Real-Time Production Monitoring as Automation
As an injection molder, Windmill Plastics sought an economical production monitoring system that could help it keep tabs on its shop floor. It’s now selling the “very focused” digital supervisor it created, automating many formerly manual tasks.
While automation provides numerous benefits to the shop floor, there is at least one drawback that Frank Desrosiers picked up on quickly as his injection molding operation implemented more robotics. “We started to automate the facility here, and it’s great — you need less people on the floor — but at the same time: there’s less people on the floor,” Desrosiers says. “You have fewer eyes and ears on the production lines.”
Desrosiers is president of custom injection molder Windmill Plastics, Knowlton, Quebec, as well as its co-owner alongside his father and brother who bought the business in 2012. It was 2015 when Windmill began implementing more automation, working with Quebecois integrator CFM Robotics. Desrosiers says that as the company subtracted people it realized it would need to add some form of real-time monitoring for tasks like machine/process tracking quality issues, downtime reasons and cycle-time verification as it also sought to eliminate paperwork from the floor.
As CFM and Windmill collaborated, both companies perceived the market need for the production monitoring system Windmill envisioned. In 2016, the molder and the integrator formed a new business, dubbed Clariprod, to create such a technology. By 2018, Clariprod had a prototype and a third partner with more than two decades of database and software programming expertise after working with Windmill’s ERP provider, CDID, from Saint Georges, Quebec. That’s when CDID also became interested in investing and became the third leg of the ownership triumvirate.
By Molders for Molders
As Clariprod went to market, its primary sales pitch centered on the fact the design of its production monitoring system was intentional, informed by its own experience as an injection molder. “We operate a 24/7 molding factory for some of North America’s largest housewares companies,” Desrosiers says, “so we’ve got a good pulse on the specific needs for this type of solution — what features users would benefit from. That’s what I think makes it unique. We are the only solution in the market that was built by injection molders for injection molders.”
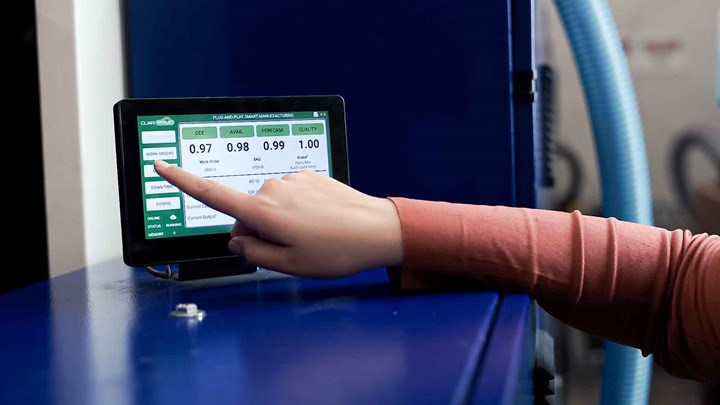
Clariprod’s controller promises fast installation at the press. Photo Credit: Clariprod
Before Windmill and its eventual partners decided to start Clariprod and while it still tested out already commercial production monitoring options, the company perceived some shortfalls with those systems that would inform its own design choices. Many of the products Windmill trialed sought to tie directly into the machines’ PLCs — a challenge when, like most molders, Windmill’s fleet is a smorgasbord of OEMs and vintages. “Like many molders, we’re not standardized,” Desrosiers says. “We have three different brands here that range over three decades.”
“We started to automate the facility here, and it’s great — you need less people on the floor — but at the same time: there’s less people on the floor,”
Some of the proposals Windmill received called for swapping out all the PLCs on its presses to achieve retroactive standardization or commonizing the disparate machines via multiple sensors or making costly changes to the company’s ERP system.
“We weren’t able to find that sweet spot of a solution that could stand alone, something that could and could give us all of the important production monitoring metrics at a cost that was really affordable,” Desrosiers says, “and also didn’t involve a ton of consultants on-site, standardizing PLCs or having people rework the data to standardize it across different presses.”
Windmill and its partners then sought to make what they couldn’t find in the form of Clariprod, getting to real-time overall equipment effectiveness operational efficiency (OEE) by connecting an electrical signal into the mold open/mold closed relay of a press with a dry contact. “That’s really the easiest way to do it,” Desrosiers says. “That allows us to stamp every single cycle down to the millisecond and keep a record of that.” Using that signal also enables the program to monitor when the press isn’t running via the signal’s absence.
Desrosiers says the simplicity of the system is exemplified in its installation, which entails connecting Clariprod’s controller to the machine via a ground wire and a wire into the mold open/close relay. It’s a process that from a hardware perspective takes roughly 20 minutes, according to Desrosiers. The controller features a 7-inch touchscreen with a microprocessor that acts as the communication portal to a cloud-based site created by Clariprod and hosted by Amazon Web Services, where the real-time OEE calculations are made.
The next step in installation involves configuration of what the system will track, report and alarm on, including reasons for downtime and reasons for rejects, among others, as well as the dashboard with the user reports, which include a suite of already developed analyses that can be segmented by numerous variables such as shift, machine, product or department and the chance to create new or customized versions. “It only takes half a day or a day to configure everything,” Desrosiers says. “Now, obviously, if you have 100 presses it can take a bit longer, but most of our customers are able to be up and running on the first day.”
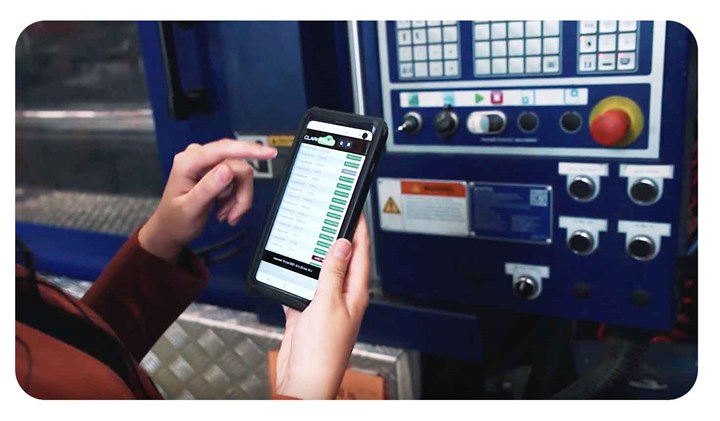
Clariprod’s status report can be viewed on any web-enabled device. Photo Credit: Clariprod
Seeking Visibility
Prior to joining Sapona Plastics, Asheboro, North Carolina, Rogon Walker spent more than 30 years in the medical molding industry, working with a variety of process and production monitoring systems. Now vice president of manufacturing at the custom molder, Walker sought a monitoring system for his plant that would track metrics like OEE, cycle time, scrap, OE, quality and performance. “I’ve been searching for many years to try to find a system that would work with what our needs were,” Walker says, “one where the people on the floor could immediately look at a dashboard on a big screen TV and see how they were performing.”
Walker’s search culminated in the evaluation of 10 different systems with three tested in-house, including a 30-day pilot trial of Clariprod. The fact that the makers of Clariprod are themselves injection molders came through when Sapona gave the system a dry run and ultimately acquired the technology. “I think the biggest attraction was the way it was formatted,” Walker says. “[Clariprod] knew exactly what you’re looking for; how they were able to attain the cycle time data and the interface made it very beneficial.”
Prior to installing Clariprod, Sapona already tracked many of the metrics gathered, analyzed and shared by the new monitoring system, but it didn’t do so in a real-time manner that was broadly displayed on the floor. The company would produce daily production reports covering efficiency, utilization and OEE, but creating them entailed a time-consuming process Desrosiers was familiar with at his molding operation.
At Windmill, the production manager would come in at 7 a.m. ahead of the start of the 8 a.m. shift and begin gathering data. “They would start gathering datasheets to try and make sense of them by 8 a.m., so we knew where we stood,” Desrosiers says. “Often times, depending on how it was going, we wouldn’t get the answer until midmorning.” Only when the data was tabulated, transferred into Excel and analyzed could Windmill make an assessment. “So we’d say, ‘O.K., we’re behind on these lines. Why? What’s happening exactly?’ That could take hours until you got there.”
Now Windmill and Sapona can immediately assess where they are. “OEE is the gold standard metric in manufacturing,” Desrosiers says. “The world’s best manufacturers are monitoring that in real time. There is a lot of value and savings to be had by quickly being able to identify when things are running well and when they’re not and being able to drill down. Is it a machine availability issue or are we running slow or are we making one bad part out of every five?”
Sapona’s chairman, Jack C. Lail, has long emphasized the importance of production data transparency, according to Walker. “Jack always said that if you track data and make it visible for the team and establish goals and objectives ,you’re going to improve that area,” Walker says. “If you make it visible — the goals for OEE, utilization, OE, uptime, as well as what’s down — your people will continue to improve them. For example, our analysis shows that we have improved machine utilization by more than 10% since implementing the system, simply by having teams more readily aware of which machines are down and when.”
“The world’s best manufacturers are monitoring (OEE) in real time.”
The alternative to such visibility, according to Desrosiers, is blindness. “If you don’t have that type of visibility, then you’re running blind,” Desrosiers says. Clariprod estimates that up to 80% of plants in the plastics industry in North America are largely ‘blind.’ “The reality for them is they’re compiling information, often still on paper, and then the day after having to sum it up and see what went right or what went wrong and why they’re behind in their production counts.”
Moving forward, Desrosiers says Clariprod is about to release a system that connects directly via cellular networks, eliminating the need for internet or Wi-Fi capabilities. The company is also currently in a beta-testing phase for a version of the monitoring technology that targets extrusion and, finally, on the hardware front, Clariprod is pursuing a wireless Bluetooth connection to the molding machine or molds versus hard wiring.
Desrosiers increasingly sees such production monitoring as automation, freeing workers from data gathering, entry and analysis, and helping address labor shortages. “Clariprod is like a very focused supervisor,” Desrosiers says. “So you’re replacing supervision and also a lot of data entry and capture. That’s a lot of labor that’s saved with these systems as well.”
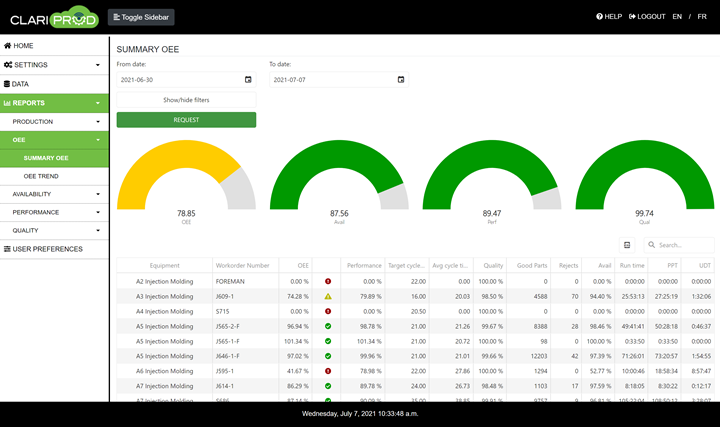
Clariprod provides real-time OEE reports for its users. Photo Credit: Clariprod
Related Content
Automation Evolution: From Robots to Work Cells, Solo Devices to Integrated Systems
Injection molding automation has progressed from devices to systems, from simplicity to more complex capabilities. The author traces this development through various levels of automation – all still available choices today – and analyzes the costs and capabilities for each level.
Read More50 Years...600 Issues...and Still Counting
Matt Naitove marks his first half-century in plastics reporting, with a few of his favorite headlines.
Read MoreFive Ways to Increase Productivity for Injection Molders
Faster setups, automation tools and proper training and support can go a long way.
Read MoreAutomation in Thermoforming on the Rise
Equipment suppliers’ latest innovations exemplify this trend driven by factors such as labor shortages, higher-speed thermoformers and tighter quality control.
Read MoreRead Next
Process Monitoring or Production Monitoring—Why Not Both?
Molders looking to both monitor an injection molding process effectively and manage production can definitely do both with tools available today, but the question is how best to tackle these twin challenges.
Read MoreHow Can Molders Achieve Effective Process Monitoring?
You have developed a proper process; now you need to monitor that process to ensure its stability through a run.
Read More