Pelletizing System for Engineered Resins and Recycled Materials for Optical Molding
NPE2024: Matsui America is introducing the Raptor 22 pelletizing system.
Matsui America is introducing the Raptor22 pelletizing system. According to Matsui, the system enables the reuse of engineered resins in critical molding applications — a use case which has not been possible with currently available technology.
The Raptor22 has a proprietary screw design that prevents carbonization and eliminates material shear heat. It also has a carbide rotating blade that cuts the hot material strands at high speed, producing round, teardrop-shaped pellets. Finally, a vacuum-based conveying system cools the material as it is being transported to a cyclone receiver.
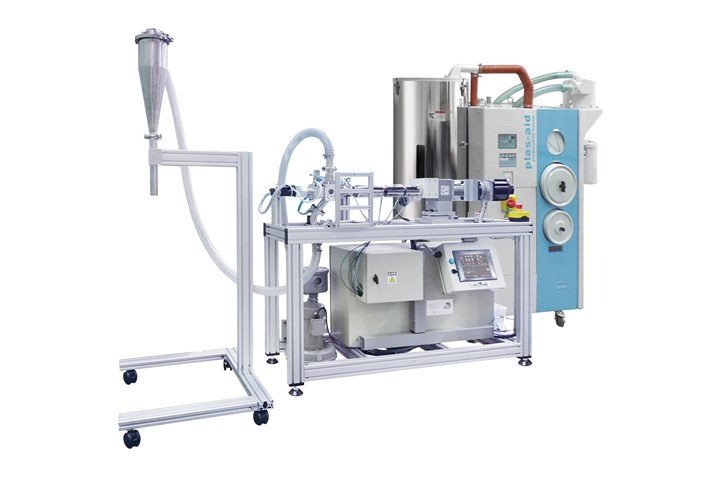
Raptor 22 is designed to facilitate reuse of engineered resins and recycled materials. Source: Matsui
The use of a Raptor 22 pelletizing system makes it possible to process and reuse highly engineered recycled materials like LCP, COC, COP, PC, PA46 and PEEK, among others. A system configuration including the integration of Matsui’s recently introduced molding defect elimination products with the Raptor enables the use of recycled materials, even for optical or cosmetically critical molding applications. Matsui’s static eliminator, for example, removes material in powder form, eliminating black and white spots, burning and uneven blending and weighting.
“The Raptor 22 pelletizing system helps our customers to save significant material and operating costs with the ability to recycle and reuse extremely expensive materials like LCP, PEEK, among others. Additionally, our technology contributes to sustainable plastics use by reusing some of these materials instead of sending them to a landfill,” says Mike Kott, GM of business development at Matsui America.
The Raptor 22 produces clean and uniform pellets, with very little deterioration of physical material properties. It also features intuitive control technology and HMI, as well as an energy-efficient design.
Related Content
-
Educating the Next Generation of Plastics Professionals
These schools and local industry are working together to close the workforce gap in the plastics industry by offering hefty plastics curricula and training programs for degree-seeking students as well as current plastics employees looking to upskill.
-
Impacts of Auto’s Switch to Sustainability
Of all the trends you'll see at NPE2024, this one is BIG. Not only is the auto industry transitioning to electrification but there are concerted efforts to modify the materials used, especially polymers, for interior applications.
-
Use AI, Machine Learning to Take Variability Out of Manufacturing
Variability has always created insurmountable challenges for manufacturers. However, in the last decade, impact has been more painful due to a lack of experienced workforce. By leveraging technological advancements, particularly in AI, manufacturers can gain a transformative competitive advantage in both cost reduction and workforce development.