iMFLUX Leverages Its Resources to Fight Coronavirus
P&G’s subsidiary pressed its design and moldmaking expertise into service to make face shields and nasal test swabs for the COVID-19 pandemic.
Procter & Gamble’s seven-year-old subsidiary, iMFLUX, has devoted some of its large captive moldmaking and design capability, and in-house injection molding capacity, to developing and producing both personal protective equipment (PPE) and diagnostic devices to combat the COVID-19 pandemic. iMFLUX, which is known for its novel low-pressure injection molding technology (see August feature), initially pursued these projects on a pro bono basis, as part of P&G’s “Force for Good” response to the global outbreak.
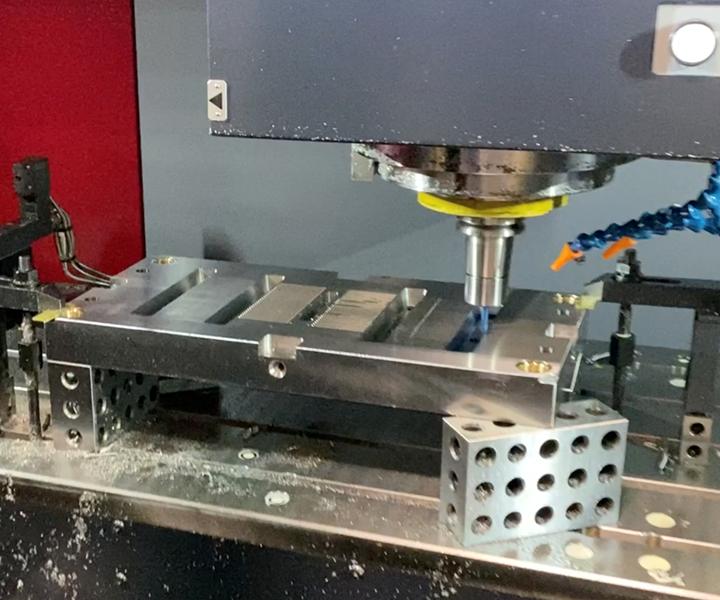
Working nights and weekends, iMFLUX built molds in nine to11 days for face-shield head bands and COVID-19 nasal test swabs.
In an interview, Mary Wagner, iMFLUX CEO, described these projects, and the collateral benefits that arose from them. The first project, which started in mid-March, is producing PP headbands for face shields. The face shield was designed by P&G Engineering resources in collaboration with the Cleveland Clinic, and the first production was donated to that clinic and to Children’s Hospital 14 days after starting the work. iMFLUX provided the ability to scale up production and aims to produce more than 12 million headbands by the end of July, initially for donation to the Cleveland Clinic and Cincinnati Children’s Hospital Medical Center, and more broadly for the Federal Emergency Management Agency (FEMA), which is buying them at cost.

“We scaled the headband design and built a four-cavity mold in 11 days from CAD drawing to delivery,” Wagner told Plastics Technology. To expedite the build, a mold base was repurposed from another application. Wagner added, “We dedicated one of the 12 presses in iMFLUX’s Innovation & Education Center to molding headbands 24/7.”

iMFLUX built this 50-cavity mold for nasal test swabs in just nine days for a customer to produce up to 2 million PP swabs a week.
Test Swabs in 50 Cavities
A second project was utilizing iMFLUX’s mold-building and design experience to produce a 50-cavity tool for COVID-19 nasopharangeal test swabs. “The mold was built in nine days and is an example of how we leveraged our ‘plastics ecosystem’ to meet a need,” said Wagner. “In this case, Milacron, with whom we have a strong relationship, used its DME tooling arm to expedite delivery of a mold base to us overnight. The first mold, capable of producing millions of PP swabs a week, is in operation at Young Innovations, which produces flocked swabs and markets them under the Microbrush brand. Additional molds and capacity are ramping up quickly to support this partnership.
iMFLUX has also partnered with a small group of experienced personnel that oversee P&G’s highly regulated businesses to design and clinically test a fully injection molded test swab that does not require any secondary steps such as flocking. P&G’s packaging suppliers have stepped up to support packaging and sterilization of finished swabs, which will be sold to FEMA and through healthcare distribution channels. Noted Wagner, “These prototypes offer new benefits, as they are less invasive, simple to administer, and the supply chain can be scaled up quickly to meet increased demand for at-home testing and a wide range of virus surveillance monitoring programs.” Once a preferred design is approved, iMFLUX will make it publicly available. “We’ll ‘open source’ it,” said Wagner.
“The new prototype swabs would be a perfect application for iMFLUX low-pressure molding technology.”
Looking back, Wagner noted, “These projects were managed nights and weekends while we continued to run our core business. Although this effort was not made for financial benefit, there have been positive results for iMFLUX. “We formed new relationships and elevated existing relationships with suppliers and customers. We also discovered things about how we run and things we could do differently.”
One thing apparent from this experience, says Wagner: “The new prototype swabs would be a perfect application for iMFLUX low-pressure molding technology.”
For more on what plastics processors and suppliers are doing to combat the pandemic, visit PTonline.com and search for “COVID-19” stories.
Related Content
Are Your Sprue or Parts Sticking? Here Are Some Solutions
When a sprue or part sticks, the result of trying to unstick it is often more scratches or undercuts, making the problem worse and the fix more costly. Here’s how to set up a proper procedure for this sticky wicket.
Read MoreWhat to Do About Weak Weld Lines
Weld or knit lines are perhaps the most common and difficult injection molding defect to eliminate.
Read MoreHow to Set Barrel Zone Temps in Injection Molding
Start by picking a target melt temperature, and double-check data sheets for the resin supplier’s recommendations. Now for the rest...
Read MoreRead Next
Low-Pressure Injection Process Facilitates ‘Green Molding’
Besides speed and quality advantages, the low-pressure iMFLUX process is said to enhance sustainability—easing use of recycled and biobased materials, saving energy, reducing scrap, and adding lightweighting potential. See what molders say about these “green” benefits.
Read MoreMoving Toward ‘Autonomous Molding’ with a Uniform-Low-Pressure Process
A new low-pressure injection molding process has aroused interest among molders and machine suppliers. In his second article on iMFLUX, the inventor of the process explains how it is evolving to support the overall industry goal of self-correcting molding processes that can compensate for common causes of variation to maintain consistent part quality.
Read MoreA New Way to Mold Better Parts Faster and Easier
A new injection molding process ‘breaks all the rules’ by using low, constant pressure to achieve faster cycles and better-quality parts.
Read More