Temperature Control: What You Need to Know to Comply With New Cooling-Fluid Regs
Beginning the first of this year, 12 states are following EPA bans on potentially damaging cooling fluids. Chiller suppliers have adjusted equipment designs to accommodate the new regulations. Here’s what all this means to processors.
New state bans on industrial refrigerants that are potentially harmful to the environment went into effect Jan. 1 in 12 states. These mandates effectively prohibit plastics processors from purchasing new chillers that do not use refrigerants with low Global Warming Potential (GWP) — but current cooling equipment based on previously legal refrigerants can be used through the remainder of its life cycle.
Equipment manufacturers have found that newly required refrigerants provide comparable cooling capacity as those being banned. What’s more, processors should notice product improvements from their suppliers well beyond simply accommodating the new refrigerants, as the shift in coolant media triggered some to redesign their units.
So far, 12 states have enacted bans on refrigerants that the EPA’s Significant New Alternatives Policy (SNAP) program designates as having high GWP. These include the R-134a and R-410A refrigerants widely used in chillers and other temperature-control units. On the heels of federal legislation to regulate the production and use of hydrofluorocarbon refrigerant, these states have enacted their own legislation that aligns with — or includes even stricter regulation — than that set out in EPA SNAP Rules.
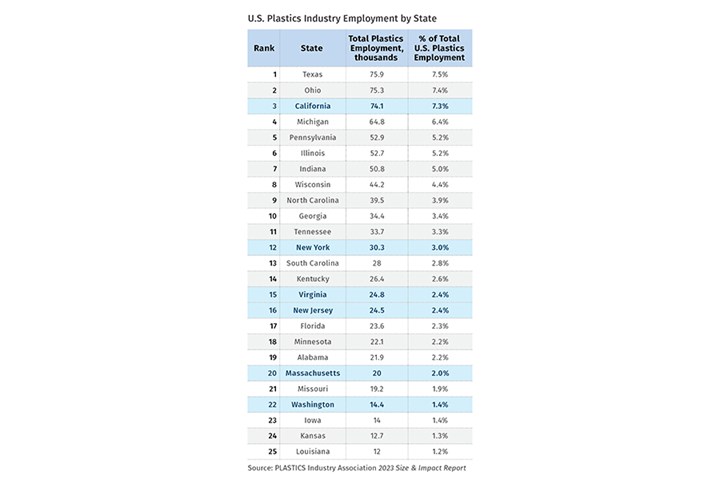
FIG 1 Six of the 12 states (highlighted in blue) with SNAP (or SNAP Equivalent) laws in place effective January 1, rank in the top 25 of plastics industry employment and combined account for nearly 20% of total U.S. plastics employment. Including the remaining six states (Colorado, Delaware, Maryland, Maine, Rhode Island and Vermont) not highlighted, new cooling fluid regs will impact close to 25% of total U.S. plastics employment. Photo Credit: Plastics Industry Association 2023 Size & Impact Report
Who is Affected in 2024
The most affected plastics processors on New Year’s Day are in the following states (see chart):
- States with GWP Laws Stricter than EPA SNAP: California, New York, Washington
- States with GWP Laws Equal to EPA SNAP: Colorado, Delaware, Maine, Maryland, Massachusetts, New Jersey, Rhode Island, Vermont, Virginia
- States with Refrigerant Legislation Pending: Connecticut, Hawaii, New Mexico, Oregon, Pennsylvania.
Effective Jan. 1, states that have enacted GWP laws are not letting businesses located within to purchase new units that use high-GWP refrigerants. Plastics processors in those states can continue to use existing equipment that relies on those refrigerants until that equipment reaches its end of life — but going forward, those businesses must purchase new equipment designed to use low-GWP refrigerants like R-454B and R-513A.
Plastics processors must make critical operational and budget decisions about when and how to purchase new chillers to comply with these new rules.
How We Got Here: The EPA and State Laws
The refrigerant ban that just went into effect stems from an EPA rule the agency announced in December 2016 and went into effect on Jan. 3, 2017. And on Oct. 5, the EPA announced a federal regulation that will further limit the GWP of refrigerants in new systems and equipment.
Pursuant to SNAP, the rule detailed more than 25 refrigerants deemed unacceptable in new centrifugal chillers and positive displacement chillers.
The EPA’s criteria for evaluating substitute refrigerants included atmospheric effects, exposure assessments, toxicity data, flammability and other environmental impacts, according to a comprehensive explanation of the rule in the Federal Register.
The SNAP program “evaluates the potential contributions to both ozone depletion and climate change” and “considers the ODP (Ozone Depletion Potential) and the 100-year integrated GWP of compounds to assess atmospheric effects,” the EPA explained. Furthermore, the program “uses exposure assessments to estimate concentration levels of substitutes to which workers, consumers, the general population and the environment may be exposed over a determined period of time. These assessments are based on personal monitoring data or area sampling data if available.”
According to an EPA spokesperson, the agency's final Technology Transitions rule under the AIM Act is applicable nationwide. Some states may have their own regulations in addition to EPA's rules, and these regulations may differ from the recently released EPA final rule, the representative explained, adding that the EPA regularly communicates with its state-level partners on this and other topics. EPA recommends reaching out to state-level officials for questions on state enforcement strategies and determinations.
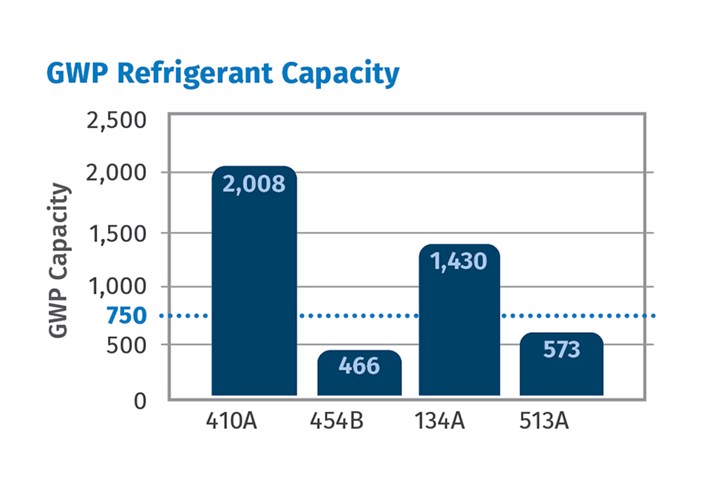
Acceptable Refrigerants By the Numbers
Different refrigerants have different thermodynamic properties and potential for flammability. Because of this, equipment must be designed from the ground up specifically to use these refrigerants; using a different refrigerant is not simply a matter of changing a compressor in an existing chiller.
GWP, which represents the capacity of a pollutant to harm the environment, is measured by how much more damaging the emission of one unit of a gas is compared with emission of one unit of carbon dioxide. With CO2 being assigned a value of 1, it becomes quite clear how much more damaging current refrigerants can be when considering the EPA’s desired limit of 750 GWP or less.
Processors will be allowed to use their existing chillers with now-banned refrigerants until the end of that equipment’s life cycle.
Comparing the GWP of previously acceptable refrigerants with the specs of their suitable replacements, we find:
• 410A: GWP of 2,088 versus 454B, with GWP of 466
• 134a: GWP of 1,430 versus 513A, with GWP of 573
Notably, 410A — the most commonly used refrigerant in 5-ton to 60-ton chillers — had been the “new green refrigerant” prior to this rule. Along with 134a (used primarily in small or very large chillers), 410A was classified as an A1 refrigerant, meaning it was neither toxic nor flammable. But with those refrigerants running afoul of the law in the previously noted states, plastics industry equipment manufacturers like us have had to respond by offering new chillers to comply with the latest GWP laws.
What This Means to You
These new refrigerant bans mean equipment makers and plastics processors have decisions to make.
For chiller makers, these rules mean equipment redesigns to incorporate new compressors and other components that run with low-GWP refrigerants. The opportunity therefore exists for chiller makers to refine various aspects of their products besides just making the compatible with low-GWP refrigerants. Upgrades can include:
• Simplified designs that can improve access to chiller components, thereby eliminating service difficulty, maintenance time and upkeep costs.
• Improved design geometries that can reduce chiller proportions — perhaps even reducing excessive shipping costs and making these units easier to install.
For plastics processors, this means making critical operational and budget decisions about when and how to purchase new chillers to comply with these new rules. Processors will be allowed to use their existing chillers with now-banned refrigerants until the end of that equipment’s life cycle. But as of Jan. 1, they will no longer be able to purchase chillers using those potentially damaging refrigerants. However, with newly redesigned chillers coming on the market, this could be a good time for processors in states not yet affected by these bans to get a jump on restrictions likely to be enacted in the future.
One final consideration for units that will use R-454B refrigerant: This is classified as an A2L refrigerant, so it is slightly flammable but nontoxic. So when purchasing these types of chillers:
• Make sure they are equipped with A2L leak detectors.
• Ensure areas where these chillers are used also have A2L leak detectors
• Follow proper safety procedures, including operating these chillers with good ventilation.
About the Author: Mark Johansen is vice president of marketing for the ACS Group, based in New Berlin, Wisconsin. He has more than 20 years of marketing and leadership experience in consumer and industrial products. Mark earned a bachelor’s degree in mechanical engineering from the Milwaukee School of Engineering and an MBA in marketing and finance from the University of Central Arkansas. Contact: 262-641-8600; mjohansen@acscorporate.com; acscorporate.com
Related Content
Follow These Best Practices When Working With Heat Transfer Fluids
Effectively choosing, operating and maintaining thermal fluid can positively impact productivity in plastics processing.
Read MoreCooling the Feed Throat and Screw: How Much Water Do You Need?
It’s one of the biggest quandaries in extrusion, as there is little or nothing published to give operators some guidance. So let’s try to shed some light on this trial-and-error process.
Read MoreHigh-Temperature, Low-Flow Indicator for Mold-Cooling Applications
Burger & Brown Engineering has released a new high-temperature low-flow indicator to monitor flow inside critical, restricted cooling paths such as those with bubblers or baffles.
Read MoreSystem Offers 'Lights Out' Mold-Channel Cleaning & Diagnostics
New system automatically cleans mold-cooling lines—including conformal channels—removing rust and calcium, among other deposits, while simultaneously testing for leaks, measuring flow rate and applying rust inhibitor.
Read MoreRead Next
Understanding Melting in Single-Screw Extruders
You can better visualize the melting process by “flipping” the observation point so that the barrel appears to be turning clockwise around a stationary screw.
Read MoreAdvanced Recycling: Beyond Pyrolysis
Consumer-product brand owners increasingly see advanced chemical recycling as a necessary complement to mechanical recycling if they are to meet ambitious goals for a circular economy in the next decade. Dozens of technology providers are developing new technologies to overcome the limitations of existing pyrolysis methods and to commercialize various alternative approaches to chemical recycling of plastics.
Read MoreHow Polymer Melts in Single-Screw Extruders
Understanding how polymer melts in a single-screw extruder could help you optimize your screw design to eliminate defect-causing solid polymer fragments.
Read More