3D Printing Providing Opportunities During COVID-19
A look at two companies working on 3D-printed PPE equipment.
There’s been plenty of movement in the 3D printing space to answer the call to help combat COVID-19 through the use of PPE equipment. Here’s a look at two companies working in this area; one is a tech business that expanded its 3D printing offerings and the other is an early stage start up.
Rajant Corp., a provider of private wireless networks, worked with applying the 3D printing knowledge it uses to create fixtures for its BreadCrumbs wireless network nodes, to construct protective face masks.
The two 3D printers Rajant had on-hand, before COVID-19, quickly doubled to four, and orders for raw materials were put into process. Materials came from from US-based filament producers Atomic Filament in Indiana and in FilaCube in Texas. Much of the detailed work is done not by machine but by human hands, the company says. Volunteers from Rajant’s extended family, like Laurie Barry and her 83-year-old father Gary, have carefully sanded and cleaned every single unit prior to boxing.
Alice DiSanto, AVP of marketing, said that the company has produced approximately 250 masks, about half small and half large in size.
“We based our design on the well-known, Montana mask design, which Rajant optimized for weight, flexibility, speed of printing, and comfort,” she said.
The company has since shifted from masks to the production of face shields. The face shield head band is an unmodified design from Thingiverse.
Early stage startup
Nishat Rustagi is the founder of Make, an early stage startup that is building a digital manufacturing workflow platform. Make has a network of industrial 3D printers that is spread across America, capable of handling production needs starting from prototyping one part to mass producing end use parts at any scale.
Rustagi says that while the software development industry has seen significant advancements in the tools to make software, the hardware/manufacturing industry - 12 times the size - still operates over legacy infrastructure.
“We want to change that by building digital tools for hardware developers. Our platform sits on top of a decentralized network of latest industrial 3D printers, CNC and injection molding machines,” he said. “Currently, we're helping developers save up to 90% in cost per part and up to 60% in lead time.”
Customer segments they’re targeting include consumer electronics, wearables, robotics, IoT products, medical devices, consumer goods and sporting goods.
Make is also involved with the COVID-19 Response Innovation Lab at Stanford, which is a new organization sponsored by the Stanford Biosecurity program in the School of Medicine. The lab is an incubator that provides pro bono services, financial assistance and general support to organizations working on projects that address everything from job searching to social isolation to health data detection.
Make is using its resources to print PPE face shields. Rustagi says that the company’s work is completely decentralized and distributed so they can print 25K+ shields per week and scale up to manufacturing millions using injection molding.
“We’re seeing more engagement from clients as they’re looking to move more toward digital tools instead of having to drive to their local machine shop, which is right now, not possible,” he said.
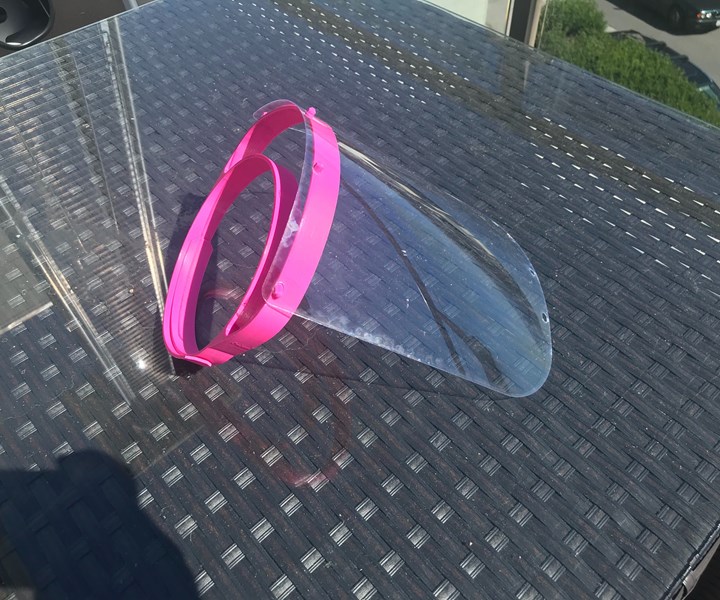
An example of a face shield printed through Make’s manufacturing network.

Related Content
How Additive Manufacturing Can Help, not Hinder, Injection Moldability of New Designs
Four cost drivers—design for moldability, mold-base size, internal componentry, polish/custom finishing—dictate the financial and processing success of a molded part design. Learn how 3D printing can assist this process, while also understanding its potential pitfalls.
Read MoreGetting into Plastics Additive Manufacturing? Avoid these Six Common Errors
There are a lot of 3D printing technologies out there, and it’s not uncommon for processors new to additive manufacturing to get tripped up. Here are some typical snafus, along with advice on how to avoid them before you start making parts.
Read MoreDaimler, OMIC Evaluate Wire-Fed DED for Moldmaking
3D printing a core and cavity on machine from Gefertec, followed by machining, allowed for a complete mold tool to be produced in three days.
Read MoreMedical Manufacturer Innovates with Additive Manufacturing and Extrusion Technology Hubs
Spectrum Plastics Group offers customers two technology hubs — one for extrusion, the other for additive manufacturing — to help bring ground-breaking products to market faster.
Read MoreRead Next
FDA Grants Formlabs Emergency Use Authorization for 3D-Printed Ventilator Component
Formlabs has the capacity to produce up to 3,000 3D printed adapters a day and is now shipping the adapters to hospitals for critically ill COVID-19 patients.
Read More3D Printing Helps Keep Production Going During the Coronavirus Crisis
Formlabs and Essentium both discuss how their companies are responding to the COVID-19 crisis and how 3D printing can help eliminate potential supply chain disruption.
Read MoreLead the Conversation, Change the Conversation
Coverage of single-use plastics can be both misleading and demoralizing. Here are 10 tips for changing the perception of the plastics industry at your company and in your community.
Read More