Daimler, OMIC Evaluate Wire-Fed DED for Moldmaking
3D printing a core and cavity on machine from Gefertec, followed by machining, allowed for a complete mold tool to be produced in three days.
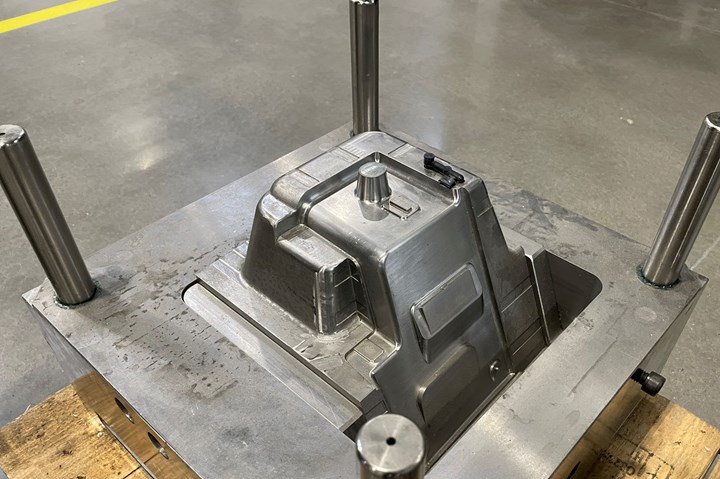
Using a wire-fed DED process, this injection mold for a truck component was produced in 3 days versus the several weeks of lead time more typical for a mold such as this.
Does directed energy deposition (DED) offer a way to fast-track large injection mold tooling?
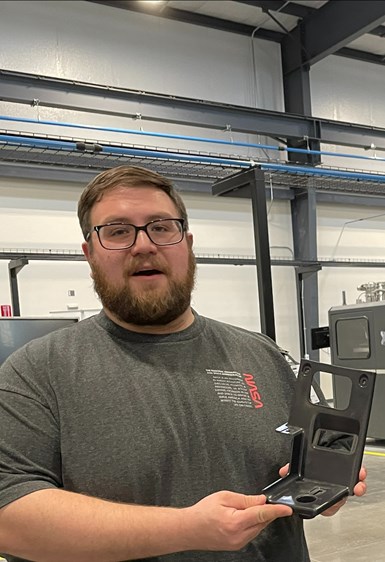
Josh Koch of OMIC was involved in the project, which demonstrates the potential responsiveness that might be possible in making mold tooling. “You just need to have wire on hand,” he says.
The Oregon Manufacturing Innovation Center (OMIC) recently worked with truck manufacturer Daimler to validate that it does. A complete core and cavity set for a large mold (pictured), including internal conformal cooling channels, was 3D printed through wire arc additive manufacturing (WAAM), or wire-fed DED, on a machine from Gefertec in OMIC’s facility in Scappoose, Oregon. Dr. Mostafa Saber of Oregon State University aided in this work.
Additive manufacturing for injection mold tooling often takes the form of a process such as laser powder bed fusion making a much smaller tool, typically mold inserts providing conformal cooling for only those areas of the mold featuring cooling challenges. Engineers at Daimler, which manufactures trucks at a nearby plant in Portland, were interested in the potential of AM for the entire mold for the sake of lead time savings in larger mold tooling. However, the DED process also offered a practical way to include cooling channels that are not straight drilled holes, but instead are 3D printed to conform to the surface of the mold.
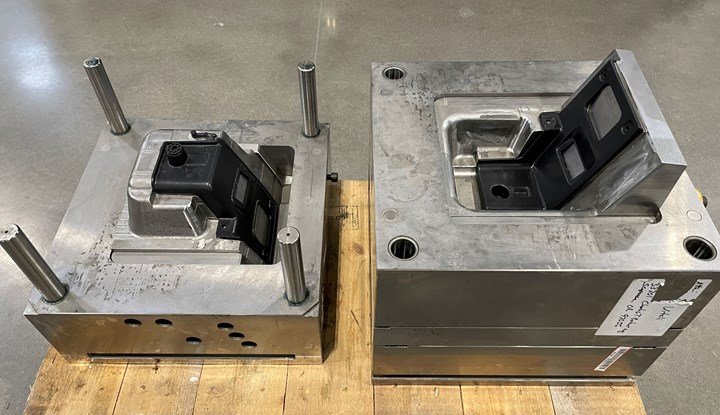
Here is the core and cavity, both 3D printed (then machined), along with the plastic part this tool set is used to produce.
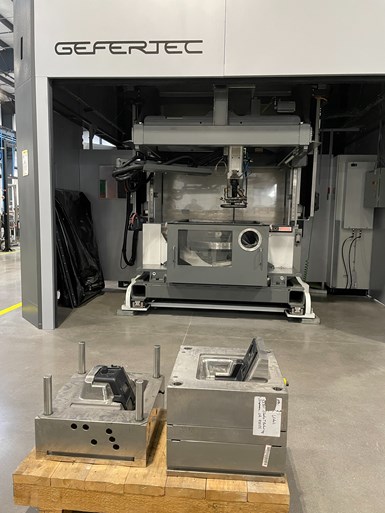
The Gefertec WAAM machine at OMIC made the mold tooling. OMIC offers a way for manufacturers to use and evaluate additive technology prior to investing in it themselves.
The demonstrated lead time savings were considerable, say OMIC executive director Craig Campbell and business development manager Joshua Koch. Lead time of several weeks is commonplace for the truck maker’s mold tooling. By contrast, the AM core and cavity were 3D printed on the Gefertec machine in 2 days. The tooling made this way was close enough to its final shape that only finish machining was needed. The machining work to complete the mold set took an additional day.
The result is potentially a much more responsive way for Daimler to obtain the tooling for new and emergent injection molding needs, Koch says. He adds, “To make a new tool, you just need to have the wire on hand.”
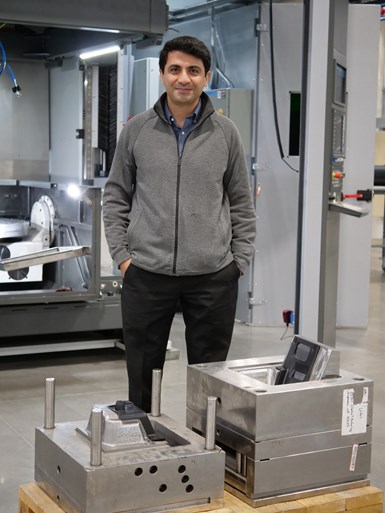
Dr. Mostafa Saber of Oregon State University also worked with OMIC on the DED mold project.
OMIC is an organization funded in large part by the state of Oregon to provide a vehicle for public-private R&D and process development partnerships with manufacturers. Machining and additive manufacturing are its focus areas. Member organizations (currently 38 companies and three universities) work with OMIC on its machines at its facilities to evaluate new manufacturing equipment or technologies. (Non-members work with the organization, too, just at a higher price.) The Additive Innovation Center at OMIC opened in 2023, and currently features machines for binder jetting (ExOne, now Desktop Metal), DED (Gefertec) and laser powder bed fusion (Renishaw), as well as hot isostatic pressing (Quintus). A process soon to be added is composite-based additive manufacturing via a system from Impossible Objects.
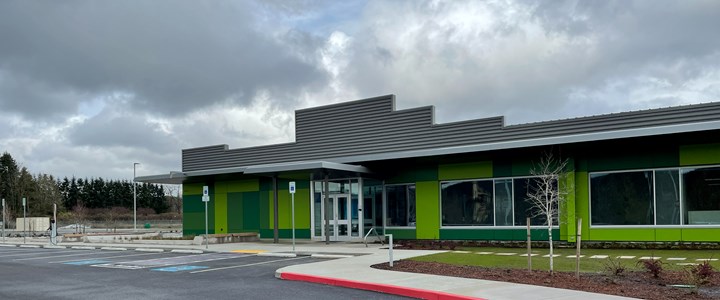
OMIC’s Additive Innovation Center opened in 2023, offering manufacturers in the region access to what is likely to be the broadest mix of additive manufacturing capabilities available in one facility in the Pacific Northwest.
This mix of capabilities all in one place likely exists nowhere else in the Pacific Northwest, OMIC says. The large Gefertec machine is one of few like it operating in the U.S. “We offer a way for manufacturers to use, evaluate and develop the application for additive manufacturing before adding the capability to their own facility,” Campbell says.
That was Daimler’s tactic with the 3D printed mold — an idea that can still be carried much further, Koch says. A likely next step is to evaluate the special freedom WAAM offers to print with multiple materials in the same build. A mold could be produced in which one metal was applied quickly and cheaply to give bulk to the tool, while another metal is applied only at the surface for the needed hardness and other properties.
This could also make possible a different idea in conformal cooling, he notes. Does the cooling of the mold have to involve water flowing through the tool? One hazard is mildew in the channels, he says. An alternative could be the use of a thermally conductive metal. A future version of the mold seen here might involve no channels for cooling, but instead might be made of copper inside the bulk of the tool to ensure fast transfer of heat. The tool would still be tool steel, but only at the surface where the mold is compressed together, contacts the part and actually does the physical work of molding.
Related Content
Production Tool, Prototype Time
Mantle's metal 3D printing technology targeted toolmaking and injection molders and moldmakers are taking notice.
Read MoreCustom Molder Manages Growth on Several Fronts
Adding people, plants and machines, expanding capabilities in LSR, high-tonnage presses, automation and 3D printing—EVCO Plastics maintains momentum through challenging times.
Read MoreMake Every Shot Count: Mold Simulation Maximizes Functional Parts From Printed Tooling
If a printed tool only has a finite number of shots in it, why waste any of them on process development?
Read More420 Stainless Steel Now Qualified With TrueShape 3D Printing Technology
NPE2024: Mantle's Additive Manufacturing Technology is Designed for Precision Tooling
Read MoreRead Next
Mantle: 3D Printed Molds Address Plastics Industry Lead Time and Skills Shortage
Company now shipping production systems. Steel mold tooling from its TrueShape process can be printed, shaped and sintered in days, and with fewer steps, compared to weeks of lead time for molds made conventionally.
Read MoreWire Arc Additive Manufacturing Delivers Low Buy-To-Fly Ratios
Manufacturers in the aerospace industry buy expensive raw material with one common goal: to make it fly. To reduce its buy-to-fly ratio (the ratio of material inputs to final part output), this company turned to wire arc additive manufacturing to create near-net shape parts.
Read MoreConformally Cooled Injection Mold Reduces Cooling Time by 55 Percent
With Renishaw’s help, Kärcher ended its production bottleneck using 3D-printed molds with conformal cooling channels.
Read More