Medical Extruders Are Direct Driven
No gearbox or belt drive eliminates gear oil and airborne dust particles from belts.
The new MED-EX Modern Medical Extruder line from US Extruders is billed as ideal for processors that operating in a low-volume business with lots of product changeovers as well as those engaged in high-volume production. The series is available in sizes ranging from ½ in. to 2.5 in.
The machines feature direct drive technology for precise speed control and quiet operation. There is no gearbox or belt drive, so there is no gear oil and airborne dust particles from belts, a critical feature when extruding in a controlled manufacturing environment.
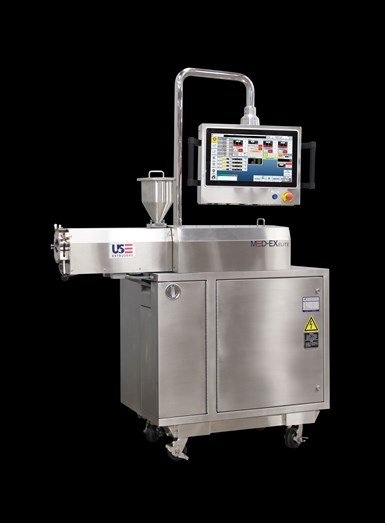
To meet the increasingly stringent quality requirements within the medical extrusion market, US Extruders has developed virtual pressure measurement technology to eliminate transducer and rupture disc ports in the barrel and reduce stagnation points where material can degrade. Degraded material that ends up in medical tubing causes a weak point in the final device. This is especially important for applications that demand superior quality beyond dimensional requirements where maintaining mechanical properties is paramount. Examples include balloon tubing, heat shrink tubing and polymer stent tubing.
What’s more, the machine builder has developed a custom “universal” barrier/mixing screw specifically designed for nylon 12, PEBA and TPU reflow compounds that are commonly used for multi-durometer catheter jacketing applications. This screw design, combined with either pressure control or a melt pump, allows for optimal melt temperature uniformity and pressure stability better than 1%, according to the company.
Related Content
-
Avoid Four Common Traps In Granulation
Today, more than ever, granulation is an important step in the total production process. Our expert explains a few of the many common traps to avoid when thinking about granulators
-
Specialty Purging Compounds Optimize Color and Material Changeovers
Selecting of the correct purging compound can speed up material and color changeover time and reduce scrap. You’ll even save on material.
-
Troubleshooting Screw and Barrel Wear in Extrusion
Extruder screws and barrels will wear over time. If you are seeing a reduction in specific rate and higher discharge temperatures, wear is the likely culprit.