Share
Read Next
Plastics processors have experienced an array of challenges over the last few years. Materials shortages, rising energy prices, the lack of skilled labor – they’ve all converged to pinch margins in ways we’ve never experienced before. This perfect storm is forcing companies to reexamine their production processes to find new efficiencies to reduce costs while increasing throughput. Today, there are pathways to running a more profitable plant by implementing more advanced auxiliaries that allow better utilization of primary processing equipment, more consistent quality, quicker changeovers, and best of all, reduced cost of operations. We’ll get to that in a moment.
In general, while the cost of resins finally stabilized this year, though at historically high prices, there are still supply chain issues in some resin grades, while future expectations come into question with the growing cost of polymer feedstocks. And, then there’s the rising cost of energy which is real concern when it comes to the bottom line. According to Statista, the average retail cost of electricity rose from 7.18 cents per kilowatt hour in 2021 to 8.45 last year with, and with dramatic differences in rates from state to state. So, for many plants, the most obvious cost reduction target will be reducing energy consumption. But there are many other sources of waste in most processing plants that also contribute significantly to shrinking the bottom line.
Moretto is a well-known and established provider of a wide range of auxiliary equipment with a global reputation for advanced technology in auxiliaries and overall processing systems. Here are some of their suggestions on how to run a more efficient plastics processing plant by choosing the right drying, blending and conveying technologies.
Reducing Energy Costs
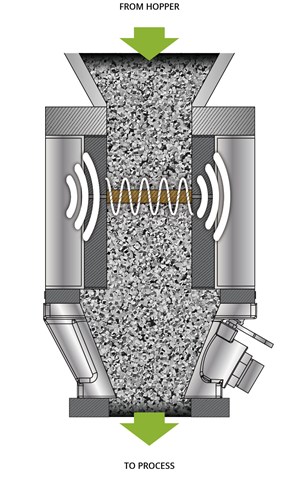
Moisture Meter works by passing electromagnetic waves through the resin and reading the exit wave patterns which precisely indicate the true moisture content of the material.
For many processors, the elephant in the room is their electricity bill. For auxiliary equipment that points directly at resin dryers as a good place to begin assessing cost reduction opportunities. That cost will certainly not go away, but newer drying technologies can go a very long way in bringing energy costs under much better control.
A primary challenge of drying is understanding the moisture content of the incoming resin pellets. This will vary based on resin storage methods, ambient plant conditions, and even the season of the year. Supplier drying recommendations often can’t account for that variability so the best-guess method is frequently used to determine drying time, which can often can lead to under- or over-drying. The former can cause quality problems. The latter can too, and it absolutely wastes energy.
Today, most dryers have the ability to measure the moisture content of the dryer air, which is a major improvement. But a more efficient and accurate solution is to measure the moisture content of the resin itself.
Moretto has a product that does that, called Moisture Meter, that works by passing electromagnetic waves through the resin and reading the exit wave patterns which precisely indicate the true moisture content of the resin. The main benefits to this process is automatic early warning detection so you are aware of potential issues before they happen; and process verification so you can actually track back in time what occurred hours ago, days ago, even months ago in the event you are challenged to prove your drying process was accurate for that specific batch.
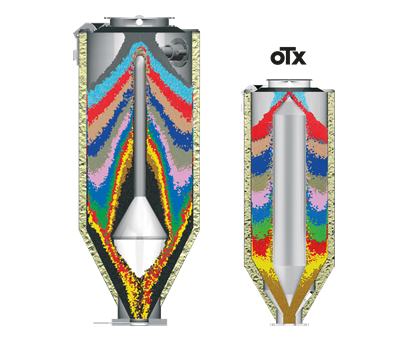
With conventional drying technology material can flow unevenly through the hopper resulting in variable resonance time. OTX hoppers use a center core that smooths resin movement with air delivery located low in the vessel for improved cone drying.
Consistency in the drying hopper is also important for the sake of quality, which means all material must have the same access to dry air and resonance time. With many traditional designs, uneven pockets of material can form due to poor flow through the hopper which results in variability of exposure to dry air and stagnant material accumulation. Moretto has an advanced technology called OTX (Original Thermal eXchanger) in their drying hoppers that is designed to deliver optimized mass flow of materials for highly predictable resin drying. More compact than traditional dryers (think space utilization), the design uses a center core that smooths resin movement with air delivery located low in the vessel for improved cone drying. Because the material comes out of the dryer uniformly “pre-heated,” it is often possible to run injection molding and extrusion processes at lower temperatures on the press, further saving on energy costs.

Eureka Plus provides closed-loop drying control for accurate and consistent resin dehumidification regardless of process variables.
By integrating these technologies with a system Moretto calls Eureka Plus, it is now possible to have closed-loop drying control the provides desired resin dehumidification regardless of process variables or human errors. Removing the guesswork from drying this way assures that extremely consistent material is delivered to a molding or extrusion process. And, it typically reduces energy consumption by some 40% compared to traditional drying systems.
More Efficient Material Use with Precision Blending
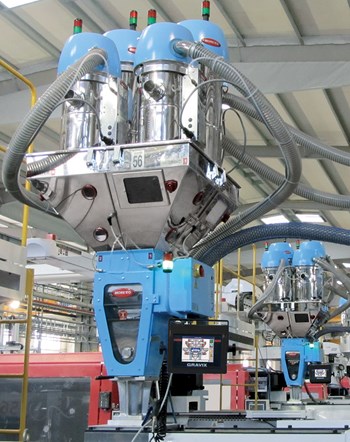
Moretto GRAVIX blender
An often-underappreciated component of variability in molding and extrusion processes is the accuracy and consistency of blending. That obviously speaks to quality concerns, but there can be significant cost ramifications as well. Material input variability in molding or extrusion processes can lead to inconsistent part appearance or mechanical properties, excessive scrap, and even compromised process speeds.
Some plastics processors just live with blending variability by overdosing colorants or other expensive additives on a “just-in-case” basis. But today’s best gravimetric blending technology can eliminate this compromise with the ability to dose and mix to astonishing levels of accuracy which helps reign in downstream problems related to material inconsistency.
For example, Moretto’s GRAVIX multi-material blenders use advanced gravimetric technology and easy-to-use touchscreen control for intuitive management of the machine and for recipe storage. The blenders have a remarkably fast “Double Eyelid” shutter system (see video above) with a reaction speed of 25 milliseconds which ensures an extreme level of accuracy and throughput, with material weight variance as small as 0.1%, even when there are differences in the bulk densities of materials. The blender measures each component of the mix 100 times per second which means it can control the weight of any resin dose to a single pellet and additive components much more precisely than other technologies. Moreover, it has a vibration isolation system that prevents measuring accuracy from being affected by any other equipment in the system.
Another important aspect of blenders to the bottom line is how quickly they can be changed over from job to job. The GRAVIX blenders have easily removable hoppers that can simply be exchanged for new jobs allowing cleanout to happen offline. Several other easy-clean features contribute to quick job changeover that can be accomplished in a few minutes.
More Cost Efficient Conveying that is Kinder to Your Materials
Central conveying system problems can also raise significant cost concerns. For one thing, they can be a source of heat loss in materials after drying. They can also waste energy by generating excessively high vacuum pressures, and sometimes in lines that are not conveying any material at all. Moreover, excessively high conveying speeds can damage materials, leaving dust and angel hair behind that must be cleaned out, and wear out conveying line elbows or other areas where pellets are impacting lines at high velocity.
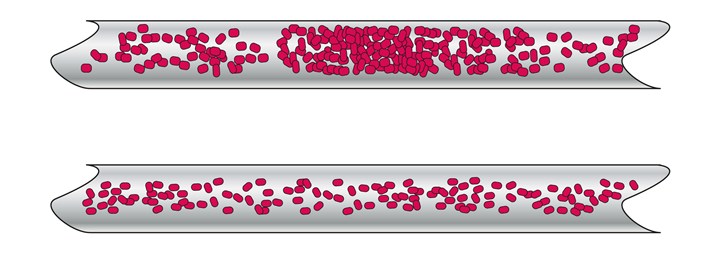
Moretto’s KruiseKontrol automatically manages material speed in a conveying system to reduce angel hair and dust as well material and line stresses due to friction and pipeline wear.
Moretto uses a technology called KruiseKontrol (KK) which automatically manages material speed based on the specific material being used. It uses just enough pressure to meet the throughput requirements, but no more that would contribute to excessive material or line damage.
On top of KK Moretto has the Flowmatik air control system for adaptive air flow management to OTX hoppers. The air control system automatically assures optimum flow to each hopper in the system. There are several important benefits to managing air flow in this way:
- Eliminates manual valves and manual balancing of airflow in multi-hopper systems.
- Assures lowest possible energy consumption since excess airflow is eliminated.
- Eliminates stress on resin from over-drying, even in reduced or stopped production.
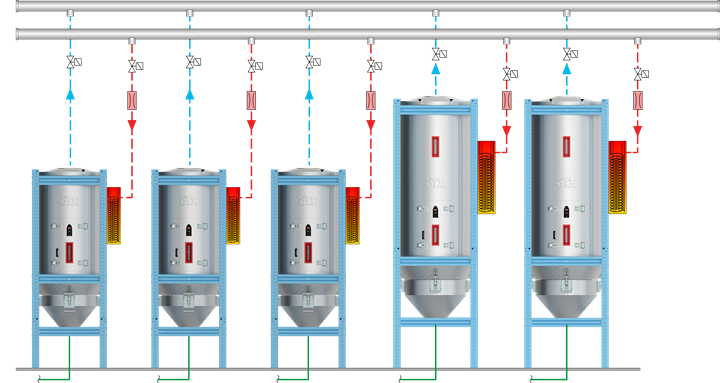
Moretto’s Flowmatik control system automatically assures optimum flow to each hopper in the system.
The system works by placing air-flow sensors on each hopper’s air inlet. The control uses this data to activate motorized valves on the dry air inlet and moist air outlet of each hopper to adaptively regulate air flow. As air flow is modulated, drying heat volume is naturally modulated, again saving energy. To set up, users simply input material resin type and throughput in lbs. or kg. per hour for each hopper, and the control does the rest.
Bottom line, the automated air control system only applies vacuum to where it’s needed, when it is needed, and at no more than the required pressure. That saves energy throughout the system, reduces maintenance costs, speeds changeover, and requires less attendant labor to keep the system running properly.
Tending to your plant-wide drying needs in one sophisticated system like Eureka Plus can address all your concerns about resin dehumidification. But what about the rest of your systems? Can cooling, blending, material delivery and distribution be addressed in a similar manner? Yes. By securing equipment with smart sensor and control systems, precise and fast electromechanical components, and basic communication capabilities, all of your auxiliary systems be can integrated into a common system that will lower operating costs, reduce changeover times, and consistently deliver high-quality product.
For more information please visit Moretto.com.