How to Maintain Pelletizing Quality When Acid Attacks
Developments in the chemistry of polymers and additives have made corrosion a real problem in pelletizers. Here’s how to ward it off.
Underwater rotary pelletizers are increasingly being attacked by acid. The growing use of biopolymers is one reason for this trend, as materials such as PLA may contain free lactic acid. However, the problem involves commodity resins too, as their chemistry continues to evolve.
Over the last five years, maintenance technicians here have been working with customers pelletizing polyolefins that have reported unusual local damage to pelletizer die plates and other components. Issues that were originally thought to be limited to a few isolated cases are now becoming widespread. The root cause turns out to be acids used or created during production, and also antioxidants or other additives to control tails that are injected into the cooling water.
At its worst, chemical attack can destroy a die plate and bring production to a halt (Figure 1). Especially in large-scale polyolefin production, where pelletizers may be expected to operate for months at a time, such unplanned shutdowns are extremely costly.
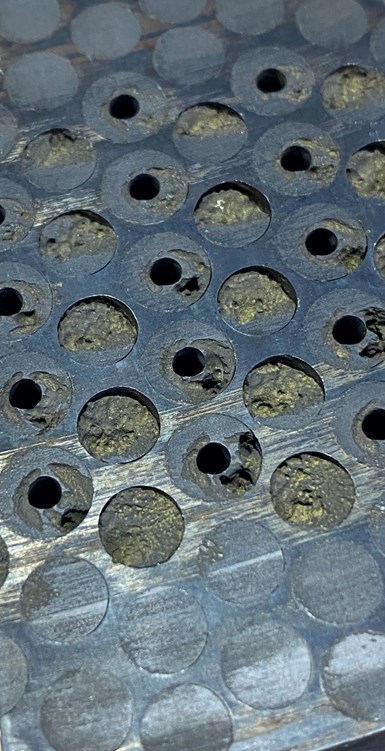
FIG 1 Acid attack has caused serious damage on the cutting face of this pelletizer. Photos: Maag
In the case of biopolymers, manufacturers and processors acknowledge that there is a lot still to be learned, so corrosion problems are less of a surprise — and the scale is generally rather small. For polyolefin producers, on the other hand, unexpected corrosion can be very bad news. An unplanned shutdown to change a die plate typically takes 24 hours or more, and at 100 tons/hour this can have serious knock-on effects for the upstream refinery. Clearly, it is better to anticipate corrosion issues before they trigger unplanned downtime.
Evolving Chemistry Is the Cause
The problem lies in today’s evolving polymer recipes and additive packages, as well as the growing popularity of biopolymers. These new products, undeniably more technical and complex, bring with them their share of production challenges. And where corrosion is concerned, these challenges often show up in the pelletization process — the link between polymer production and finished plastic products.
The key issue is that these new recipes may introduce acids in amounts that are sufficient to cause corrosion in key locations, while remaining difficult to detect in bulk materials.
It is better to anticipate corrosion issues before they trigger unplanned downtime.
Typically, cooling water circulating around the pelletizer remains neutral or alkaline, so manufacturers may not believe they have an acid problem. At the die plate itself, however, very local acid attack can damage critical areas around the extrusion nibs, even when there is little or no change in the bulk pH.
The underwater cutting head, composed of a die plate on the extruder side and a knife holder and knives on the pelletizer side, forms a set of wear parts. Their performance depends mainly on their ability to support a predictable number of thermal and mechanical stress cycles, leading to equally predictable maintenance and production continuity. However, with the development of new polymers or additives, new constraints and phenomena are emerging.
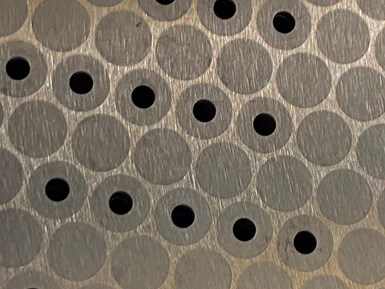
FIG 2 The cutting face of a new die plate. Note the sharp edges of the holes in the tungsten carbide nibs.
Even in cases less extreme than that of Figure 1, the sharp edges of the extrusion nozzles in a new die plate (Figure 2) can become rounded (Figure 3), leading to loss of cut quality and substandard pellets. This, in turn, may shorten equipment life from years to months, and even force unplanned shutdowns. Accelerated wear also causes poor pellet quality, which manufacturers may address by adding chemicals to control tails. Ironically, this can make the problem worse as the additives contribute to corrosion of the die plate.
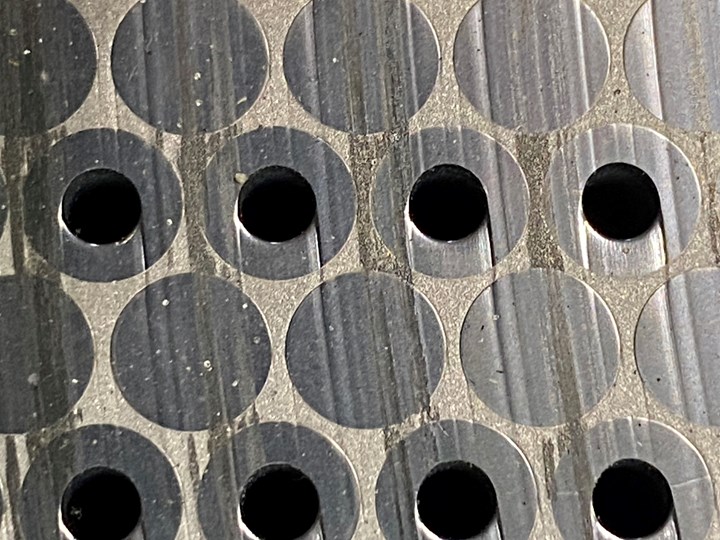
FIG 3 Cutting face showing accelerated wear due to local chemical attach, which has reduced the sharpness at the edges of the extrusion holes.
Choosing Materials to Resist Corrosion
Back in 1979, leading pelletizing suppliers began to use tungsten carbide for the pelletizer nibs, which is the area through which the polymer is extruded during the process. This was a breakthrough in terms of equipment life, thanks to the extreme hardness of the carbide material.
As it turns out, however, in some circumstances the tungsten carbide can be vulnerable to acid attack. Tungsten carbide is not a homogeneous material; typically, microscopic carbide grains are embedded in a matrix of metal or ceramic to provide mechanical strength and toughness. Not all grades of tungsten carbide are created equal, and under the wrong conditions the granular structure represents a gateway to chemical attack.
Allowing the knives to wear at a controlled rate makes them self-sharpening and protects the costly die plate.
The bulk of the die plate is traditionally made from stainless steel, and this too can be vulnerable to corrosion, along with the joints between the stainless steel and the tungsten carbide nibs. A solution is to make the die plates from superalloys such as Hastelloy or Inconel, and the extrusion nibs from grades of tungsten carbide chosen for their corrosion resistance. We also pay attention to the brazing process used to attach the nibs.
The resulting Hybrid Acid Resistant (HAT) die plate (Figure 4) combines standard stainless steel for strength with Inconel and high-performance tungsten carbide for ultimate corrosion resistance.
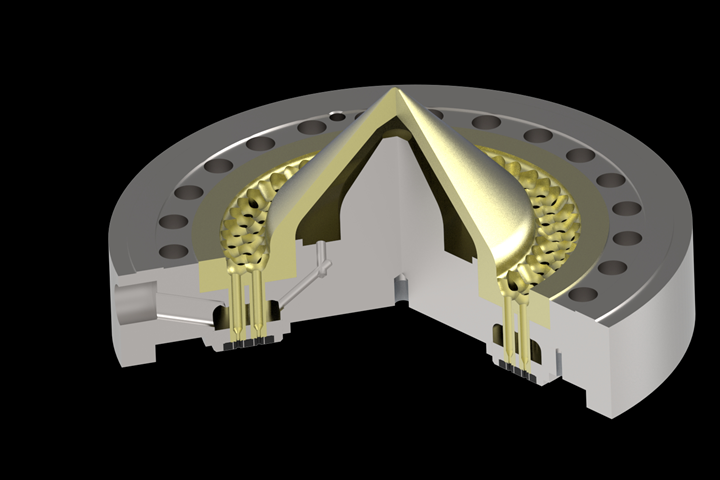
FIG 4 Die plate incorporates parts made from solid Inconel for maximum corrosion resistance.
Thanks to the use of solid materials instead of surface treatment, the HAT die plate has been proven to significantly increase die-plate life while reducing shutdowns and off-spec pellets. In practice, the die plates can last up to 10 times longer, provided they’re traditional equivalents under corrosive conditions and, in some cases, the improvement has been dramatic. One PLA manufacturer, for instance, was originally able to run for just five days before the die plate needed to be reground. With updated materials, the material supplier can now achieve six months before regrinding.
The Complete Pelletizing System
Of course, the die plate is only part — although a very important part — of the complete pelletization system. For instance, another key engineering decision is to make the cutting knives from a titanium carbide composite that is less hard than the tungsten carbide nibs. Enabling the knives to wear at a controlled rate makes them self-sharpening and protects the costly die plate.
An example is the Central Injection System (CIS) shown in Figure 5. With a die plate 1,500 mm in diameter and a central water injection system, this handles throughputs up to 100 tons/hour with up to 30% longer service life compared to traditional solutions.
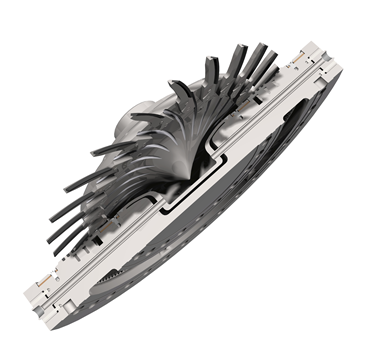
FIG 5 Cutting-head system with central water injection.
CIS includes a self-aligning knife holder with a grooved cone and sword-shaped knives. It is an effective solution for high melt index or peroxided polymers. Water is directed through the die plate toward the cutting face, improving pellet cooling and ejection. By making use of the existing process water supply, the CIS system contributes to reducing waste and water consumption.
Trace quantities of acids resulting from new polymers, new blends and new additives can cause expensive damage to pelletizer die plates and, in some cases, other equipment along the production chain. To reduce costly shutdowns, careful attention to materials choice can improve the corrosion resistance of die plates and other key items.
About the Authors: Pierre LeRoy has been head of engineering role at AMN since 2021. In that role, he leads a team of engineers tasked with choosing the optimal design for each customer’s application. LeRoy’s team drives quality by ensuring product performance, on-site installation, operators' training and technical assistance. Contact: maag.com
Margaux Pierens is the director of operations at AMN based in Normandy, France. She worked at AMN in 2015 prior to moving to the U.S. While in the U.S. she spent time working in both New York and Texas and in 2018 returned to AMN, France.
Related Content
How to Configure Your Twin-Screw Barrel Layout
In twin-screw compounding, most engineers recognize the benefits of being able to configure screw elements. Here’s what you need to know about sequencing barrel sections.
Read MoreHow to Configure Your Twin-Screw Extruder: Part 3
The melting mechanism in a twin-screw extruder is quite different from that of a single screw. Design of the melting section affects how the material is melted, as well as melt temperature and quality.
Read MoreConfiguring the Twin Screw Extruder: Part 4
For many compounding operations, material is fed to the extruder at the feed throat. This is the case when feeding a single polymer or a blend of polymers mixed with solid additives. Some ingredients, however, present a challenge in feeding. Here’s how to solve to them.
Read MoreHow to Configure Your Twin-Screw Extruder -- Part 2
Follow these tips to configure your twin-screw elements to promote feeding and solids conveying.
Read MoreRead Next
The Path to Pellet Perfection
In underwater pelletizing, numerous variables in the equipment, process and material affect pellet shape, consistency and quality factors such as fines. Defining the “perfect” pellet depends on the conditions of end use, and achieving that ideal requires understanding of the causes of imperfections.
Read MoreMitigating and Troubleshooting Underwater Pelletizing Issues
There’s a shift to underwater pelletizing systems as compounders strive to produce higher-quality pellets. But underwater pelletizers are not general-purpose tools. Follow these steps to help ensure you maintain throughput, pellet quality and efficiency.
Read MoreHow Polymer Melts in Single-Screw Extruders
Understanding how polymer melts in a single-screw extruder could help you optimize your screw design to eliminate defect-causing solid polymer fragments.
Read More