New Method Boosts Medical-Tubing Efficiency
At Plastec West, Novatec unveiled an ultrasonic centering gauge to all but eliminate concentricity issues while decreasing startup time and slashing material waste.
Novatec has devised a novel method aimed at improving the processing of precision medical tubing. At February’s Plastec West show in Anaheim, Calif., the Baltimore-based machine builder took the wraps off its Ultrasonic Centering Gauge, a system that reportedly will allow operators to very easily center the tube in the tank during startup, avoiding troublesome processing issues, decreasing setup time and wasted material.
The new Novatec Ultrasonic Centering Gauge ensures a microbore tube is quickly centered in the tank tooling before processing. According to Bob Bessemer, Novatec’s v.p. of extrusion technology, this is critical because it solves concentricity issues due to the tube rubbing against the entry tooling. He explains, “When processing microbore tubing, the crosshead die is typically in very close proximity to the water or vacuum-tank tooling, making it almost impossible to see whether the tube is centered in the tooling and not rubbing against it, which leads to hard-to-solve concentricity issues and product defects.”
When Novatec developed its MVT Vacuum Tank Series, it found the vacuum was so stable it could be used to control water drool at the entrance to the vacuum tank. “This allowed the tube to enter a wall of water, which greatly enhanced concentricity over older systems using an iris or precise water-level control to minimize water exiting the tank in an uncontrolled manner,” Bessemer explains.
With this in mind, Novatec created a water-level-controlled vacuum chamber in combination with an open-to-atmosphere pre-skinning chamber to house ultrasonic transducers located at the entrance to the water or vacuum tank. The ultra-precise vacuum and water-level control allow the transducers to be maintained underwater even while located only 1 to 2 in. from the die face.
At Plastec West, Novatec displayed this unit in combination with a Zumbach Electronics O.D., I.D., Wall System, showing wall thickness/concentricity and the position of the tube within the housing. Crosshairs similar to a gunsight visually display the tube-centering process to assist the operator in using the tank up/down and side-to-side adjustments to center the tube. Bessemer also notes, “Because the transducers are so close to the die, the die acts as support for the tube, and thus no rollers or guides are necessary, further simplifying the string-up process and eliminating the potential for the tube to touch and/or stick to any surfaces, making it a truly non-contact solution.”

Novatec’s Ultrasonic Centering Gauge features a real-time display to facilitate centering the medical tube in the tank’s tooling.
Another advantage of the Ultrasonic Centering Gauge is the distance to the ultrasonic transducers from the hot die, according to Bessemer. “With traditional laser-gauge/cold control, the laser gauge is the control point, as this is the final tube measurement of the O.D. The distance from the laser gauge to the hot face of the die is the distance the control waits before making a change to either the internal air unit, vacuum level, or puller speed to control the dimensions of the tube being processed. But, generally, due to control-loop delays, it is typical for this distance to be 10 to 15 times longer.”
As an example, if the distance on a high-speed flexible PVC line from the hot die to the puller is 50 ft, then the control loop is every 500 to 750 ft. This means that small diameter or wall-thickness variations will not be corrected within this distance, leading to diminished Cpk quality values and thus not being able to run on the thin side of wall tolerances, notes Bessemer.
“For the last five to 10 years, the ultrasonic units have been enhanced to not only measure the wall thickness but also the outside ‘hot’ diameter, as the distance can now be measured from the individual transducer face to the outside of the tube,” Bessemer explains. “The typical ultrasonic transducer holder is mounted 18 to 20 in. inside the cooling or vacuum tank, which can accommodate a control distance of approximately 24 in. Within the software of these units, the ‘hot/ultrasonic’ diameter is compared with the ‘laser-gauge/cold’ diameter reading and then used as a dynamic offset for control. As with the previous example, if we now use, say, 24 in. from the hot die face to the ultrasonic transducer, and apply a 10-15X factor, we end up with a control loop of 20-30 ft. Dramatic improvements have been seen with the ultrasonic control and the associated tube tolerances and Cpks. This has allowed typical tolerances of ±0.001-in. diameter control of tubing with 0.125-in. O.D. at line speeds of 800 to 1000 ft/min or more.”
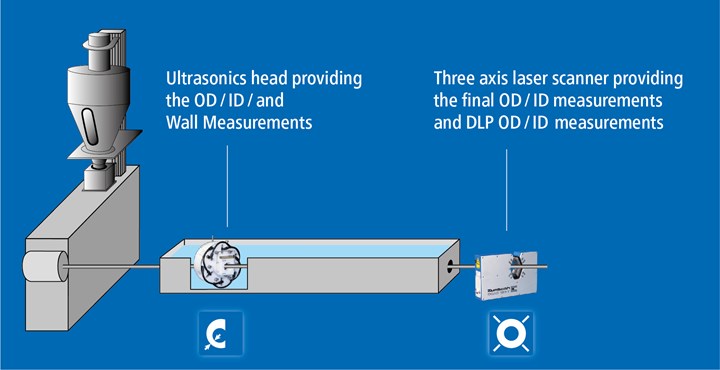
Novatec’s Ultrasonic Centering Gauge will also have the potential to take this “hot” control approach one step further, according to Bessemer. “With the holder mounted to the entrance of the water or vacuum tank, the transducers will be within 2 to 3 in. of the hot die face, which will further reduce the control point to 20-30 in. That will allow even further improvements in tube O.D. and wall-thickness tolerances and precision,” Bessemer explains.
Related Content
Plastic Compounding Market to Outpace Metal & Alloy Market Growth
Study shows the plastic compounding process is being used to boost electrical properties and UV resistance while custom compounding is increasingly being used to achieve high-performance in plastic-based goods.
Read MoreMedical Molder, Moldmaker Embraces Continuous Improvement
True to the adjective in its name, Dynamic Group has been characterized by constant change, activity and progress over its nearly five decades as a medical molder and moldmaker.
Read MoreNew Cap for Child-Resistant Pill Bottles Is Senior-Friendly & Saves Resin
Exclusive lightweight cap design can be removed simply pushing down on the center. No gripping or twisting needed.
Read MoreSeaway Plastics Acquired
Private equity firm ICG purchased the injection molder and its three facilities located in Florida and California.
Read MoreRead Next
New Downstream System For Inline Cutting, Curing of TPU Tubing
Novatec will debut an altogether new approach for processing tacky, hard-to-cut thermoplastic polyurethane tubes at next month’s Plastec West show.
Read MoreA Culture Built on Innovation in Medical Tubing Extrusion
Microspec was born out of innovation, and 28 years later continues to set the global standard in medical tubing by developing high-precision multi-lumen catheters—among other tubing products—by refusing to believe “it can’t be done.”
Read MoreDownstream System ‘Rewrites the Rules’ for Medical Tubing Extrusion
Extrusion downstream expert Bob Bessemer joins Novatec to enter medical tubing market with innovative line of tanks and puller/cutters.
Read More