Proper Vacuum Receiver Selection Impacts Central System Operation
Vacuum receivers are an integral part of any central conveying system. As such, it is important to understand:
- Types of receivers
- Basic receiver features
- How receivers operate
- Troubleshooting procedures
Vacuum receivers, also called vacuum chambers, vacuum stations, or just stations, are integral parts of a central conveying system. Think of them as intermediate holding points for resins conveyed by vacuum. Vacuum receivers have one primary job: separate material from air. They accept resin from a source that is pulled by vacuum, separate the material from the air flow and transfer that resin to a destination.
Vacuum receivers come in several designs with all sorts of features aimed at offering a variety of advantages in conveyance, maintenance, and ease of use. Some receivers are designed for pellets, some for regrind, and others for powders.
Some receivers mount atop hoppers or bins; others are mounted directly to the throat of a processing machine.
All receivers have a sequencing device. Some receivers require a separate sequencing valve to connect to the vacuum line; others have a built-in fill valve. The sequencing device allows vacuum to pull material into the receiver and while the bulk of the material falls to the bottom of the receiver, the vacuum pulls the air up through the top of the receiver and back to the vacuum pump.
Most dust and fines are trapped by a filter but there are also Filterless Receivers.
Receivers come in various capacities, from small (1.5 lb.), to medium (75 lb.), to large (114 lb. and more). The multitude of designs, capacities, and feature sets is what makes it possible to specify a vacuum receiver that perfectly matches the needs of a plastics conveying system.
Major Parts of a Receiver
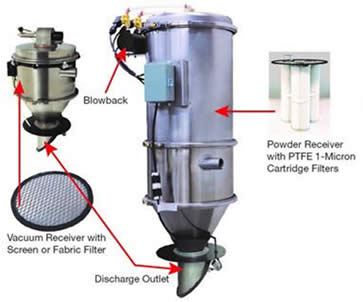
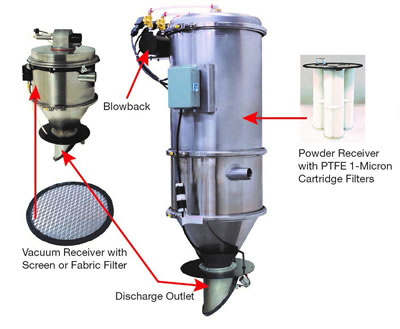
1) Receiver lid - allows access to the receiver chamber. Access is necessary to clean and/or change filters, if present, and perform other maintenance within the receiver. The lid can be hinged or completely removable, and typically can be rotated to the orientation required by the layout of the conveying system.
2) Vacuum breaker or sequencing valve - at each receiver directs vacuum to that receiver. The vacuum draws resin through the conveying lines to the vacuum receiver. Sequencing valves can be either a “T” valve located above the receiver in the vacuum line or an external fill valve (EFV) located right on the receiver lid.
3) Receiver chamber or body - is usually a cylinder connected to cone-shaped lower section - that collects resin from the conveying system before discharge. The slant of the cone helps material slide down to the discharge valve.
4) Machine-mounted receivers – typically have a glass hopper and are connected directly to the throat of the process machine. Often referred to as J.I.T. receivers.
5) Filter or some type of filter-less system - separates powders, dust, fines, and other contaminates from the resin entering the receiver. The filter-less receiver shown below uses a cyclonic action to separate material from the air flow. The material is heavier than air so it falls into the body of the receiver while vacuum and cyclonic action pulls the air into the vacuum stream.
6) Material level switch - detects the amount of resin in the machine-mount receiver and controls the discharge of the resin. The mechanism to detect the level of material in the receiver can range from simple, non-automated devices to sophisticated electronically controlled sensors.
7) Discharge valve – allows collected resin exit the receiver chamber. The resin can be dispensed to a hopper or some other type of container. Machine-mount receivers typically gravity-feed directly to the throat of the process machin
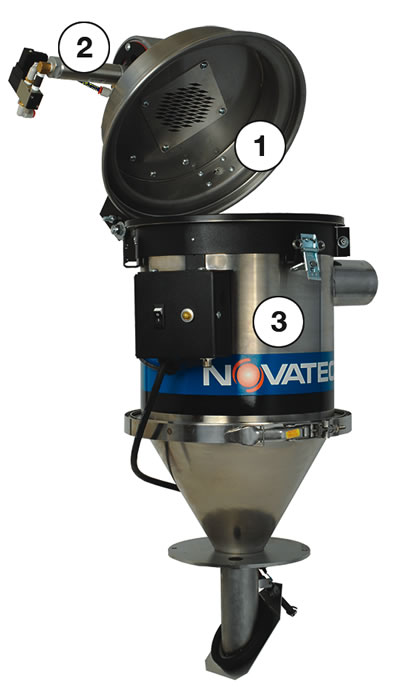
This receiver has a hinged lid with a built-in sequencing/fill valve
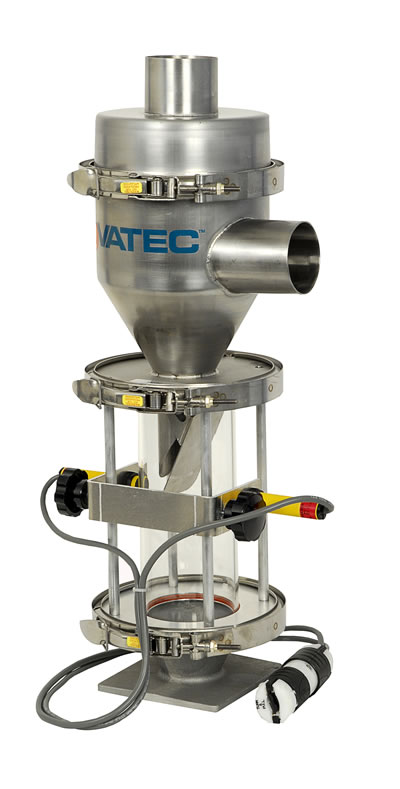
Machine mount receivers feed material directly to the process machine throat.
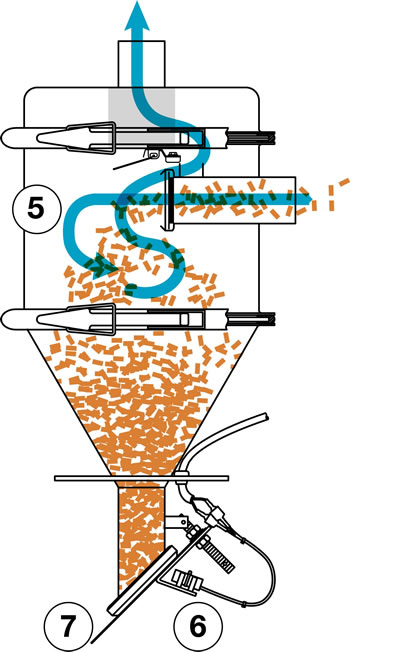
Filterless receivers use a cyclonic principle to separate air from the material stream.
More on Filterless receivers:
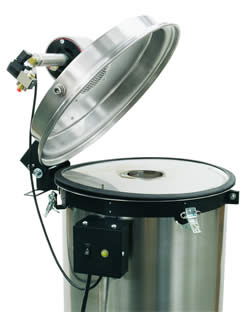
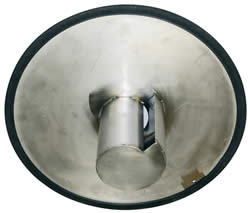
There are two distinct styles of filterless vacuum receivers. The “removeable-lid’ receivers require a separate vacuum sequencing valve (“T” valve) while the very popular hinged-lid models that have a built-in sequencing valve.
In either case, going filterless eliminates the necessity of cleaning filters and the filter replacement costs. A filter is not required because these models use a cyclonic action to separate the material from the air flow. In addition, a Blowback option is not required so that cost is eliminated.
There are other features that should be considered like; a stainless steel body which provides an attractive scratch-resistant surface; a tangential material inlet with a gasketed check valve that minimizes degradation of material while also minimizing harm to the receiver walls.
The hinged lid models are popular because the lid swings up and locks in place so the interior of the receiver can be safely cleaned after material changes. Some also have a local ON/OFF switch so the operator does not have to walk to a central control to turn the unit OFF.
When conveying particularly abrasive materials, either style is available with extended wear ceramic coated options that are bolted in place and can be replaced, when necessary.
The removable lid models are available in capacities of 1/3 to 3 ft3 while the hinged lid models are available from 1/3 to 2 ft3. Machine mount styles are available with multiple glass sizes for most models.