Internal Gas Pressure Molding Offers Sustainability Benefits
Wittmann Battenfeld says its upgraded Airmould 4.0 technology, which features a more compact footprint, saves material and cycle time — thereby also cutting energy use.
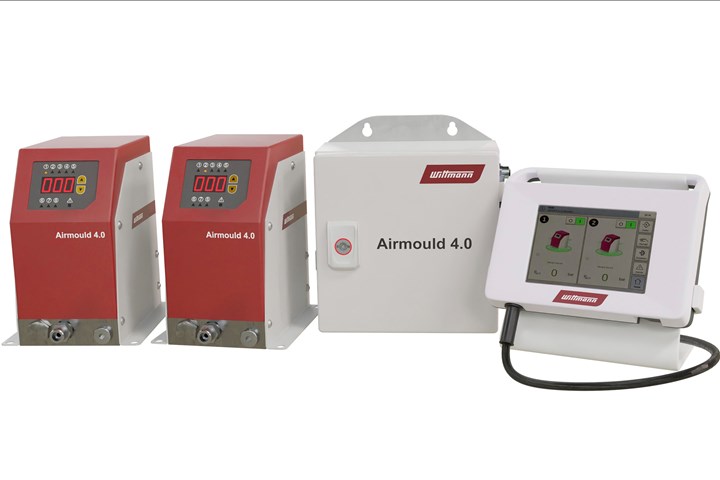
Wittmann’s Airmould 4.0 features a more compact design.
Photo Credit: Wittmann
Injecting nitrogen into a mold cavity that’s partly or completely filled with melt to form an internal void within the part, Airmould technology from Wittmann Battenfeld results in light-weight components made with shorter cycle times and featuring higher quality surfaces, while saving resources.
In 2022, the company rolled out Airmould 4.0 featuring an internal gas pressure system that eliminated the need for a large control cabinet, thus saving customers floor space. Furthermore, the necessary pressure control modules were also downsized. As a result, Wittmann says they can now be mounted and used flexibly on any injection molding machine. Airmould 4.0 can also be fully integrated in the Unilog B8 or B8X control system of Wittmann Battenfeld injection molding machines. If used on non-Wittmann presses, the company says user-friendly operation is possible via the Wittmann Group’s standardized manual control terminal.
At a time when CO2 footprint and conservation of resources are areas of focus, Wittmann say its Airmould technology has become more and more significant for users. This process saves plastic material, which in turn reduces part weight — an especially attractive prospect for the automotive and mobility sectors. Also, since gas assumes the function of the holding pressure and counteracts component shrinkage from the inside, Airmould can eliminate scrap parts resulting from sink marks and warpage.
Typical Airmould applications include bar-shaped parts like handles, levers, brackets and hangers. Some other common applications include media lines and tubes for the automotive sector and parts for the furniture industry, such as components for tables and chairs.
Apart from bar-shaped geometries, Airmould can also be used for flat parts with ribs, such as panels and covers, or beverage crates and tabletops. Here, the nitrogen is injected into the rib structures, in order to prevent sink marks on the surface of the opposite side. Moreover, this process is also suitable for flat parts with local bulges. Typical examples here are car outside mirrors, housings or reusable boxes.
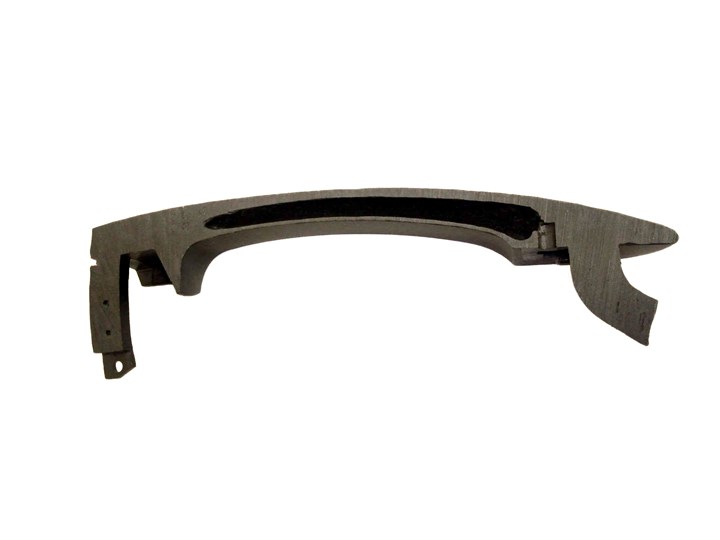
Airmould 4.0 displaces resin in the parts interior, cutting weight and resin usage, while also improving surface finish on the part’s exterior.
Photo Credit: Wittmann
Related Content
-
‘Monomaterial’ Trend in Packaging and Beyond Will Only Thrive
In terms of sustainability measures, monomaterial structures are already making good headway and will evolve even further.
-
Scaling Up Sustainable Solutions for Fiber Reinforced Composite Materials
Oak Ridge National Laboratory's Sustainable Manufacturing Technologies Group helps industrial partners tackle the sustainability challenges presented by fiber-reinforced composite materials.
-
Film Extrusion: Boost Mechanical Properties and Rate of Composting by Blending Amorphous PHA into PLA
A unique amorphous PHA has been shown to enhance the mechanical performance and accelerate the biodegradation of other compostable polymers PLA in blown film.