Additive Supplier, Film Processor Get Grant to Advance Multilayer Film Recycling
Interface Polymers and Flexipol awarded $1 million+ grant to provide fully recyclable LDPE multilayer packaging.
UK-based Interface Polymers Ltd. and flexible packaging manufacturer Flexipol Ltd. have jointly won funding through a competition run by UKRI’s Smart Sustainable Plastic Packaging challenge. The $1.07 million grant will finance the 24-month collaborative project, titled Recycle Ready multilayer barrier plastic packaging films, to provide fully recyclable LDPE multilayer packaging, suitable for upcycling into high value applications.
The development project brings together Interface Polymers’ internationally patented and proven surface functionality Polarfin additive technology, which overcomes inherent molecular level non-compatibility between polyolefins to enable them to be recycled; and Flexipol’s film technology expertise and flexible packaging manufacturing capabilities.
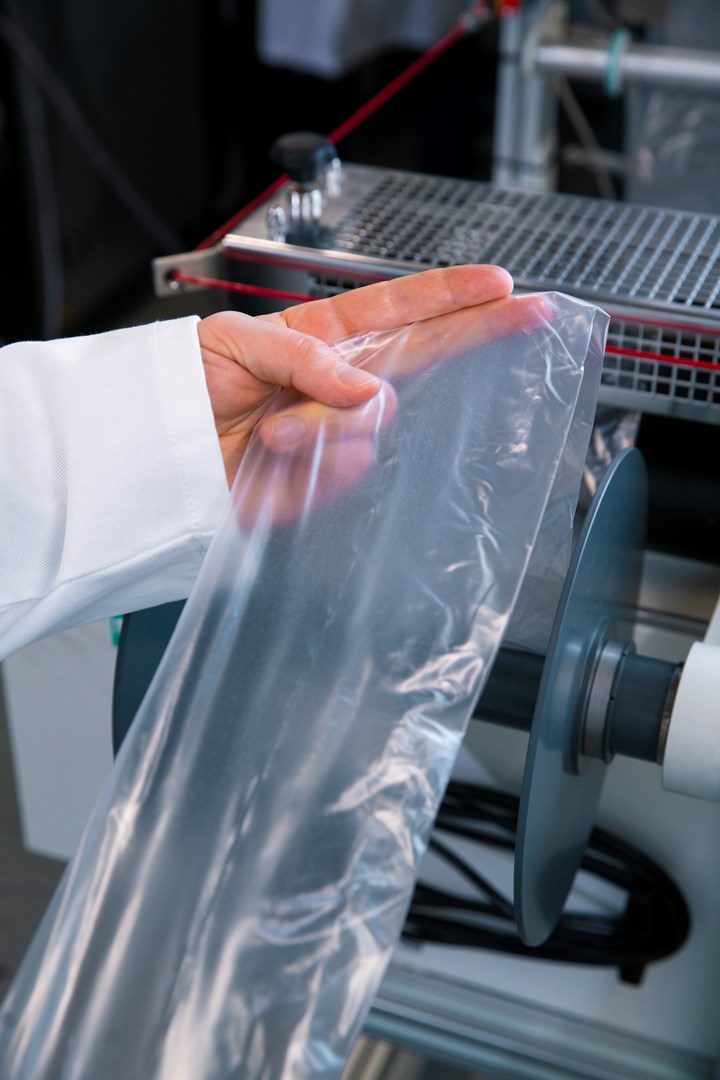
Using Interface Polymers’ compatibility-enabling di-block copolymer additive, the project is looking to build in recyclability as an integral part of originally manufactured multilayer domestic and commercial packaging product formulations that can be viably scaled up. The aim is to provide a new range of “recycle ready” multilayer packaging with a recyclability classification that will allow the waste to be collected and 100% reclaimed via existing pure stream reprocessing centers instead of being incinerated or sent to a landfill.
The aim of the project is to offer the packaging industry fully scalable alternative LDPE multilayer barrier films for the commercial production of food-approved multilayer flexible packaging that can be repeatedly recycled using existing pure plastic waste streams sorting and separation processing plants. Additionally, the project team is looking to validate that recycle ready multibarrier layer packaging can enhance product performance when reprocessed with either virgin or recycled materials to produce high value upcycled products.
According to Interface Polymers, this is expected to be achievable based on test results from previous mixed plastic recycling R & D projects that proved their Polarfin di-block additive acts like a toughening agent, providing as good, if not better, mechanical properties than the original 100% virgin polymer resin formulation, even if the same materials is repeatedly recycled.
Since the start of Interface Polymers back in 2016, several R & D projects have been commercialized and Polarfin additives are now providing compatibility and enhanced surface functionality for both virgin and recycled mixed plastic thermoplastic packaging (primarily polyolefin/ nylon/polystyrene/ EVOH). A key recycling R & D project in 2019 was also Innovate UK funded by an Innovation grant. From the R & D work successfully completed by Interface Polymers on this previous recycling project, a di-block additive that enables high value recycling of multilayer mixed plastic flexible packaging was developed which succeeded in changing surface functionality such that the different polymer chains in recycled mixed plastic no longer repelled each other and created voids and inherent weakness, but bonded together and could be used in added value upcycling applications.
This latest UKRI grant funded project will use key additive parameters from the successful 2019 mixed plastic recycling project, taking things to the next logical stage; this time the collaboration project team is looking to include Polarfin di-block additive technology in the formulation of originally manufactured packaging. The Recycle Ready project is initially targeting multi-layer PE and nylon food packaging vacuum bags and thermoplastic films.
The food packaging sector was selected for the project for three reasons explains Tom Mason, Flexipol’s innovation manager, “Firstly, producers and retailers know the performance benefits of multibarrier layer plastic film packaging, such as keeping foods fresher and providing a longer shelf life, that monofilm packaging simply cannot provide to the same extent. Secondly, the sector is well served by the existing recycling infrastructure currently operating across the UK. Thirdly, Flexipol has well established supply chain links with both recycling and packaging companies.”
In addition to the film qualification and production scale up of the new range of Ready Recycle multilayer packaging products, Flexipol will be working with established bulk food processors. This ensures that the entire value chain is included in the project, from packaging production, food product packaging and packaged food processing, to post use waste packaging collection and washing for recycling. The longer term objective is to leverage solutions coming out of this project into other multilayer barrier film packaging sectors using alternative polymers, such as PP, PET, EVOH and nylon..
Related Content
Graphene-Enhanced Stretch Film Billed as 'World First'
Thinner, stronger films to be commercialized by Brazil’s Packseven in August.
Read MoreBASF to Purchase Pyrolysis Oil Produced From Waste Plastics
Agreement with Arcus Greencycling GMBH anticipates a volume of 100,000 ton/yr.
Read MoreMasterbatches Reduce Gloss in PLA and PETG 3D Printed Products
Insight Polymers & Compounding’s two low-gloss additive masterbatches shown to boost appearance of 3D printed objects.
Read MoreSurface-Activating Primer for Polyolefins and Fluoropolymers
XlynX Materials’ PlastiLynx is designed for use with low-surface-energy polymers for improved bonding and printing.
Read MoreRead Next
Beyond Prototypes: 8 Ways the Plastics Industry Is Using 3D Printing
Plastics processors are finding applications for 3D printing around the plant and across the supply chain. Here are 8 examples to look for at NPE2024.
Read MoreRecycling Partners Collaborate to Eliminate Production Scrap Waste at NPE2024
A collaboration between show organizer PLASTICS, recycler CPR and size reduction experts WEIMA and Conair will seek to recover and recycle 100% of the parts produced at the show.
Read MorePeople 4.0 – How to Get Buy-In from Your Staff for Industry 4.0 Systems
Implementing a production monitoring system as the foundation of a ‘smart factory’ is about integrating people with new technology as much as it is about integrating machines and computers. Here are tips from a company that has gone through the process.
Read More