Vacuum System Gives Molds a Chance to Vent
When the in-house vacuum systems and tooling tricks that NMC Dynaplas usually deploys to deal with trapped gas failed, it turned to a Mold-Vac system and saw reject rates go from 44% to zero.
The first time NMC Dynaplas Ltd. was introduced to Mold-Vac LLC’s Mold-Vac System for vacuuming trapped gas from molds and blowing clogged vents clear, it was impressed, but not in the market, since it was content with the in-house vacuum systems and toolmaking know-how it typically applied to deal with off-gassing materials in the mold.
Then the Toronto-based company, which injection molds under-hood automotive systems that entail high-temperature molding of engineering resins, took on a project from the Schaeffler Group, a German automotive, aerospace and industrial OEM. Tooling for the project involved roughly a dozen different thermal-management system components.
Dynaplas has worked with a wide range of high-temperature engineering thermoplastics, ranging from PEEK and PAI to acetal and various nylons. For the Schaeffler job, the parts called for polyphenylene sulfide (PPS), which “flows like water,” according to Richard Davison, Dynaplas director of product engineering. Thus, if the mold’s 0.0002-in. vents are opened even a little, parts will flash, which is unacceptable in these applications, given the risk that flash could flake off and contaminate and/or clog a fluid system.
The challenges of molding PPS got Davison and Dynaplas thinking back to the sales call from Mold-Vac in a new light. “Fast forward five years to the Schaeffler job,” Davison says, “and we thought we should revisit the Mold-Vac unit because our vacuum systems just were not powerful enough and we were experiencing reject rates of up to 44%.”
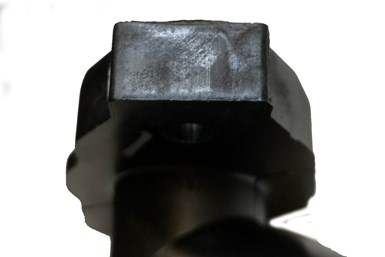
PPS part shows noticeable flash prior to Dynaplas installing Mold-Vac system.
Dynaplas was experiencing those reject rates despite changing the tool’s vent depth to improve venting performance and even sacrificing cycle time to give the cavity more chance to expel off-gas. Beyond its own vacuum systems, Dynaplas also created elaborate seals for the parting line to ensure that only gases from the mold were venting and not outside air. None of that seemed to be enough, however.
Where the previous system left Dynaplas wanting in the power department, the new Mold-Vac system brought more than enough oomph. “One nice thing about the Mold-Vac unit is that it’s very much like using a tank to squash a ladybug,” Davison says. “I mean you’re just overpowering the system—that’s really the whole secret—it’s just horsepower.”
Today, with the Mold-Vac system, Dynaplas says its reject rates are now zero, with some other ancillary benefits beyond less scrap. The Mold-Vac unit has both vacuum and blow-back modes, so molders can draw vacuum during pre-fill and then can blow back to clean the tool’s vents. “It’s actually very nice in that it helps maintain or lengthen the life of your vent cleanliness and reduce the maintenance cycle,” Davison says.
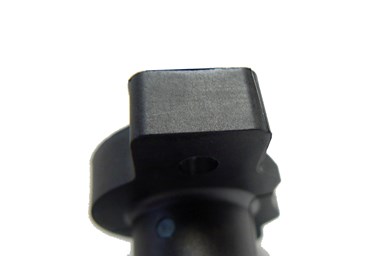
PPS part after Dynaplas installed Mold-Vac system shows dramatic reduction in flash, reducing the molder’s reject rate to zero.
The Schaeffler job went from being a source of scrap and headaches to running virtually unattended, Davison notes. The power of the Mold-Vac has also allowed the company to simplify new mold designs, eschewing sealing mechanisms with the knowledge that steel-to-steel shutoff at the parting line is sufficient.
Since that initial Mold-Vac purchase, Dynaplas has acquired more units and is designing most new tooling with ports to receive the Mold-Vac, should it become necessary. “It is very easy to apply Mold-Vac to existing tooling, and it’s not that big a financial hit to buy one,” Davison says. “Plus it’s portable so you can wheel it around your plant from machine to machine.”
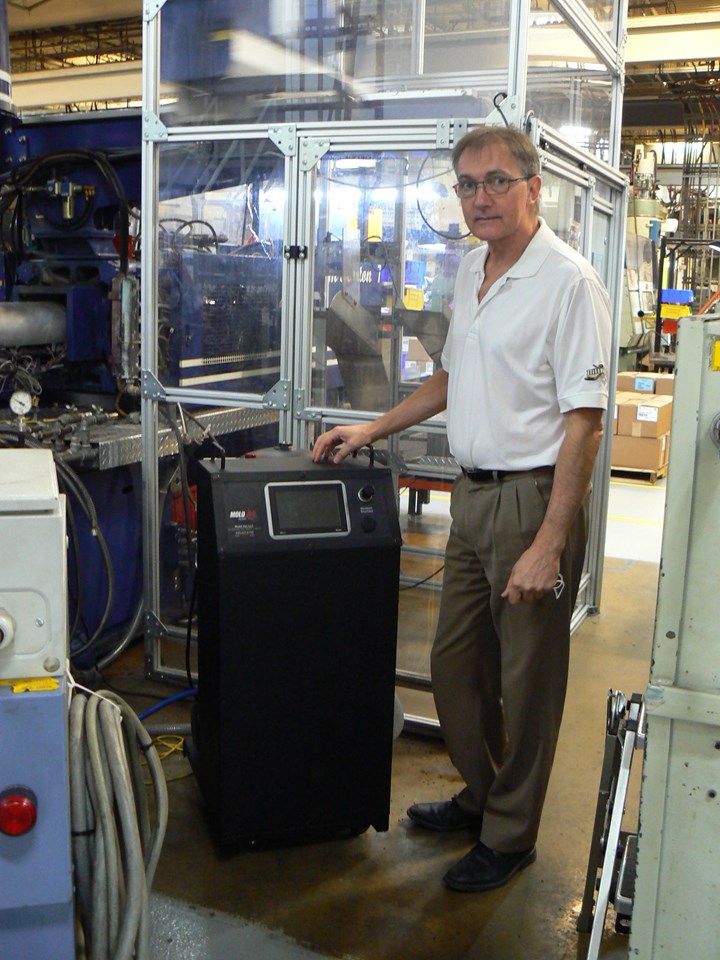
Dynaplas’ Richard Davison points out that one benefit of the Mold-Vac system for evacuating gas from tools and blowing tool vents clean is its portability. (Photo: Mold-Vac)
Related Content
Best Methods of Molding Undercuts
Producing plastics parts with undercuts presents distinct challenges for molders.
Read MoreHow to Reduce Sinks in Injection Molding
Modifications to the common core pin can be a simple solution, but don’t expect all resins to behave the same. Gas assist is also worth a try.
Read MoreHow to Stop Flash
Flashing of a part can occur for several reasons—from variations in the process or material to tooling trouble.
Read MoreRead Next
How to Fix Outgassing Problems in Injection Molding
Gas and air entrapment can cause a variety of problems in injection molding, including part burns, short shots, voids and blemishes, even clogged vents. Vacuum venting can solve all these problems, and increase output in the molding process.
Read MoreVacuum Venting Keeps Molds Running Longer
In tough economic times, facing hungry competition here and abroad, molders cannot afford to ignore preventable problems that slow cycles, cost machine downtime and mold maintenance, and waste material on reject parts.
Read MoreProcessor Turns to AI to Help Keep Machines Humming
At captive processor McConkey, a new generation of artificial intelligence models, highlighted by ChatGPT, is helping it wade through the shortage of skilled labor and keep its production lines churning out good parts.
Read More