Rapid Robotics Partners With Yaskawa Motoman
Through a new partnership with Yaskawa Motoman, the San Francisco-based robotic workforce company will apply its rapid deployment, machine vision and artificial intelligence model to industrial applications.
Rapid Robotics announced a collaboration with Yaskawa America Inc.’s Motoman Robotics division that will bring industrial capabilities to Rapid Robotics’ Rapid Machine Operator (RMO). Rapid is now integrated with the entire Yaskawa robotics portfolio, allowing it to deliver more speed and higher payloads for a more diverse range of needs.
Rapid says the deal brings its advanced computer vision, artificial intelligence and instinctive learning with as-a-service characteristics including cloud connectivity, monthly leasing and 24/7 support to bear with Yaskawa’s robot portfolio.
Rapid Robotics fast deployment speed is linked to its modular approach to work cell design. A key feature of that is the mobile robot pedestal with modular fixturing. The mobile pedestal gives this light industrial arm the same flexibility as Rapid Robotics’ collaborative robot (cobot) since the pedestal can be moved or reconfigured and then re-locked into place by a single person.
Rapid said its advanced vision systems and AI allow Yaskawa’s full line of robotic manipulators to shift repetitive or dangerous tasks away from humans. Historically, industrial robotic arms can be more challenging and time-consuming to deploy than cobots, especially outside of mass production environments, but Rapid says its industrial RMO offers the flexibility of a cobot while meeting all mandatory safety measures for traditional industrials, as well as the performance they provide with regards to payload, speed and reach.
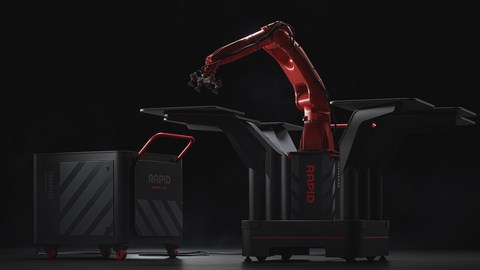
Rapid Robotics’ mobile robot pedestal adds flexibility via modular fixturing.
Photo Credit: Rapid Robotics
Related Content
-
Drones and Injection Molding Ready for Takeoff
Drones and unmanned aerial vehicles (UAV) are approaching an inflection point where their production volumes — and functionality — will increasingly point to injection molding.
-
A Cost Saving Modular Approach to Resin Drying Automation
Whether implementing a moisture-sensing closed-loop system for a single dryer, or automating an entire plant, technology is available to take the guesswork and worry out of resin drying. Using a modular approach allows processors to start simple and build more capabilities over time.
-
Real-Time Production Monitoring as Automation
As an injection molder, Windmill Plastics sought an economical production monitoring system that could help it keep tabs on its shop floor. It’s now selling the “very focused” digital supervisor it created, automating many formerly manual tasks.