Market Changes Spur Industrial Recycler to Enhance Capabilities in Clear Plastic Reprocessing
Butler MacDonald found new business and flexibility thanks to a big step-up in purging efficiency.
Butler MacDonald has seen changing markets before. Founded as a scrap metal recovery business in 1983, the company shifted to recycling plastics as so many manufactured goods shifted to plastic materials during the 1980s and 90s. Recently, the COVID-19 pandemic put the industry through a sudden change as demand for plastic materials skyrocketed for PPE, food and drink containers, and more. Inevitably, this disruption brought change to Butler MacDonald.
The company processes postindustrial materials including polyolefins, styrenes and more. About 50% of its business is toll processing, meaning that companies hire Butler Macdonald to process a material and send it back to them.
“Our goal is to solve problems for customers. Often our business comes from some kind of mistake that has been made,” says Jeff Pierce, general manager at Butler Macdonald. The problem could be a silo of mixed, incompatible materials or a lot of molded products that do not meet specifications. Butler MacDonald will help the company recover the value in the material through sorting and/or recycling. Often, a company will come back to Butler Macdonald months or years later, when a completely new issue has arisen.
Because of the business model, in-feed for Butler MacDonald is always changing and widely varied. The list of accepted materials on its website includes nearly every category of polymer resin. A lot of that material has color, and historically this has limited the amount of clear and white material the company processes because of the time and expense required for changeovers.
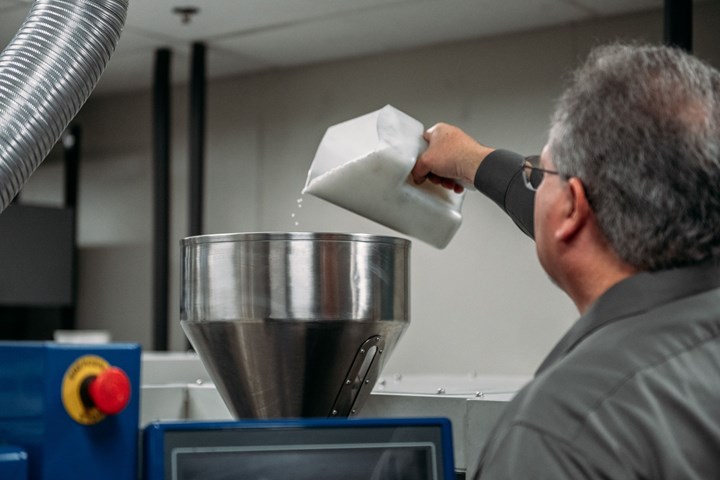
Purging compounds and procedures can vary depending on the type of resin and the configuration of the extrusion operation, but often processors will find one compound will be suitable for most of their processes. Source: ID Additives.
Butler Macdonald’s two extrusion lines are a key part of its operation, which includes size reduction, sortation and pelletizing. Whenever extrusion equipment is changed over, it’s necessary to purge remaining product from the system. Any regions of slower flow can become areas where material can stick behind and contaminate the next run. This is especially a problem when transitioning from a dark material to light or clear materials — even a small amount can leave an obvious visual defect. So, before processing a new material, especially clear, the system must be thoroughly purged. Purging consumes both material and time, and therefore value.
During the pandemic, the demand for plastic material increased far beyond what the industry was ready to supply. For Butler MacDonald this translated to opportunities for more and bigger jobs in clear and white. To make the most of them, they needed to answer the purging challenge. Purging for hours in efforts to remove material that would affect quality in its output expended both time and material. Pierce relates they would sometimes discover “fish eyes,” a hazy discoloration with a black speck in the center, indicating contamination with carbon, and determine that additional purging was needed.
Before long, they were shopping for a new commercial purging compound. At a 2022 conference they met with staff from ID Additives and decided to trial 25 pounds of the company’s MP Purge, a purging compound formulated to clean out equipment completely and quickly. The compound’s foaming action helps it expand into hard to reach spaces.
Dave Denzel, technical manager at ID Additives, helps customers tailor purging solutions to their operations. “I’m a visual person,” Denzel says, “So I like to be there on hand to see what the system looks like, because there can be many different variations to the equipment.” Extruder configuration and the processing material can affect not just which compound should be used but the best procedure for purging.
According to Butler MacDonald, results with MP Purge were immediate. “There is always loss in reprocessing materials and changing over, but the new compound enabled us to go from 92% yield to 97% or higher,” Pierce says. Purging time has been reduced as well, from three to four hours down to just one hour.
As the market has normalized following the surge caused by the pandemic and associated supply chain issues, demand for these materials dropped and subsequently stabilized. But Butler MacDonald continues to do business in clear and white materials. As applications shift away from colored packaging by brands implementing design for recycling, this business could continue to grow in importance.
Related Content
Inside the Florida Recycler Gearing Up to Take on Scrap at NPE2024
Hundreds of tons of demonstration products will be created at NPE2024 next spring. Commercial Plastics Recycling strives to recycle all of it.
Read MoreFoam-Core Multilayer Blow Molding: How It’s Done
Learn here how to take advantage of new lightweighting and recycle utilization opportunities in consumer packaging, thanks to a collaboration of leaders in microcellular foaming and multilayer head design.
Read MoreNew Facility Refreshes Post-Consumer PP by Washing Out Additives, Contaminants
PureCycle prepares to scale up its novel solvent recycling approach as new facility nears completion.
Read MoreAdvanced Recycling: Beyond Pyrolysis
Consumer-product brand owners increasingly see advanced chemical recycling as a necessary complement to mechanical recycling if they are to meet ambitious goals for a circular economy in the next decade. Dozens of technology providers are developing new technologies to overcome the limitations of existing pyrolysis methods and to commercialize various alternative approaches to chemical recycling of plastics.
Read MoreRead Next
People 4.0 – How to Get Buy-In from Your Staff for Industry 4.0 Systems
Implementing a production monitoring system as the foundation of a ‘smart factory’ is about integrating people with new technology as much as it is about integrating machines and computers. Here are tips from a company that has gone through the process.
Read MoreTroubleshooting Screw and Barrel Wear in Extrusion
Extruder screws and barrels will wear over time. If you are seeing a reduction in specific rate and higher discharge temperatures, wear is the likely culprit.
Read More