest day of winter, while also being impervious to various chemicals and solvents.
As part of a recent innovation, Polyfuze can now be produced with a unique D-Tect tagging technology, supplied by Intelligent Material, Princeton, N.J. D-Tect is comprised of microscopic, highly-tunable physical, optical, and magnetic crystals—sub-micron ceramic-based particles, introduced into the polymer matrix of Polyfuze Graphics during production. Once these magnetic crystals are embedded into the polymer matrix, they literally become part of the label and are ready to be applied onto reusable packaging containers, crates, totes, coolers used for products such as baking goods and meat and poultry transport, to name a few.
The result is a permanent authenticatable mark on plastic that cannot be lifted, separated, or removed for the life of the product no matter the environment or exposure. D-Tect crystals can be custom formulated to individual customers or even individual customers’ products which then act like a fingerprint for identification purposes. Once introduced into Polymer Fusion Labeling Technology, labels can be manufactured as visible labeling (e.g., branding, warning, informative) or as imperceptible/invisible labeling that can be fused onto customers products and later identified.
D-Tect crystals are impossible to reverse engineer and permanently ensure consumer safety, brand protection, and product security, as well as supply chain governance and quality control for the life of the product. Special handheld D-Tect readers tuned to individual customers labels are available to be purchased for use in authenticating and/or identifying products by distributors and end users.
Related Content
Film Extrusion: Boost Mechanical Properties and Rate of Composting by Blending Amorphous PHA into PLA
A unique amorphous PHA has been shown to enhance the mechanical performance and accelerate the biodegradation of other compostable polymers PLA in blown film.
Read MoreAvoid Four Common Traps In Granulation
Today, more than ever, granulation is an important step in the total production process. Our expert explains a few of the many common traps to avoid when thinking about granulators
Read MoreScaling Up Sustainable Solutions for Fiber Reinforced Composite Materials
Oak Ridge National Laboratory's Sustainable Manufacturing Technologies Group helps industrial partners tackle the sustainability challenges presented by fiber-reinforced composite materials.
Read MoreA Recycling Plant, Renewed
Reinvention is essential at Capital Polymers, a toll recycler that has completely transformed its operation in a short period of time.
Read MoreRead Next
For PLASTICS' CEO Seaholm, NPE to Shine Light on Sustainability Successes
With advocacy, communication and sustainability as three main pillars, Seaholm leads a trade association to NPE that ‘is more active today than we have ever been.’
Read MoreRecycling Partners Collaborate to Eliminate Production Scrap Waste at NPE2024
A collaboration between show organizer PLASTICS, recycler CPR and size reduction experts WEIMA and Conair will seek to recover and recycle 100% of the parts produced at the show.
Read MorePeople 4.0 – How to Get Buy-In from Your Staff for Industry 4.0 Systems
Implementing a production monitoring system as the foundation of a ‘smart factory’ is about integrating people with new technology as much as it is about integrating machines and computers. Here are tips from a company that has gone through the process.
Read More