Five Strategies for Cutting Reshoring/ Nearshoring Costs via Data Automation
Leveraging real-time data via tools like ERP and MES is one form of automation plastics processors can apply to capitalize on reshoring and nearshoring trends.
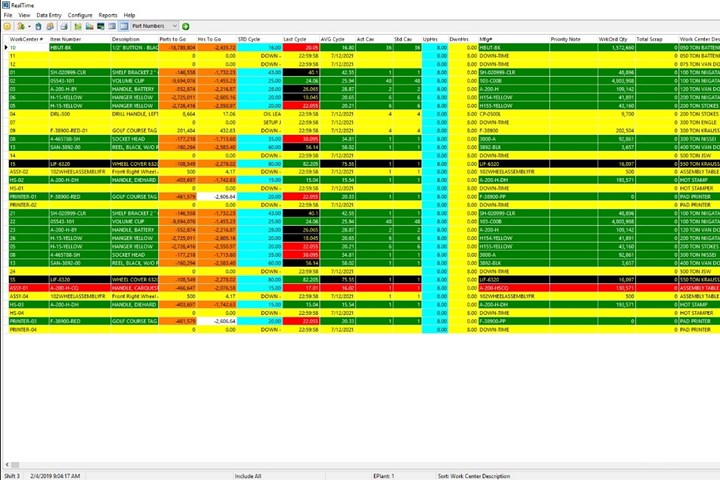
Real-time updates and a 360° view of all scheduled jobs across all shop floors can help plastics processors gain greater visibility and control over operations.
Photo Credit: DELMIAWorks
For decades, many manufacturers relied on plastics processing operations in Asia, most notably China, to take advantage of low wages and cheap real estate. However, supply chain uncertainty, long lead times, tariffs and rising costs have eroded the advantages of offshoring in the region. As a result, the plastics industry has seen a strong move toward reshoring and nearshoring in North America, Latin America and the Caribbean. In fact, the Manufacturers Association for Plastics Processors (MAPP) noted in its “State of the Plastics Industry Report 2023” that 54% of plastics processors see their customers reshoring — the highest percentage in 18 years.
The move toward reshoring and nearshoring presents plastics manufacturers with the opportunity to compete on the basis of high quality, easier collaboration, and faster delivery, among other benefits. Moreover, automation of data collection and interpretation now makes it possible to offset the costs associated with higher local wages. Let’s look at the main drivers that are leading to reshoring and nearshoring in the plastics industry, along with five ways that plastics processors can employ automation to compete effectively while maintaining margins.
Plastics Industry Reshoring and Nearshoring Drivers
According to the MAPP “State of the Plastics Industry Report 2023,” more than one-third of plastics processors surveyed reported that they gained business from foreign competition. This indicator of a continued move toward reshoring aligns with findings by the “Reshoring Initiative 2022 Data Report” that more than 364,000 manufacturing jobs were announced in the United States last year. A 53% increase over 2021, these gains were due to reshoring and foreign direct investment.
Both reshoring and nearshoring can provide several strategic benefits, including the ability to alleviate geopolitical risks and the high costs of tariffs; improve quality control; and gain greater agility to respond to changing customer and market demands. For many plastics processors, two factors serve as the primary motivators for reshoring and nearshoring: proximity to customers and the advantage of a regional resin supply.
Proximity to Customers
Among U.S. manufacturers, 62% have begun shifting from suppliers in Asia to suppliers based in closer-proximity markets to reduce transportation costs and improve time-to-market, according to Deloitte’s report, “The Future of Freight: Transforming the Movement of Goods.” For many plastics processors, the ability to relocate production closer to customers also makes it easier to communicate and collaborate with them and customize solutions to their needs, boosting customer satisfaction. Additionally, by having better visibility into customers’ future orders and their forecasts in real time, these manufacturers are able to build greater resilience into their supply chain.
Regional Resin Advantage
Within the plastics industry, a compelling factor in reshoring and nearshoring is the availability of resins according to Shale Crescent USA in its report, “Global Economic Factors Align Favoring U.S. Plastic Product Manufacturing Over China-Based Operations.” The report observes that Ohio, West Virginia and Pennsylvania combined produce one-and-a-half times more natural gas than China — a huge advantages in a key plastics feedstock. By contrast, China either imports plastic resin or produces resin from more expensive Naphtha based on crude oil. Additionally, the report notes that the distance between U.S. resin providers and North American processors is often less 2000 miles. By comparison, the roundtrip to get resin or feedstock to China and then receive finished products in return is roughly 25,000 miles. That translates into a potential 30-day supply chain process for North American plastics processors.
Collectively the benefits of a regional resin supply include the ability to lower prices, reduce delivery times, decrease the working capital required, and enable greater feedstock flexibility. At the same time, the elimination of transcontinental supply chains enables plastics processors in North America to significantly cut their carbon footprint and support the sustainability initiatives of their organizations, customers and supply partners.
Five Ways to Reduce Costs Using Data Automation
Even as plastics manufacturers find ways to cut the costs of nearshoring and reshoring through regional resin supplies and lower transportation costs, they continue to face higher wages, particularly for skilled workers. Among plastics processors surveyed for the MAPP “State of the Plastics Industry Report 2023,” 55% stated that operator wages increased in Q4 2022, and for 3% of respondents, those increases were significant. Increasingly, these manufacturers are automating processes to reduce labor costs while increasing shop floor productivity and providing greater visibility and control across their shop floors.
There are five areas in particular where manufacturers can maximize the benefits of reshoring and nearshoring by using enterprise resource planning (ERP), manufacturing execution system (MES) and other solutions to leverage real-time data and drive automation.
1. Optimize Inventory Management
Local and regional facilities typically rely on trucking and rail transportation, making it cost effective to handle smaller shipments, reduce on-hand inventory and support just-in-time (JIT) manufacturing. Plastics processors can gain accurate, up-to-date insights into inventory by capturing real-time data from the shop floor in MES software and automatically updating the ERP system’s inventory management. By understanding, for example, the rate of production, quantity of material being used in production, and the amount of scrap available for reuse, manufacturers can maintain the right level of inventory to support customers while minimizing overhead.
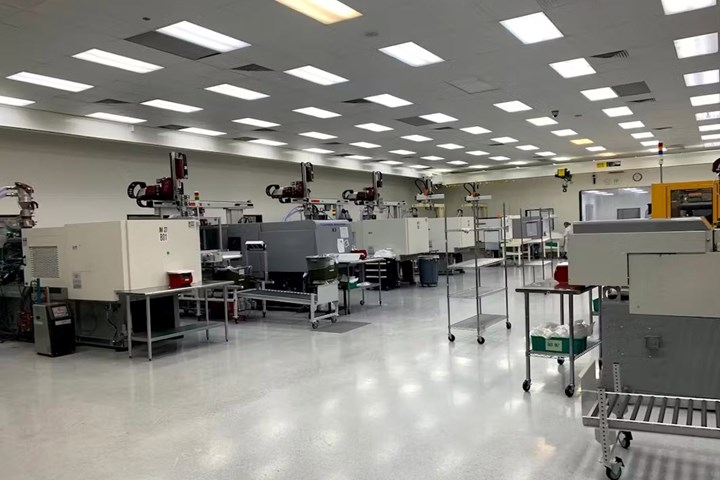
Trademark Plastics offers custom plastic injection molding services, producing more than 300 different plastic medical components.
Photo Credit: Trademark Plastics
For example, one plastics processor uses Internet of Things (IoT) sensors and devices to track production and material usage in real time. This data is fed into the manufacturer’s inventory management system to maintain the right inventory level to support customers while minimizing overhead. The data collected in the inventory management system also allows the plastics processor to track finished goods and provide customers with more accurate delivery estimates.
2. Run Lights-Out or Near-Lights-Out Operations
The integration of a programmable logic controller (PLC), which measures and controls manufacturing operations, with sensors, smart devices, and machine-learning algorithms can help plastics processors collect real-time data without human intervention, reducing errors and inconsistencies. Then data and insights from these technologies are fed into the MES software, enabling manufacturers to identify production bottlenecks across production operations and quickly make informed decisions that will increase production efficiency and cost savings.
The same functionality also provides the foundation for running lights-out or near-lights-out operations at local and remote facilities with minimal staff while maintaining high productivity. A case in point is plastics manufacturer Medical Components of America. Many of the 540 million components it has molded over the last five years were produced in a fully lights-out facility that runs 80 to 100 hours each week without human intervention. The company has gone five years without shipping a bad part or missing a delivery.
3. Increase Productivity and Consistency
At today’s plastics processing plants, work center dashboards provide operators with the data and tools to start production runs quickly and maintain quality. These touchscreen interfaces tie back to the ERP, while MES software presents operators only with the information needed to do their exact jobs, including provide real-time machine readiness, raw material availability and process parameters, so they can start production runs quickly.
Work center dashboards also provide the data and insights production teams need to keep orders on schedule while also monitoring the current state of every machine and process on the shop floor. Operators can control machinery and process parameters with these dashboards. Meanwhile, real-time data on cycle time, temperature, pressure and other critical process metrics delivered via the dashboards allow operators to spot deviations early and take corrective action, helping to improve production quality and consistency.
For example, Comar a provider of primary plastics packaging and dispensing products for the healthcare industry, uses its ERP and MES software for real-time process and product monitoring, quality management and production. Data is consolidated in the ERP system, which refreshes the dashboards used by production managers to provide them up-to-the-moment insights into production efficiency and quality.
4. Automatically Adjust Pricing to Costs
At least 90% of processors surveyed for the MAPP “State of the Plastics Industry Report 2023” passed on resin price increases to customers, but more than a third of those who saw price decreases didn’t pass on those savings. Keeping prices higher can increase margins, but it can also hinder a plastics manufacturer’s ability to compete, particularly in cost-sensitive markets. This dilemma points to the need for automatically adjusting product pricing to raw material costs to preserve both margins and customer loyalty.
By integrating real-time raw material cost data with the inventory management and customer information in their ERP system, manufacturers can automatically and dynamically modify pricing to keep pace with fluctuating costs and protect margins, while also aligning with any contractual agreements or discount rates in place with customers. Not only does this foster stronger relationships with customers; it can also cut demands on employees’ time. In fact, through automatic adjustments, one manufacturer was able to reduce the time to update individualized customer pricing from 40 hours over two weeks to just two hours.
5. Strengthen Supply Chain Collaboration
Plastics processors can improve their overall business performance and cut unnecessary costs by implementing supply chain integration across platforms and applications. Doing so provides continual updates on product quality at the network, supplier, and contract manufacturer level to facilitate operational efficiency and greater knowledge sharing.
Supply integration is achieved by combining real-time data with technologies such as ERP, supply chain management (SCM), customer relationship management (CRM) and analytics. Together, these capabilities automatically deliver insights needed to identify trends, bottlenecks and opportunities. Using these insights, that help plastics manufacturers and their partners have the power to improve their decision making, communication and collaboration — and ultimately orchestrate efforts to adapt to changes in demand in real time without impacting quality.
Seize Reshoring Opportunity
A confluence of factors is helping to accelerate reshoring and nearshoring in the plastics industry. Chief among these are the need to address supply chain delays and uncertainty; opportunities to deliver goods more cost-effectively; and the time-to-market advantages provided when plastics processors are located near both their resin supplies and customers. However, the continued rise of local wages, especially for skilled workers, can present a stumbling block to profitably maintaining local or regional operations.
To address the challenge, plastics processors increasingly rely on automation as a proven strategy for reducing labor costs and increasing shop floor productivity, making nearshoring and reshoring a profitable alternative to offshoring. By relying on real-time data to automate their business in the five areas outlined here, plastics processors can create more resilient, cost-effective and customer-focused onshore or nearshore operations to increase their competitiveness and thrive in a rapidly changing global economy.
About the Author
Louis Columbus, Senior Industry Marketing Manager, DELMIAWorks. Previous positions include product management at Ingram Cloud; product marketing at iBASEt; Plex Systems; senior analyst at AMR Research (now Gartner); marketing and business development at Cincom Systems; and Ingram Micro, a SaaS start-up. Louis has an MBA from Pepperdine University and completed the Strategic Marketing Management and Digital Marketing Programs at the Stanford University Graduate School of Business. He teaches MBA courses in international business, global competitive strategies, international market research and capstone courses in strategic planning and market research.
Related Content
Eigen Integrates Ampacet Color Monitoring into Machine Vision Solutions for Plastics
Injection molders, blow molders and extruders looking to avoid downtime and reduce scrap related to defect detection and color monitoring get a single solution for inline quality monitoring and management.
Read MoreSoftware Tracks Energy Waste in Real Time
Affordable add-on to production monitoring software alerts uses when energy is being wasted.
Read MoreNot Thrilled by All the ‘4.0’ Talk?
Are you (perhaps secretly) put off by expressions like Industry 4.0, Internet of Things, Big Data, Smart Factories, Digitalization and so forth? If so, you’re not alone. You might be friendlier to terms like operational Transparency and Visibility.
Read MoreIndustry 4.0 Without Fear: Modular MES Software Lets You ‘Start Simple’ and Add on Later
‘Don’t be afraid of MES.’ App-based platform can start with monitoring just downtime and cycle time on a few machines and add machines and functionality later.
Read MoreRead Next
Eight Ways Manufacturers Can Attract & Retain Customers–Part 1
The time and effort invested in cultivating customer relationships and creating new ones deliver the most value.
Read MoreERP Platform Keeps Molders Connected in the Pandemic
Enterprise resource planning (ERP) software offers its users many tools and modules with manufacturing and plastics specific platforms like DELMIAworks touching everything from inventory and quality to bookkeeping and process and machine monitoring.
Read More