In-Line Proofing System for Resin Distribution
Wireless RFID system said to simplify and error-proof resin distribution.
Conair’s new wireless RFID line-proofing technology simplifies and error-proofs resin distribution by translating source/destination connections from the conveying control and HMI into operator instructions guided by color-changing LEDs on the resin selection tabletop. Other key features of this easy-to-use system include an LED-guided line purging option and full compatibility with Conair’s evolving Wave Conveying technology.
The new RFID line proofing system works with Conair’s recently introduced SmartFLX conveying control and an RFID-capable Resin Selection System (RSS) table. Each material port on the modified RSS table connects, via a fantail assembly, to a specific resin supply and is associated with an RFID antenna that is protected from damage beneath the RSS tabletop. All resin sources, along with their RSS ports and unique RFID antenna addresses, are tracked in the material source/destination database in the SmartFLX control.
Above the RSS table, the flex tubes to destination receivers are equipped with steel connection handles that contain and protect uniquely coded RFID chips, whose addresses are associated with destination receivers and stored in the SmartFLX database. Wireless signals between the flex-tube RFID chip and the antenna at each RSS port are used by the SmartFLX control to proof each connection.
When an operator initiates a material change using the RSS table, the SmartFLX control consults the material/source/destination database to identify one or more RSS port(s) linked to the correct resin source, as well as one or more flex tube(s) linked to the desired destination. Then, as these correct connection(s) are displayed on the HMI screen, the control translates them into light-guided instructions using LEDs embedded in the surface of the RSS table.
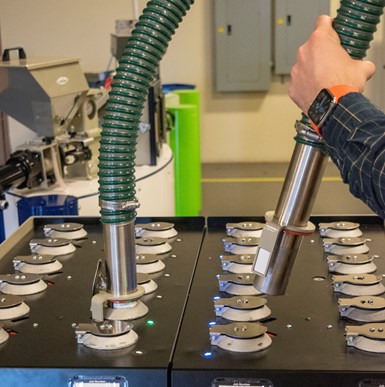
A correct flex tube (destination) is indicated by a flashing yellow LED, indicating that it should be unplugged from its current position and moved to a new RSS port (source) identified by a flashing blue LED. To make the connection, the operator moves the flex tube end to the indicated RSS port, then connects the tube into the port, aligning the tube’s RFID-equipped handle with the tabletop slot next to the port. Inserting the tube handle into this slot aligns its RFID chip with the port’s RFID antenna, enabling the SmartFLX control to proof the connection. The tabletop LED flashes green to indicate a good connection, after which the SmartFLX control unlocks the destination receiver and initiates the conveying cycle.
Should an operator attempt to connect either the wrong tube or port, the tabletop LED at that port flashes red, indicating an error, while the LED for the correct port continues to flash blue until the correct tube/port connection is made. For added reference, the SmartFLX HMI continues to display the correct tube/port combinations as well, using numbers that correspond to the markings on flex tube handles and RSS port positions.
Conveying systems often have a combination of non-purged and purged lines. Lines that are not automatically purged (e.g., cleaned with an air-only purge cycle that flushes all remaining resin to the receiver) may leave behind some resin that can be picked up, contaminating the resin in the next conveying cycle. Many line-proofing systems rely on operators to recognize this risk and perform a manual line purge when needed. But if busy operators forget, resin contamination can occur.
To error-proof the cleaning of non-purged lines and eliminate any resin contamination risk, Conair’s RFID line proofing system introduces “Clean Cycle.” This process combines a filtered purge-air source/port on the RSS table with color-coded LED indicators that guide operators through the correct purging sequence. It is managed by the SmartFLX control, which knows the purge status of each source and automatically adds the Clean Cycle process whenever resin is conveyed from a non-purged source.
Here’s how the Clean Cycle process works: As soon as an operator completes a material conveying cycle from a non-purged source, the LED at that RSS port switches from flashing green to flashing yellow—indicating that the flex tube needs to be moved—while the LED for the Clean Cycle port flashes blue. When the flex tube is connected to the Clean Cycle port, the purging connection is proofed, its LED flashes green, the destination receiver is unlocked, and the line is completely purged – any remaining resin is pushed through to the receiver.
Related Content
Wisconsin Firms Unite in Battle Against Covid
Teel Plastics opened new plant in record time, partnering with AEC & Aqua Poly Equipment Co. to expand production of swab sticks to fight pandemic.
Read MoreMobile Sanitary IBC Unloading and Conveying System
Transfers contamination-sensitive bulk solid materials from IBCs to downstream processes, dust-free.
Read MoreRedesigned Rotary Level Indicator
Red enclosure now rotates once installed to help ensure conduit entries are always pointed toward the ground, mitigating the risk of moisture damaging internal components.
Read MoreHow to Effectively Reduce Costs with Smart Auxiliaries Technology
As drying, blending and conveying technologies grow more sophisticated, they offer processors great opportunities to reduce cost through better energy efficiency, smaller equipment footprints, reduced scrap and quicker changeovers. Increased throughput and better utilization of primary processing equipment and manpower are the results.
Read MoreRead Next
How Polymer Melts in Single-Screw Extruders
Understanding how polymer melts in a single-screw extruder could help you optimize your screw design to eliminate defect-causing solid polymer fragments.
Read MoreWhy (and What) You Need to Dry
Other than polyolefins, almost every other polymer exhibits some level of polarity and therefore can absorb a certain amount of moisture from the atmosphere. Here’s a look at some of these materials, and what needs to be done to dry them.
Read MoreLead the Conversation, Change the Conversation
Coverage of single-use plastics can be both misleading and demoralizing. Here are 10 tips for changing the perception of the plastics industry at your company and in your community.
Read More