
Baeropol RST by Baerlocher is an additive blend. Here’s it’s shown in the prill form (sugar-like particle size).
Despite countervailing forces such as lower virgin resin prices, strong demand continues for post-consumer recycled (PCR) content in applications such as packaging, pipe and furniture. One reason is the commitment by major brands to address consumer demands for sustainable products and packaging. Also, there are new regulations that encourage the reuse of plastics to support circularity. For instance, in 2022, the UK will introduce a Plastic Packaging Tax to incentivize the incorporation of recycled plastic. Also, the Council of the European Union (EU) adopted a directive in 2019 that introduces upcoming restrictions on certain single-use plastic products. It includes targets for plastic bottles to contain at least 25% recycled content by 2025 and 30% by 2030.
As demand for, and use of, PCR content continues to increase, there has been a renewed focus on the issue of polymer degradation. The properties of PCR content, such as melt flow, color and contamination, are directly related to proper stabilization—either upstream by plastics producers or downstream by recyclers and processors.
However, re-stabilizing PCR products has, to date, attracted less attention than the larger challenges facing our recycling economy, such as improving recycler education and updating recycling facilities. In the U.S., for example, the recycling industry has invested, and continues to invest, in new technologies to improve the sortation and quality of recycled materials. These efforts should help make PCR content re-stabilization more effective.
The properties of PCR content, such as melt flow, color and contamination, are directly related to proper stabilization.
While these infrastructure improvements are critical, PCR material stabilization is also vital to enable the plastics industry to produce the high-quality PCR material needed to meet brands’ requirements. Effective stabilization can:
• Improve the physical properties and extend the useful life of the final application.
• Enhance the processability of the material to maintain productivity.
In turn, better properties and processability can help to:
• Increase the percentage of PCR content that can be incorporated in a given application.
• Expand the range of applications that use PCR material.
Benefits of PCR Content Stabilization
Every time a polymer is heated, sheared or stressed during recycling, its original molecular structure can change. These changes affect physical properties such as impact and tensile strength. They also affect melt flow—a key factor in efficient throughput and the complete filling of a mold. Further, recycling can cause a material’s color to change, which can limit the applications in which PCR material is used. Other visual properties, such as gloss or clarity, can suffer as well.
Chemical stabilizers can prevent or minimize these undesirable effects. They can optimize melt flow for better processing, preserve physical properties that support better application performance, and prevent or minimize oxidative degradation that can lead to cracking and failure.
Chemical stabilizers can be incorporated during resin manufacturing, allowing the virgin material to be recycled several times. Also, stabilization can be added during PCR material filtration by recyclers, which involves melting and cleaning the resin to remove impurities that cause gels and black specks. Maintaining a constant level of stabilizers in your resin at every stage is key to optimal recycling.

HDPE PCR flakes.
Some recyclers use stabilization technology to improve the quality of their PCR material or to meet customer requests, while others do not—either because their customers are not asking for stabilized PCR content or to avoid adding costs to their product in a market with slim profit margins.
However, the recycling industry is demonstrating stronger support for the use of stabilizers. Chemical stabilizers help advance four important goals of the Association of Plastic Recyclers (APR) to improve the plastics circular economy: increasing supply, enhancing quality, expanding demand and communicating value. Stabilization expands potential uses for PCR content, due to the material’s higher quality vs. degraded resin, and enables more content to be reused for higher-value applications.
How Stabilizers Work
When a resin is made by a polymer producer, its structure is highly controlled to provide excellent consistency in physical and visual properties. It is also often accompanied by a base level of stabilizer blends, which allow these properties to remain unaffected by the harsh process conditions the resin will be subjected to during its conversion to the final product.
Maintaining a constant level of stabilizers in your resin at every stage is key to optimal recycling.
These stabilizer blends are typically composed of several components:
• An antacid that will neutralize leftover catalyst residuals from polymer production. These residuals can negatively affect color and physical properties.
• A primary antioxidant, which is active in the processed article. These antioxidants prevent auto-oxidation by capturing oxygen-centered free radicals that propagate the degradation chain reaction.
• A secondary antioxidant, which works during the melt phase. It destroys hydroperoxides generated during the melt, which would otherwise destroy the primary antioxidant. Secondary antioxidants also help to delay the formation of quinones, a color-changing biproduct that forms when primary antioxidants are consumed.
Often, the base stabilizer package is only sufficient for a single use and is depleted within the first use of the polymer. With an insufficient level of stabilizer in the polymer, harsh conditions during recycling can more aggressively degrade the material and damage its properties.
Maintaining Productivity
One argument against using PCR content is the potential impact on high-speed injection molding, blow molding and extrusion processes. PCR material with poor melt flow can slow throughput. The addition of a stabilizer can help prevent this issue.
During the process of oxidative degradation, polymer chains change in different, negative ways. Polymers like HDPE and LLDPE tend to crosslink, raising melt viscosity and causing artifacts like gels. In polymers like PP, the oxidative degradation process results in chain scission, causing PP chains to be cleaved and melt viscosity to decrease. These changes in melt flow create issues with consistent melt processing. With the inclusion of a stabilizer package, changes to the polymer chains are mitigated and a more consistent melt flow can be expected.
Stabilizer packages can support the current version of the resin while enhancing future uses. One example is post-consumer HDPE bottles that are sorted, ground, washed, dried and then extruded into a fractional-melt pellet. To increase the flow of fractional-melt HDPE, metal stearates such as calcium stearate and zinc stearate that have lubricative properties can be used. These additives have the added benefit of being great acid scavengers, helping to protect stabilizer systems and prevent equipment corrosion.
PCR material with poor melt flow can slow throughput. The addition of a stabilizer can help prevent this issue.
Maintaining Recyclability
One concern about the use of stabilizers is the potential contamination effects they may have on recyclability. As to be expected, many stakeholders are cautious about contaminating the recycle stream, and industry groups are continuously working to provide practical guidelines. However, additives are becoming an increasingly valuable tool for users of recycled material. Many additives can be used at reasonable levels during resin production while still permitting the material to be recyclable. These additives include stabilizers, nucleating agents, lubricants and impact modifiers.
Expanding Applications
An important benefit of stabilizing PCR content is expanded application possibilities. With effective stabilization, PCR material can be used in higher-value applications rather than downcycled into low-value parts.
For instance, the American Association of State Highway and Transportation Officials (AASHTO) adopted new specifications to account for possible failure modes of corrugated HDPE pipes that incorporate recycled content. The new specifications now include a requirement for a minimum length of oxidative induction time, a measure of the level of stabilization present in a resin. The Association recognized that polymer stability was needed to prevent chemical failure in these pipes, or else the use of recycled HDPE would be a liability. Adding stabilizers helps HDPE recyclers meet these stringent requirements and encourages the use of recycled HDPE in drainage pipes by enabling long lifespans.
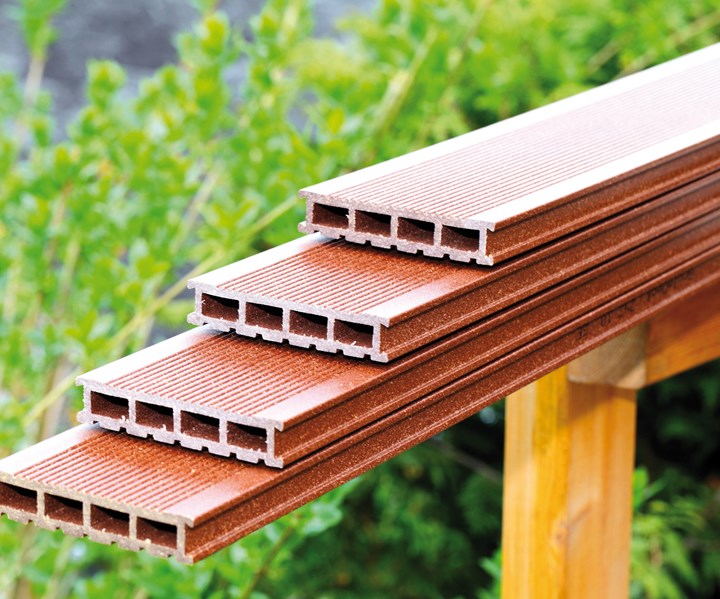
Wood-plastic composite (WPC) stabilized with Baeropol RST stabilizer.
Another example is wood-plastic composites, which have been a traditional success story for recycled polyolefins.
ABOUT THE AUTHORS: Roberto Nunez, Ph.D., is business head of the Special Additives division of Baerlocher USA. He has held this position since 2017 and is responsible for managing P&L, sales, marketing, strategy development, innovation, and technical support for the division. Before joining Baerlocher USA, Nunez was a member of the Milliken Chemical executive leadership team for 12 years. baerlocher.com.
Ian Query is a technical specialist for the Special Additives division of Baerlocher USA. He has held this position since 2018, and is responsible for supporting downstream recycling and wood-plastic composite customers. Prior to joining Baerlocher, Query was a researcher for Nike’s Material Science Innovation team, focusing on material processing innovation and laboratory testing. He also has experience in PVC processing, serving on Emerald Kalama Chemical’s applications team, and performing research on PVC plasticizers. query.ian@baerlocher.com
Related Content
Market Changes Spur Industrial Recycler to Enhance Capabilities in Clear Plastic Reprocessing
Butler MacDonald found new business and flexibility thanks to a big step-up in purging efficiency.
Read MoreReworking Off-Spec Material? Add Some Science to the Mix
Reworking off-specification material and low-demand material is good for the compounder and good for the environment. Here’s how to make sure it’s good for the customer too.
Read MoreInside the Florida Recycler Gearing Up to Take on Scrap at NPE2024
Hundreds of tons of demonstration products will be created at NPE2024 next spring. Commercial Plastics Recycling strives to recycle all of it.
Read MoreEnergy Company Plans to Feed Recycling Scrap Into Fuel Production
Clean Planet Energy reaches agreement with KW Plastics to Feed its Low-Sulfur Fuel Plants
Read MoreRead Next
Making the Circular Economy a Reality
Driven by brand owner demands and new worldwide legislation, the entire supply chain is working toward the shift to circularity, with some evidence the circular economy has already begun.
Read MoreLead the Conversation, Change the Conversation
Coverage of single-use plastics can be both misleading and demoralizing. Here are 10 tips for changing the perception of the plastics industry at your company and in your community.
Read MoreBeyond Prototypes: 8 Ways the Plastics Industry Is Using 3D Printing
Plastics processors are finding applications for 3D printing around the plant and across the supply chain. Here are 8 examples to look for at NPE2024.
Read More