Specialty Purging Compounds Optimize Color and Material Changeovers
Sponsored ContentSelecting of the correct purging compound can speed up material and color changeover time and reduce scrap. You’ll even save on material.
Share
Read Next
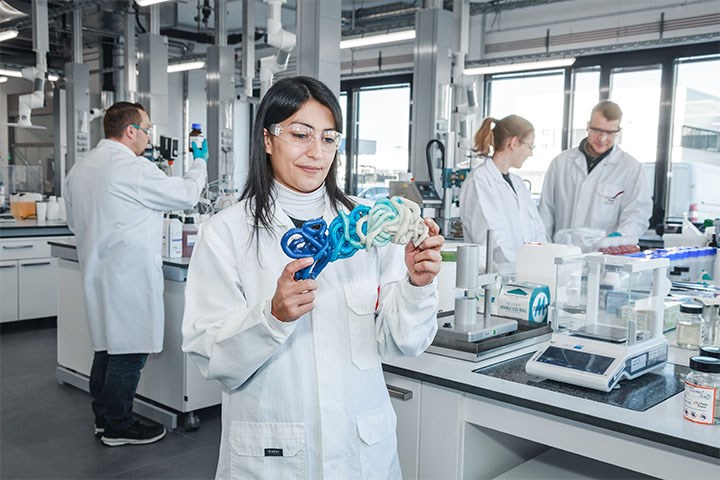
For many press operators of injection molding, packaging, extrusion, blown film, and extrusion blow molding machines, the traditional cleaning methods used between color and material changeovers lead to a predictable and frustrating cycle:
- Residue remains after cleaning
- Even the smallest remnants create buildup over time
- Production problems occur
Parts can come out streaked, spotted, and discolored, which results in unusable pieces, higher scrap rate, more downtime, lower-quality finished products, and machine damage that’s compounded by daily use.
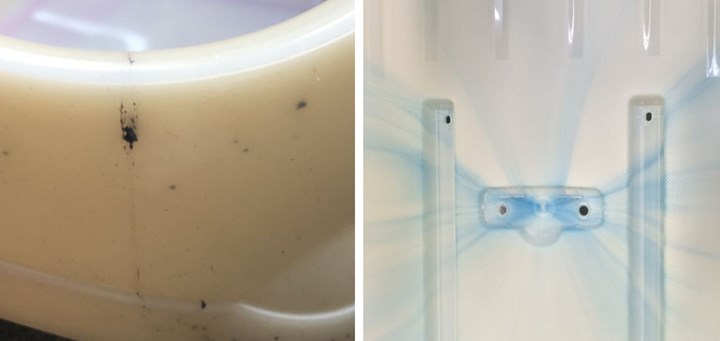
Black spots and color contamination can be minimized with purging compounds. See more common challenges and solutions at Chemtrend.com.
How can specialty purging compounds help?
All purging compounds are not created equal. Specialty purging compounds, like those available from Chem-Trend’s Ultra Purge™ brand, are the result of years of shop-floor research coupled with advanced scientific development. They cover a wide array of polymers, operating temperatures, and equipment types to provide a remedy for common production issues and can add to the life of a press. Within the line, formulations can also be tailored to meet the needs of application processes such as extrusion as opposed to injection or blow molding, which present different challenges.
Purging compounds offer advantages that can produce long-term gains and value for producers. A significant plus of purging compounds is their high efficiency, which allows for the use of less product without requiring changes to existing machinery and equipment.
Following a tailored procedure in a specified order for your process can create predictable and seamless results, including greatly reduced scrap, an increase in mold-cleaning speed, fewer and shorter stoppages, and ultimately less daily wear on expensive equipment.
Why Purging Compounds? from Chem-Trend on Vimeo.
Some colors are easier than others
There are many things to consider when it comes to choosing the right purging compound for your process. The purge grade selected may differ between color change, removal of carbonized residues, or machine shut-down. The processing type also plays a role, and matching up polymer and viscosity is essential for successful purging. Processing temperature, length of production, and order also come into play.
Changeover from higher-temperature darker colors to lower-temperature lighter pigments will definitely require a purging compound like Ultra Purge™. Some types of pigments, such as dark blue, red, or purple, are more prone to “impregnate” the metal surfaces with which they come into contact. Use of a low-grade purging compound in such cases can result in hours of pigment removal, significant material waste, and more costly complications in the long run.
The use of white colorants after a darker pigment can be especially challenging due to the naturally abrasive nature of the former. They also contain heavy TiO2 pigments, which scrub every surface of the machine, releasing color residue that causes contamination. Purging compounds are often the only way to ensure that white parts can be generated without producing excessive scrap or increasing production time.
Problem solved: safe for hot runners
Historically, producers have avoided usage of products in hot runners and manifold heaters due to damage concerns for the expensive equipment and resulting constant stoppages. With specialty formulations like Ultra Purge™, this is no longer an issue, thanks to their non-abrasive technology. This type of product is specifically designed for thin-wall polyolefin packaging (container, trays, and lids) and is highly effective at removing color and carbon residues.
Faster and successful color changes can be achieved by following the same steps and procedures with every use, and even “on -the-fly” purging requires no machine setting changes or soak time. Eliminating extra steps can help producers accelerate their process in ways that just aren’t possible with purging compounds that aren’t specialized.
Please visit Chem-Trend’s Purging Compound Solutions page to learn more, request a sample, or contact a purging compounds expert.