Engineering Resins Compounder Expands to Take on More Scrap
Polymer Resources responds to sustainability push by upgrading plant with grinding and shredding equipment to take on both postindustrial and postconsumer reclaim.
The entire supply chain for plastics is responding to market demands that promote sustainability and a circular economy. Some are responding quicker than others. Count Polymer Resources Ltd., a leading U.S. compounder of high-quality engineering resins with headquarters in Farmington, Connecticut, among the fast movers.
Last year, the compounder of engineering resins completed the expansion and enhancement of its compounding facility in Rochester, New York. The company has significantly upgraded an existing building on its campus to support a 40% increase in overall compounding capacity.
Polymer Resources, founded 50 years ago, serves customers in a wide range of markets, with a strong emphasis on electrical/electronics (it offers more than 70 UL grades).
Its specialty is electrical/electronic compounds which are used in buildings for wiring devices, circuit protection, cable ties, connectors/ terminal blocks and power equipment; in electronics for flashlights, residential and commercial controls, signaling protection and communication (such as automatic detectors and traffic cameras); and in lighting systems for controls and sensors, emergency lighting and exit signs.
The compounder also participates in a variety of other markets with injection molding, extrusion and blow molding grades for medical/health care, transportation, industrial, appliances, housewares, sporting goods, toys and more.
Its range of services extend beyond formulating compounds to include product design, tooling recommendations, troubleshooting and process development, agency approval support (both UL and CSA) and thermoset-to-thermoplastic conversion, which is a big issue for some electrical components.
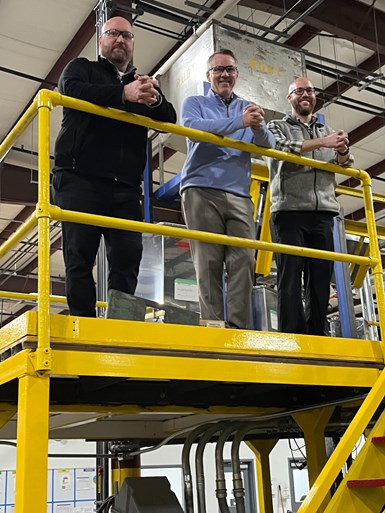
Polymer Resources recently expanded its operation in Rochester, N.Y., to handle more scrap. Pictured (left-right): Rob Currie, plant manager; Scott Anderson, president and COO; and Timothy Farrell, director of technology. Source: Plastics Technology
Some seven years ago, when Plastics Technology visited the Polymer Resources operation in Connecticut, President and COO Scott Anderson described the company as a “small big guy,” meaning that it provides the speed, flexibility and service that usually are the hallmarks of a small business, and combines that with the technical firepower of much larger firms.
Says Anderson, “Every product we make is for a specific customer. We don’t shoehorn customers into this grade or that grade. Our orders range from 250 lbs to a full truckload.”
The compounder has stocking programs for customers and will inventory compounds in either of its two production plants or at one of 10 distribution centers across the country. Polymer Resources has four-week lead times for custom-colored compounds, two weeks for black and gray, and offers an Express Service program that can provide turnarounds in as few as three days.
Upgrades in Rochester
The compounder’s two production plants, as Anderson puts it, “back up each other,” meaning there is built-in manufacturing redundancy that enables orders to be filled in either location. That said, each plant has its particular focus, with the Connecticut facility honing in on color formulations and Rochester riveted on sustainable, natural and black formulations.
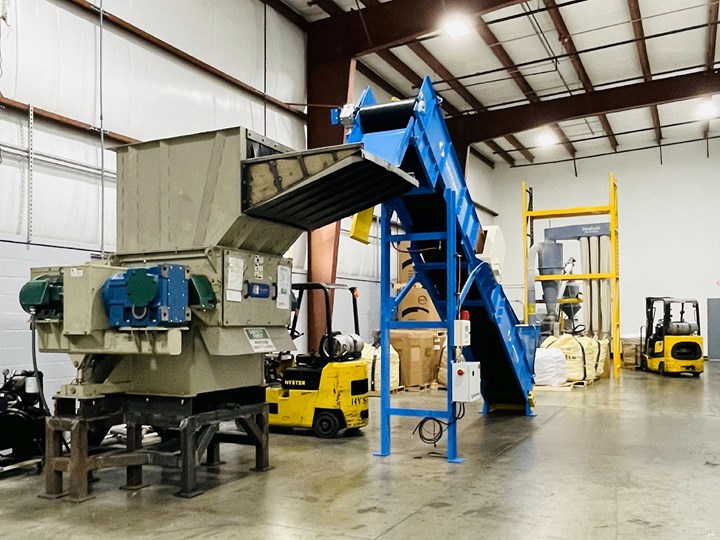
Grinding and shredding scrap is handled in a separate, sound-proofed 3,200 ft2 room. Source: Polymer Resources.
Two years ago, the new location for the plant in Rochester was mainly used for warehousing, while a separate site housed three compounding lines. Over the course of a year, under the direction of Rob Currie, plant manager in Rochester, the facility was upgraded for manufacturing, with a focus on ehhancing extrusion operations and handling scrap. As part of that process, it built out a separate, soundproofed, 3,250-square-foot room for grinding and shredding postindustrial and postconsumer waste for its sustainable resin grades. It also moved a twin-screw extruder from its Connecticut plant to New York. All told, the new equipment increased capacity by 40%..
The project expanded the footprint of the compounding facility from a total of 35,000 square feet, previously divided between two buildings, to 60,000 square feet in one building. This change offers far more space for compounding and grinding operations, storage, a laboratory and offices, and it improves process efficiency and streamlines workflow. The firm has the space in Rochester to add an additional twin-screw line and also owns property close to its existing location to enable future expansion to 100,000 square feet. Polymer Resources runs three shifts/5 days a week in Rochester and operates with 25 employees.
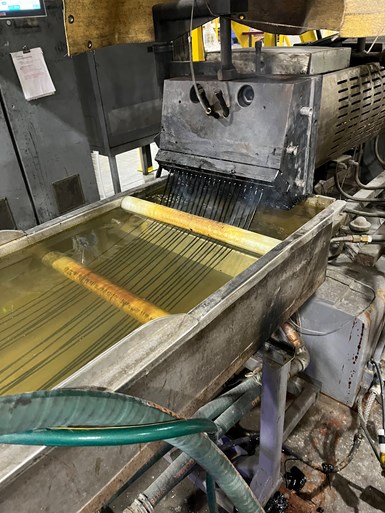
Polymer Resources added boosted production capacity in Rochester by 40% to handle reclaim. Source: Plastics Technology
Polymer Resources also designed the Rochester facility with employees in mind. It houses a powerful air filtration system, a dust collection system for the grinding operation and a modern break room. Greater space between machines also improves workers’ physical safety as they move around the production floor.
This is consistent with its move years back in Connecticut, when it installed an air-purification system on the production floor to capture dust.
“This is developing and formulating grades that come with specific specifications for demanding applications that must perform as well as their all-virgin counterparts.”
Material suppliers formulating with scrap feedstock have two critical challenges. Steady supply is one. Polymer Resources has long-term agreements in place with molding customers to take back their scrap — off-spec parts, purging, runners and the like. The company works with its customers to help them in establishing best practices on segregating scrap for ultimate delivery to Rochester.
And it is working with undisclosed brand owners to reclaim postconsumer scrap. When Plastics Technology toured the Rochester plant, it was packed with rows of post-consumer parts made of PPO that previously had been discarded.
A second critical challenge for material suppliers formulating with scrap, whether postindustrial or postconsumer, is performance. “For years we’ve produced utility grades of material containing PIR or PCR to help our customers drive costs down,” Anderson says. “But this isn’t that. This is developing and formulating grades that come with specific specifications for demanding applications that must perform as well as their all-virgin counterparts. These materials are made-to-order for specific customers and to meet rigorous specification requirements.”
As Polymer Resources’ Director of Technology Timothy Farrell explains, to assure quality and consistency, the company inspects and tests all recycled content according to the ISO 9001-2015 standard for quality management. “Understanding the properties of the recycled content is critical to success,” Farrell notes. Scrap material is moved from the shredding and granulated room in gaylords. A three-ribbon blender then mixes this scrap with virgin resin and various additives and reinforcements, as needed. The mixture is then conveyed to the extruders.
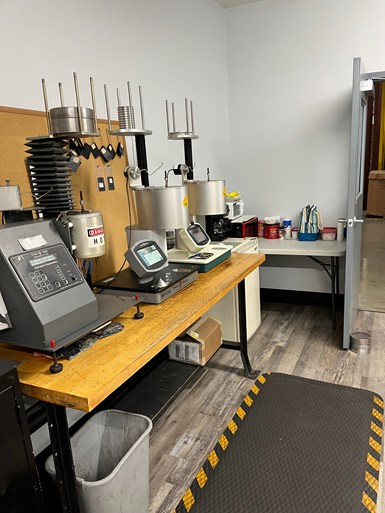
Polymer Resources has the full gamut of instruments at its lab in Rochester to inspect and test recycled materials to the ISO 9001-2015 standard for quality measurement. Source: Plastics Technology
Polymer Resources initiated its sustainable materials portfolio with the development of four general-purpose grades, each containing a minimum of 50% recycled content. The four commercially available products consist of a low-flow PC (PC-GP1S), a medium-flow PC (PC-GP2S), a high-flow PC (PC-GP3S) and a PC/ABS blend (PC/ABS-GP1S). All are opaque and available in natural, black or custom colors.
Next on Polymer Resources’ agenda is UL94 V0 listing for flame-retardant grades of PC and PPO-modified polyphenylene ether (PPX) that will enhance the sustainable material portfolio. These grades will also contain at least 50% recycled content. Target applications include electrical/electronic components, industrial parts and consumer products.
“The expansion of our Rochester facility is strategic to the robust growth of our compounding capabilities and the expansion of our sustainability initiatives, both of which are increasingly important to customers,” Anderson says. “In addition to continuing to address customer requirements for scalable, reliable resin supply, short lead times and exceptional quality, the updated facility will help us advance sustainability through plastic waste collection and recycling. We are committed to helping our customers reach their production and sustainability goals, as well as meeting our own sustainability goals, and this new facility positions us to achieve those objectives.”
Related Content
A Recycling Plant, Renewed
Reinvention is essential at Capital Polymers, a toll recycler that has completely transformed its operation in a short period of time.
Read MoreScaling Up Sustainable Solutions for Fiber Reinforced Composite Materials
Oak Ridge National Laboratory's Sustainable Manufacturing Technologies Group helps industrial partners tackle the sustainability challenges presented by fiber-reinforced composite materials.
Read MoreProcessing Megatrends Drive New Product Developments at NPE2024
It’s all about sustainability and the circular economy, and it will be on display in Orlando across all the major processes. But there will be plenty to see in automation, AI and machine learning as well.
Read MoreAdvanced Recycling: Beyond Pyrolysis
Consumer-product brand owners increasingly see advanced chemical recycling as a necessary complement to mechanical recycling if they are to meet ambitious goals for a circular economy in the next decade. Dozens of technology providers are developing new technologies to overcome the limitations of existing pyrolysis methods and to commercialize various alternative approaches to chemical recycling of plastics.
Read MoreRead Next
Processor Turns to AI to Help Keep Machines Humming
At captive processor McConkey, a new generation of artificial intelligence models, highlighted by ChatGPT, is helping it wade through the shortage of skilled labor and keep its production lines churning out good parts.
Read MoreTroubleshooting Screw and Barrel Wear in Extrusion
Extruder screws and barrels will wear over time. If you are seeing a reduction in specific rate and higher discharge temperatures, wear is the likely culprit.
Read MoreUnderstanding Melting in Single-Screw Extruders
You can better visualize the melting process by “flipping” the observation point so that the barrel appears to be turning clockwise around a stationary screw.
Read More