A Cost Saving Modular Approach to Resin Drying Automation
Sponsored ContentWhether implementing a moisture-sensing closed-loop system for a single dryer, or automating an entire plant, technology is available to take the guesswork and worry out of resin drying. Using a modular approach allows processors to start simple and build more capabilities over time.
Share
Read Next
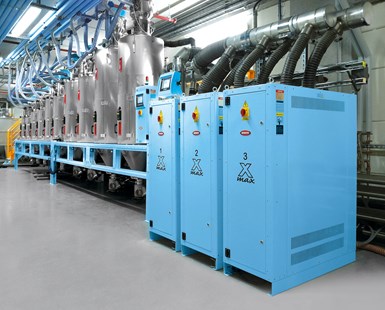
FACT: Sooner or later all plastics processors have to dry resins. Some plants dry a lot. But in all too many cases processors don’t give the same scrutiny to building efficient and consistent drying capabilities as they do to the primary molding and extruding processes in their plants.
That can be a serious oversight because drying often is the key enabler to achieving a stable molding or extrusion process. Talking about automated drying conjures the notion of reducing labor and cost. While that’s certainly true, this view misses perhaps the most important aspect of automated drying. Automation forces you to stabilize the drying process. That means more optimal and consistent material input to the primary processes, which in turn leads to more efficient and high-quality production. If you’re thinking about achieving better process controls and maximizing cost savings, it has to start with drying.
But you can’t achieve these improvements with just any drying technology. Since its foundation in 1980, Moretto S.p.A. has gained a leadership position in the resin drying space and in the production of automated auxiliary systems for the plastics processing industry. Their drying technology and design innovation is regarded as being among the world’s most sophisticated. It can be applied to a single press or an entire plant, and just about anything in between. To better understand the importance of having an effective automation plan in place, here’s Moretto’s take on the necessary components of a truly automated drying system.
Key Enabling Technologies to Automation
A primary challenge of automated drying is that it can be very difficult to know what’s really happening in the drying hopper. This knowledge, and other factors, can lead to inconsistency in the moisture content of the dried resin. There are two key enabling technologies that deal with these issues.
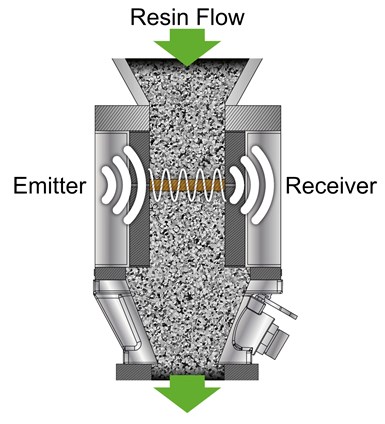
Moisture Meter works by passing electromagnetic waves through the resin and reading the exit wave patterns which precisely indicate the true moisture content of the material.
Measuring Moisture – Without the ability to automatically monitor moisture content of dried resin you have little choice but to sample material on a periodic basis and tweak the recipe, live if needed, or live with variable moisture content, or both. A smarter alternative is an inline moisture sensor that provides precise real-time feedback of actual material moisture content. Called, Moisture Meter, this sensor reads the moisture content of the resin itself, not the air
surrounding the resin. It works by passing electromagnetic waves through the resin and reading the exit wave patterns which precisely indicate the true moisture content. That data can be extremely valuable all on its own, but the biggest advantage is when the moisture sensor is integrated with a control system that self-adjusts to consistently deliver material within +/- 20 of the set dew point.
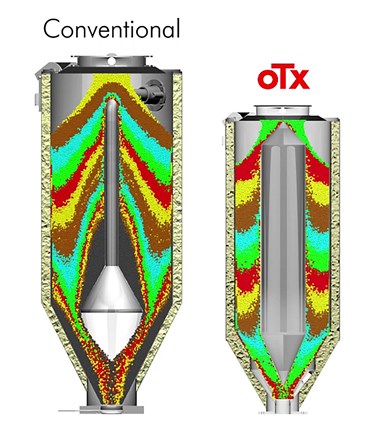
OTX hoppers use a center core that smooths resin movement with air delivery located low in the vessel for improved cone drying.
Consistency in the Hopper – To achieve consistent output all material in a dryer hopper must have the same access to dry air and residence time. Unfortunately, with many traditional designs, uneven pockets of material can form due to poor flow through the hopper which results in variability of exposure to dry air and stagnant material accumulation. Moretto has a technology called OTX (Original Thermal eXchanger) in their drying hoppers that is designed to deliver optimized mass flow of materials for highly predictable resin drying. More compact than traditional dryers (think space utilization), the design uses a center core that smooths resin movement with air delivery located low in the vessel for improved cone drying. Each hopper has a viewer control that provides drying status and temperature readout.
Bottom line, OTX combined with Moisture Meter delivers extremely consistently dried resin hour after hour, day after day.
Building System Capabilities
In terms of automation, the key point of technologies like Moisture Master and OTX is that they can render a drying process capable of high consistency under varying plant conditions. They achieve this by self-correcting for any changes in ambient conditions, material density or other factors without the need for human intervention. Now that the drying process is stabilized, further automation becomes possible with the ability to serve one or more presses, or to create a flexible drying system for either a few presses, or an entire plant.
The X-Max Modular Drying System enables drying on demand to make make drying more efficient and flexible. Click on image to view full size.
Moretto’s approach to this is with a modular system that can include 2 to 10 dryers. While not quite as simple as plug and play, that is the basic idea. It allows processors to start small and expand the system as their needs grow. It’s called the X-Max Modular Drying System which deploys single-bed zeolite desiccant dryers with dewpoints down to 85°F. An added feature is that the units require no cooling water or compressed air.
The key benefit of having interchangeable modular dryers in a system is that it enables drying on demand, meaning that any one of the drying units can be deployed on a moment’s notice to provide maximum flexibility in servicing multiple processes. This lets you, for example, pull a dryer offline to regenerate the desiccant with no change in drying system performance. It also provides the opportunity to perform routine maintenance tasks without stopping production.
The X Max dryer control is what enables processors to manage the system. A single control can manage up to 10 dryers. The control assures that ample dry air is always delivered to the drying process by sequencing regeneration and adjusting air flow as required.
The dryer control also syncs with Moretto’s Flowmatik control system for adaptive air flow management to the OTX hoppers. The air control system automatically assures optimum flow to each hopper in the system. There are several important benefits to managing air flow in this way:
- Eliminates manual valves and manual balancing of airflow in multi-hopper systems.
- Assures lowest possible energy consumption since excess airflow is eliminated.
- Eliminates stress on resin from over-drying, even in reduced or stopped production.
- Intrinsic viscosity levels are protected for improved processing.
The system works by placing air-flow sensors on each hopper’s air inlet. The control uses this data to activate motorized valves on the dry air inlet and moist air outlet of each hopper to adaptively regulate air flow. As air-flow is modulated, drying heat volume is naturally modulated, saving energy. To set up, users simply input material resin type and throughput in lbs or kg per hour for each hopper and the control does the rest.
Putting it All Together
While each of these technologies are important on their own, the true potential of automation arrives when these elements are integrated into a single system, which Moretto calls Eureka Plus.
Eureka Plus provides closed loop drying control for accurate and consistent resin dehumidification regardless of process variables.
By integrating these subsystems, Eureka Plus provides closed loop drying control for accurate and consistent resin dehumidification regardless of process variables. By automatically adjusting for actual resin moisture levels the system takes the guesswork out of resin dehumidification. Every molded or extruded part is free of excess moisture, regardless of process variables and human error. An added benefit, it typically reduces energy consumption by some 40% compared to traditional drying systems.
A typical system is specified and built in 4 steps:
- Determine required resins, throughputs, number and sizes of OTX hoppers required. The hoppers are then outfitted with heaters, air controls, moisture controls and material conveying.
- Based on hopper and throughput requirements, a selection of modular, X-MAX dryers is specified. Hoppers and dryers are joined by dry air supply and moist air return lines.
- Dry air balancing controls are added to assure precise, automatic air flow through each hopper.
- Closed loop drying control is added with the Moisture Meter system.
A major advantage of approaching automation in this fashion is that you don’t have to do everything at once. Provisions can be made in design of a system so that it is adaptable for future growth. You may want to start with just a few presses and dryers for current volume requirements in anticipation of future growth, or just to prove out the efficacy of automated drying. As your business and confidence grows, more capacity can be added as you go.
The Next Level of Automation (MOWIS)
Tending to your plant-wide drying needs in one sophisticated system like Eureka Plus can address all your concerns about resin dehumidification. But what about the rest of your systems? Can cooling, blending, material delivery and distribution be addressed in a similar manner? Yes. By securing equipment equipped with basic communication capabilities, all of your auxiliary systems, including Eureka Plus can be integrated into a common computer network.
Moretto’s MOWIS system monitors and can allow control of everything from simple additive feeders, to heat transfer systems to material delivery
Moretto’s MOWIS system is a supervisory network that reaches out to monitor and allow control of everything from simple additive feeders, to heat transfer systems to material delivery. From a computer, located virtually anywhere, your entire plant is visible and manipulable for total control. In fact, most Eureka Plus users have opted to add this capability when installing their system, further adding to their confidence in their drying assurance and preparing for additional growth that includes a wide range of auxiliary support.
As the scope of drying and plant automation gets larger, processors are well served by picking an expert partner that can help assess all your current drying requirements and plan for future requirements in order to get the best efficiency now, and still be able to grow with future demand. That includes the ability to integrate with existing plant equipment, design storage-to-production systems, manage conveying requirements, provide installation and maintenance support and enable plant wide data collection and analysis capabilities.
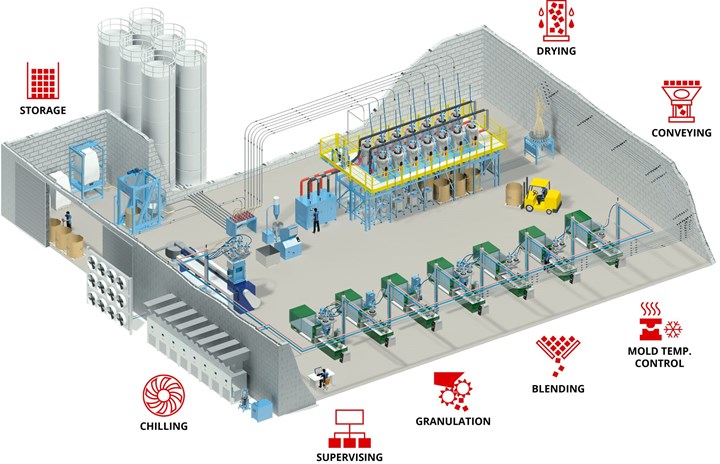
Processors are well served by picking an expert partner that can help assess all your current drying requirements within the context of your entire manufacturing environment.
Moretto can help with needs assessment and systems development regardless of the scale of the project and build a system that fits your business needs. For more information, please visit Moretto.com.