TCU with Common Control Offers Smaller Footprint, Ease of Operation
Units sized at 3 hp and under also require 15% less floor space than earlier designs.
The new Thermolator TW-T Series temperature-control unit (TCU) from Conair is quipped with the company’s common-control and 4.3-in. color touch-screen HMI package and also includes new features that reportedly make operation and maintenance much easier than previous TCUs.
TW-T Series units sized at 3 hp and under also require 15% less floor space than earlier designs. All sizes (from 0.75 to 10 hp) have an open-back cabinet that allows for beneficial air flow around pumps and other internal components and enables visual maintenance inspection without having to remove cabinet panels.
Other new features include:
Automatic phase detection: An alarm sounds if the TCU is powered up using incorrect wiring so it is no longer necessary to look at pump shafts to determine rotation.
Dynamic maximum setpoint: Cooling-water supply pressure determines the machine’s maximum setpoint (up to 250°F standard, 300°F optional), so processors can work around plumbing limitations. Low-pressure installations can now operate readily at lower temperatures, while higher water pressure provides access to full high-end range of setpoint temperatures.
Modulating cooling valve: Ensures consistent temperature control without valve changes or deadheading, even when in different mold applications or processes, or when the TCU is moved from one machine to another.
Industrial heater construction with leak-free heater gasket: This ensures for leak-free operation in high-pressure applications. No gasket maintenance or replacement required.
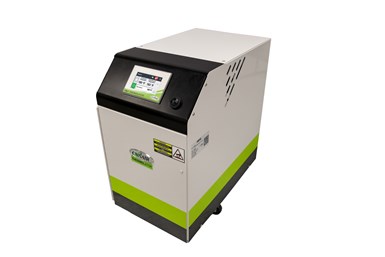
Photo: Conair
The new TW-T Thermolator units are among the most recent auxiliary equipment to be equipped with the exclusive Conair common control platform – a control (and associated touchscreen HMIs) that delivers the same look, feel and user experience regardless of equipment type. Common controls simplify and accelerate the training process since people trained on one machine and control can more easily and quickly translate that experience to operate other equipment that uses an essentially identical control.
The 4-in. touch-screen user interface gives operators access to top-shelf control functions like a customizable home screen that shows two Key Process Indicators (KPI). A five-step ramp/soak program protects the process from rapid changes in setpoint and possible thermal shock as the controller tries to force the process variable to follow. An alternate-set-point feature gives users the option to use an external input—a setting on the molding machine, for instance—for added control.
With the new TCU control, calculated flow rates, or current readings from an optional integrated flow meter are always available, while trend curves of historical readings can be used to help identify potential problems before they arise. These might include mold channels that need cleaning or set-up errors like incorrect hose connections or an unopened manifold valve. Trending is also available for temperatures.
The common control platform supports both OPC-UA (the leading Industry 4.0 communications protocol, supporting the Euromap 82.1 standard), legacy control protocols, like MODBUS, as well as SPI communications (RS-485). The new TW-T controllers are also SmartServices-ready. It is easy to connect the TCUs to Conair’s unique cloud-based platform, which allows processors to connect all of their plastics processing equipment (even older or non-Conair equipment) to a single, central web-based dashboard. From here, SmartServices is able to analyze temperature-control data (or data from any other equipment) and convert it into usable, actionable information for operators, maintenance technicians, plant managers, and even procurement specialists.
Related Content
Cooling Geometry and the Reynolds Calculation
The original Turbulent Flow Rate Calculator worked well with a round circuit diameter, such as a drilled passage, but not as well using hydraulic diameters. Here’s how the problem was fixed.
Read MoreTemperature Control: What You Need to Know to Comply With New Cooling-Fluid Regs
Beginning the first of this year, 12 states are following EPA bans on potentially damaging cooling fluids. Chiller suppliers have adjusted equipment designs to accommodate the new regulations. Here’s what all this means to processors.
Read MoreMachine-Side and Central Chiller Lines, Industry 4.0 Controls to Launch
Frigel will use K 2022 to showcase a number of developments in process cooling, including new and expanded lines of central and machine-side chillers, as well as advanced control platforms.
Read MoreIs Your Water System Setup Helping or Hurting Your Molding Plant Productivity?
The plant water system is a critical component of an injection molding facility. A poorly designed or maintained water-cooling system can have a serious impact on production efficiency and cause many maintenance issues. Here’s what you need to know — and ask — to prevent those problems.
Read MoreRead Next
Lead the Conversation, Change the Conversation
Coverage of single-use plastics can be both misleading and demoralizing. Here are 10 tips for changing the perception of the plastics industry at your company and in your community.
Read MoreBeyond Prototypes: 8 Ways the Plastics Industry Is Using 3D Printing
Plastics processors are finding applications for 3D printing around the plant and across the supply chain. Here are 8 examples to look for at NPE2024.
Read More