Star Plastics Adds Leistritz Compounding Line
Twin-screw was installed at its West Virginia plant in December as part of $5 million expansion.
Star Plastics has installed the first of two new twin-screw compounding extruders at its plant in Ravenswood, W. Va. This new machine marks the first phase of a larger investment that will amount to more than $5 million in 2022 as the company commits to major growth within its current market space to support current and new customers.
The new twin-screw is a 75 mm built by Leistritz and is Star’s largest
to date, improving production rates and tripling capacity in anticipation of continued long-term growth, the company said. The equipment also allows the Star team to increase the breadth of its product offering.
The Leistritz extruder was installed in Star’s Ravenswood facility in December 2021, with trials running throughout January 2022. The new high-torque machine provides improved material incorporation and dispersive mixing during production, and its special screw design can be modified to generate higher quality production outputs, Star Plastics says.
Star Plastics plans to introduce more product offerings for its customers and become a full-service supplier of compounded engineering-grade resins. When asked about this new investment, CEO Donald Wiseman said, “Our customers asked us to expand our current portfolio and capabilities—they want our quality, service, and delivery on even more material options, and we are going provide them with just that.”
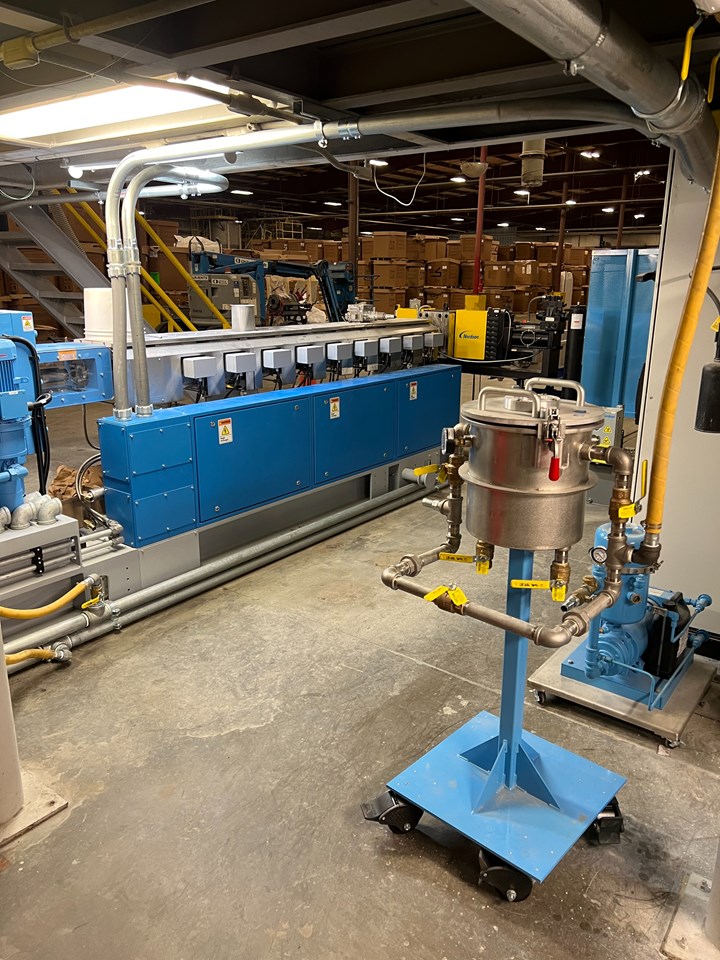
While Star is considered a leader in furnishing compounds for the E&E market, the additional polymer types will open the door to new markets and product development, allowing the company to offer a wider range of glass-filled and composite-type materials not presently within its product line-up. The equipment investments will further support Star’s growth with the Italian specialty resin compounder LATI as it produces LATI materials in North America.
“The extruder is an exciting investment for us. We’re eager to offer Star Plastics’ customers even greater access to more advanced engineering compound grades and to satisfy their needs far into the future,” said Star founder Doug Ritchie.
From an operations standpoint, while increased capacity and production rates are important, Operations Manager Mike Vacek notes that, “This new twin screw not only improves our ability to produce high-quality, consistent material; more importantly, it also enhances our ability to operate even more safely, given its state-of-the-art safety interlocks.”
Star’s second new twin-screw, a used Coperion 58-mm purchased from Aarom Industries, is expected to be installed in April.
Related Content
-
Processing Megatrends Drive New Product Developments at NPE2024
It’s all about sustainability and the circular economy, and it will be on display in Orlando across all the major processes. But there will be plenty to see in automation, AI and machine learning as well.
-
Configuring the Twin Screw Extruder: Part 4
For many compounding operations, material is fed to the extruder at the feed throat. This is the case when feeding a single polymer or a blend of polymers mixed with solid additives. Some ingredients, however, present a challenge in feeding. Here’s how to solve to them.
-
The Path to Pellet Perfection
In underwater pelletizing, numerous variables in the equipment, process and material affect pellet shape, consistency and quality factors such as fines. Defining the “perfect” pellet depends on the conditions of end use, and achieving that ideal requires understanding of the causes of imperfections.