Milacron’s Massive Booth Highlights Multiple Brands
NPE2024: Coinjection of postconsumer resin, in-mold decoration, LSR micromolding and bioplastics processing are just some of the machine displays at Milacron's booth.
Milacron has filled the corners of its 26,600-square-foot NPE2024 booth with technology representative of its various fellow operating companies and preferred partner brands, including DME, FANUC Roboshot, Mold-Masters and its own injection molding machine line with the debut of its M Series. Milacron’s Andy Stirn says most prominent will be a 1,070-ton M-Series injection molding machine running a SyBridge Technologies 2-cavity tool for 5-gallon pails featuring in-mold label (IML) decoration and up to 50% recycled content via coinjection and a Mold-Master valve-gated hot runner.
Featuring twin injection units and a high-base machine design, the cell showcases the potential to free drop the buckets onto a conveyor running below the press, which is still common for many pail molders. Here, backside automation provides label insertion, with key stats on the label, as well as part removal and full inspection.
The Mold-Master hot runner controls are fully integrated into the Milacron’s injection molding machine control, with plans to utilize different resins and mixes of materials, including in different colors, to showcase how the coinjection technology can hide or reveal the core in a very controlled manner.
Stirn says the pail is a great application to utilize coinjection for sandwiching recycled content between layers of virgin resins, but there are others. While 5-gallon pails would normally run in cycle times of 18-25 seconds, Milacron is targeting 18- to 20- second cycles for the show display. “For coinjection, that is phenomenal,” Stirn says. “For a standard monolayer setup that’s competitive, to go that fast with coinjection of two pails is special.”
Milacron has three material partners for the project, with Shell supplying virgin HDPE for the skin and the core uses postconsumer resin (PCR) from KW Plastics and LyondellBasell that has been reclaimed, reprocessed and repelletized, with the PCR core to alternate each day between the two suppliers. To support this level of production, Milacron’s booth includes a 20-by-30-foot “Resin Room” with two 30-ton air-cooled chillers and a complete material handling system, including surge bins and vacuum pumps. Stirn notes that the company coinjected a pail at NPE2015, but it was from only a single-cavity mold running at 45-48% PCR core level.
The DME section of the booth has a 170-ton Q series servo-hydraulic machine with automation as well as a high amount of DME products inside the tool, including collapsible cores and some serialization devices for part identification. Running a BioLogiQ bioresin, the machine is molding a phone holder. Stirn says the Q series promotes energy efficiency and automation integration. The machine has a small, heated sprue built-in, and a DME controller and hot runner, for the single-cavity tool.
Next to the DME area, Milacron is promoting its various aftermarket capabilities, including control technologies for retrofitting, information on its Industry 4.0 M Powered real-time monitoring and analysis program, as well as a general aftermarket display. “Aftermarket is a big part of our business and value proposition,” Stirn says.
A 55-ton all-electric Fanuc Roboshot with DIY Robots automation is set up for an LSR application in partnership with a cold-deck runnerless tool from M.R. Mold & Engineering and metering from Nexus to create very small umbrella-type diaphragms from a four-cavity tool. How small are the parts? Small enough that Milacron hasn’t been able to weigh them individually, but combined they weigh just 0.9g. Milacron turned to DME and its machining expertise to fabricate an 8-mm plunger system for the application to dose in material with precision. The positional accuracy of the plunger is due in no small part to the machine. “No machine controls motion like a Roboshot,” Stirn says.
Another all-electric 275-ton Fanuc Roboshot is molding medical vials from a 48-cavity tool using a Mold-Masters hot runner system. Post-molding, a platen-mounted robot removes the 48 vials and places them on conveyor above the clamp, with the parts separated into “lanes.” Stirn says this setup helps “containerize” production for traceability while minimizing floor space impact.
In a partnership with Kurz, Milacron is introducing its new M series two-platen servo-hydraulic machines. In a touch display application geared toward the automotive or appliance markets, Kurz-supplied decorative and functional foil is fed through the open tool for back molding. The 500-ton cell has three integrated robots, including one that enters the mold with an infrared heater used to heat the foil. Another robot removes the molded part from the press and places it on a fixture for trimming. The finished part is then moved to another fixture where it’s backlit to show the different patterns and buttons that are revealed as it is interacted with by consumers.
In the middle of Milacron’s booth, the company has a nonoperating 90-foot extrusion line. The SG75 single-screw extruder is paired with a new pipe head that Milacron is making in-house for the first time. The display also features pullers and saws, plus a new extruder control. At the end of the line, a small cobot picks up finished pipe, stacking and arraying the product.
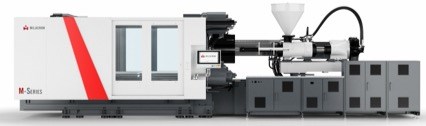
The Milacron M-Series of injection molding machines gets its global launch at NPE2024. Source: Milacron
Related Content
Are Your Sprue or Parts Sticking? Here Are Some Solutions
When a sprue or part sticks, the result of trying to unstick it is often more scratches or undercuts, making the problem worse and the fix more costly. Here’s how to set up a proper procedure for this sticky wicket.
Read MoreHow to Get Rid of Bubbles in Injection Molding
First find out if they are the result of trapped gas or a vacuum void. Then follow these steps to get rid of them.
Read MoreImprove The Cooling Performance Of Your Molds
Need to figure out your mold-cooling energy requirements for the various polymers you run? What about sizing cooling circuits so they provide adequate cooling capacity? Learn the tricks of the trade here.
Read MoreHow to Stop Flash
Flashing of a part can occur for several reasons—from variations in the process or material to tooling trouble.
Read MoreRead Next
Larger, All-Purpose, All-Electric Machines Debut from Milacron
As reported in our Keeping Up section last month, Milacron LLC invited Plastics Technology to its Batavia, Ohio, headquarters for an exclusive preview of its new Elektron line of all-electric injection presses ahead of their official debut at Milacron’s open house Apr. 24-25.
Read MoreMilacron Coinjection Tech Approved For Fruit Cans & Recyclable Coffee Pods
First-to-market clear plastic cans wil arrive early next year.
Read MoreMaking the Circular Economy a Reality
Driven by brand owner demands and new worldwide legislation, the entire supply chain is working toward the shift to circularity, with some evidence the circular economy has already begun.
Read More