Educating the Next Generation of Plastics Professionals
These schools and local industry are working together to close the workforce gap in the plastics industry by offering hefty plastics curricula and training programs for degree-seeking students as well as current plastics employees looking to upskill.
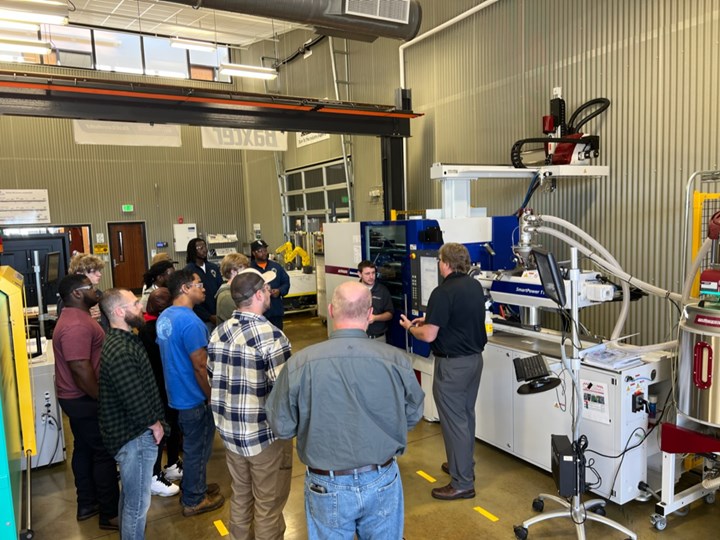
SUSCC’s latest equipment addition is an industry 4.0 cell built around a SmartPower120 injection molding machine and robot. Photo Credit: Wittmann
A satellite campus of the larger university in State College — Penn State Erie, The Behrend College — is just over a 3-hour drive northwest of the home of the Nittany Lions. Southern Union State Community College (SUSCC) in Opelika, Alabama, meanwhile, is roughly 10 miles from Auburn, Alabama, and Auburn University. Both schools might be overshadowed by these larger better-known institutions, but they also both boast outsized plastics curricula and training programs, including sizable labs for hands-on studies that attract the interest of large national and multinational manufacturing firms seeking to hire ready-on-day-one plastics professionals.
“For students that want jobs, job placement is 100%,” explains Bill Clifton, plastics engineering and mechatronics instructor at SUSCC. “I mean, it’s every student that comes through.”
At Penn State Behrend, just over 700 miles north of Opelika as the crow flies, the placement stats are equally gaudy. “Well, by the time plastics students graduate, if they don’t have a job, it’s because they haven’t been trying very hard,” jokes Brad Johnson, the director of the Plastics Training Academy at Behrend. Whether the final placement percentage is actually perfect, Johnson’s mathematics background gives him pause. “Some of the faculty say placement is 100%,” Johnson explains. “I don’t say 100%, as I teach the statistics class. It could be 100% — there’s always a straggler.”
Todd Shackett, SUSCC president, who came to that position after plastics processing and management stints with the likes of GM, Becton Dickinson and Baxter, backs Clifton’s placement assertion. “Our students usually get hired well before they graduate,” Shackett says. “The best opportunity for the company and the student is to get a work-based internship or apprenticeship, because the ones that do that have their company dialed in, and the company has its employee locked in. We have a lot of companies come through looking for graduates, and if you ask the students, most of them already have a plan.”
Seeking Pre-Pandemic Enrollment
Coming out of the pandemic, which hampered the student-outreach activities of both schools, Penn State Behrend and SUSCC are seeking to get back to pre-COVID-19 enrollment and graduation levels. They do so at the same time that the broader plastics industry struggles to slot employees into all manner of positions — from material handling and process techs to designers and process engineers.
Penn State Behrend has just one of four accredited Plastics Engineering technology programs in the U.S., providing undergraduates the chance to pursue a bachelor’s degree in plastics engineering technology. In addition to classroom work, Penn State Behrend students have access to the 10,500-square-foot Jack Burke Research and Economic Development Center, which includes 15 injection molding machines ranging in clamp force from 11 to 220 tons, as well as blow molding, extrusion, thermoforming and compression molding machinery.
SUSCC offers an associate’s degree in applied science degree in plastics engineering technology, as part of its advanced manufacturing associate of applied science, which takes five full semesters, with many companies providing tuition reimbursement. The program also provides stackable short-term certificates in basic molding, mold process technician and mold setter. The company’s lab covers more than 5,000 square feet, with seven injection molding machines ranging in clamp force from 55 to 110 tons. There are all-electric, hybrid and hydraulic machines from Engel, Nissei, Arburg and Shibaura, with the newest press being a 110-ton SmartPower at the heart of an industry 4.0 work cell provided by Wittmann.
In addition to providing a degree path to younger students, both Behrend and SUSCC offer training to current plastics professionals. At SUSCC, the company’s sizable lab is also utilized by injection molding training and technology supplier RJG as a Master Molder training outpost in the booming southeast. At Behrend, it also offers seminars and training programs for plastics workers, most recently adding an automation lab to its hands-on equipment offerings. In Alabama, Clifton has been certified by RJG to provide Master Molder training, making him qualified to pass that credential to class participants.
“Noncredit training is an area that we’ve seen the most growth,” SUSCC’s Clifton says. “That’s one way we support a lot of the local companies. Not only with our recent graduates, but for them to take advantage of noncredit training, helping to upskill their current employees.”
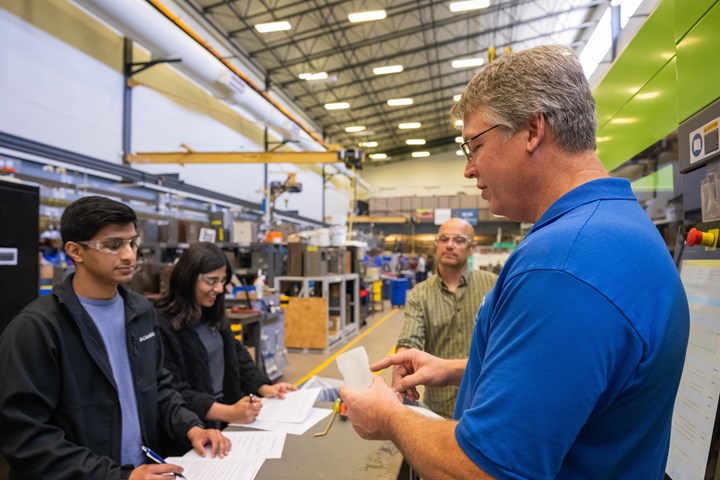
Brad Johnson leads instruction at Penn State Behrend’s plastics lab. Photo Credit: Penn State Behrend
Manufacturing and the Great Resignation
Plastics specifically and manufacturing in general was not untouched by the “Great Resignation” that accompanied the pandemic. In a January 2024 report entitled “Understanding America’s Labor Shortage,” the U.S. Chamber of Commerce found that labor force participation still has not returned to pre-pandemic levels. In fact, the report stated that if labor force participation rates were back to February 2020 levels, immediately prior to the world shutting down, there would be an additional 2.2 million people in the workforce.
Of the five major industries tracked from January 2021 to December 2023, durable goods had the second lowest quit rate (1.7%), with only financial activities coming in lower (1.4%), while the highest rate was found in leisure/hospitality (4.1%). The Chamber does report, however, that hiring rates have continuously outpaced quit rates, so the gap is closing.
The manufacturing industry lost roughly 1.4 million jobs in the pandemic. “While durable goods manufacturing has seen a more substantial recovery compared to nondurable goods manufacturing, as of August 2023, a gap persists, with 616,000 total manufacturing job openings yet to be filled,” the report stated.
Assessing Industry’s Needs
As these schools and the local industry work together to close that gap, they maintain an ongoing dialog to make sure students graduating from the program, or current workers that need additional skills, can find the course and lab work they need.
“Each one of our programs has advisory committee members from local companies,” Clifton says, “and they help to advise on the curriculum, and as we need new equipment, they advocate for that. They’ll say, ‘This is what we need to be looking for down the road.’ They help shape the program.”
Ultimately, the students will be joining the local business community, and SUSCC wants to ensure they’re going to be a good fit. “We want our graduates to be relevant,” Shackett says. “I worked in the era where technicians learned on the job. They would push a button because the guy told them to push the button when they saw this condition. You need to know what’s happening after you push the button; why am I pushing it?’”
In Pennsylvania, Behrend maintains an industrial advisory board to help keep its curriculum and equipment current with the present needs of the plastics sector. “We have a lot of alums that are running places now,” Johnson says. “We’re able to have a lot of them come back and tell us what we need to add, and what we’re not doing enough of.”
To that end, the school recently created a polymer engineering science degree, as companies in the field sought graduates with more of a material testing and characterization background.
Opening Their Doors
The biggest recruiting tool for both schools was unavailable to them for much of the last four years: open houses. “Normally when we have open houses here, that’s when we get a lot of students and interest,” Johnson says of Behrend. “They not only see the lab but we have students working those open houses. The incoming kids don’t want to talk to faculty; they want to talk to the students, and the parents want to talk to faculty.”
At SUSCC, recruitment starts as early as middle school. “Up until the pandemic, we were doing manufacturing days here and we’d run 4,000 or 5,000 students through here in two days.” Getting those students, and their parents, in the door is key to educating the broader public on the opportunities in plastics and other technical degrees available at SUSCC. “I would say advocacy is one of our biggest issues,” Shackett says. “They don’t know what they don’t know, and that’s what we fight every day — trying to educate students about opportunities in our technical programs.”
Clifton says that for the students who do find out what they don’t know about the plastics industry, the impact can be dramatic, as he lists all the various automotive OEMs, brand owners and more who have stopped off recently in Opelika to see what SUSCC is teaching. “The students that get into the program,” Clifton says. “it’s life changing for them. They come from all different walks of life — they might be working at Zaxby’s making chicken fingers for $10/hr, and then they get into an internship and are making in the $20/hr range.”
The individual economic impact on the students extends to the broader local economy, as companies consider the ability to hire skilled workers a key box to check when they seek to open a new operation. “When companies come to our facility, they see how we can help support them and their training needs, and it gives our economic developers a huge step up compared to other areas,” Shackett says.
By the time a company visits a potential site, it already knows if the community has good schools, hospitals and highway access, as well as enough water and electricity infrastructure. “Those are all just the price of consideration,” Shackett explains. “What they really want to know is, ‘Where am I getting my skilled employees.’”
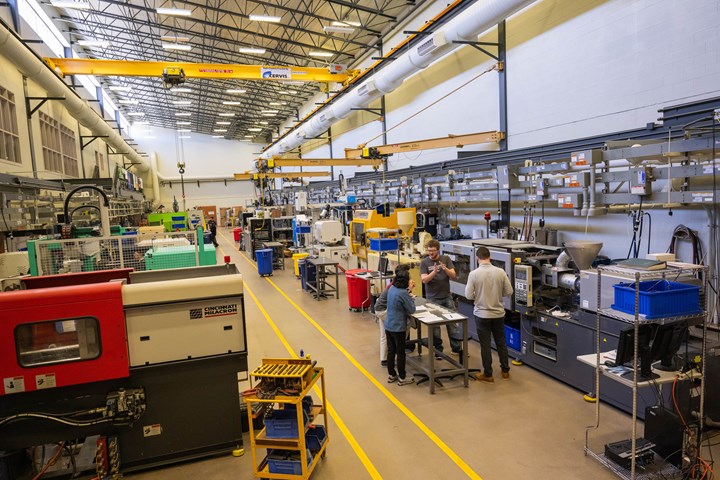
Penn State Behrend’s 10,500-sq-ft Jack Burke Research and Economic Development Center features 15 injection molding machines ranging in clamp force from 11 to 220 tons. Photo Credit: Penn State Behrend
Related Content
TAPPI to Provide Film Education Program at PTXPO 2023
Second-ever PTXPO will feature a robust education program on flexible film, with more technical programming in the works.
Read MoreThe Cost of High Employee Turnover in Injection Molding: Why Retention Matters
Starting in molding in 1993 and clocking in for nearly every job on the floor over the intervening decades, I’ve seen all sides of the hiring, training and retention process in the industry. Here are my thoughts on how to keep your most important asset — your people.
Read MoreSilicone Elastomer Course Returns
After completely filling the classroom last year, the Silicone Elastomers Technology and Fabrication course returns to Pomona, Calif. Jan. 31-Feb. 3.
Read MoreKraussMaffei and NIAR Propel Injection Molded Thermoplastic Composites
The maker of plastics processing equipment has placed a machine and an injection molding expert in NIAR’s ATLAS lab in Wichita, Kansas, to help molding, composites and aerospace take off.
Read MoreRead Next
What Processors Are Doing To Bridge the Skills Gap
Seasoned technicians are leaving, and replacing them with youngsters is a challenge. But some processors have taken dramatic initiatives to change how young people think about manufacturing and are bringing the next generation into the fold.
Read MorePlastics Technical Conference Returns to Penn State Behrend
Returning last June after a pandemic hiatus, Penn State Behrend (Erie, Penn.) will once again host its Innovation and Emerging Plastics Technologies Conference.
Read MoreHow Polymer Melts in Single-Screw Extruders
Understanding how polymer melts in a single-screw extruder could help you optimize your screw design to eliminate defect-causing solid polymer fragments.
Read More