Arburg Showcases Partnership Aimed at Simplifying End-of-Life Recycling
To be presented at VDI’s international congress for plastics in automotive, Arburg will discuss its collaboration with Reifenhäuser’s R-Cycle Project.
At the PIAE Europe congress this September, Arburg will discuss its collaboration with Reifenhäuser on the R-Cycle project, specifically efforts to add a “digital product passport” to molded components to simplify their sorting at end of life. Organized by the Association of German Engineers (VDI), the PIAE Europe congress will be held in Mannheim, Germany from Sept. 8-9.
Extrusion equipment supplier Reifenhäuser announced the multi-company R-Cycle effort last November, describing it as a data-driven approach to allow high-quality recycling derived from improved waste sorting. In addition to Arburg, the initiative also includes fellow extrusion equipment supplier Brückner and blow molding machine maker Kautex, as well as the IKV, Germany’s plastics research institute, at RWTH Aachen University.
Arburg, which said it is the only mechanical engineering partner on the project, will discuss the creation of a “smart” turnkey system based around an electric Allrounder 370 A molding inline-printed cups that are 100% traceable and can be separated by type.
Arburg’s Bettina Keck told Plastics Technology that for the cup application, the DM code is printed together with the picture motif on the injection molded part. This code can be read by a camera system at the recycling plant, with all the information transferred to a global database during the production process. Each part receives an individual ID giving it a unique “passport” that is stored in the cloud, making real-time data acquisition possible during its whole life cycle.
This code would give recyclers all the information they need about the part to properly sort it for reclaim, including the resin and additives used, and detailed data about those aspects, including the resin’s melt flow index, for example. The recycling plant can then correctly separate the plastic waste by reading this code.
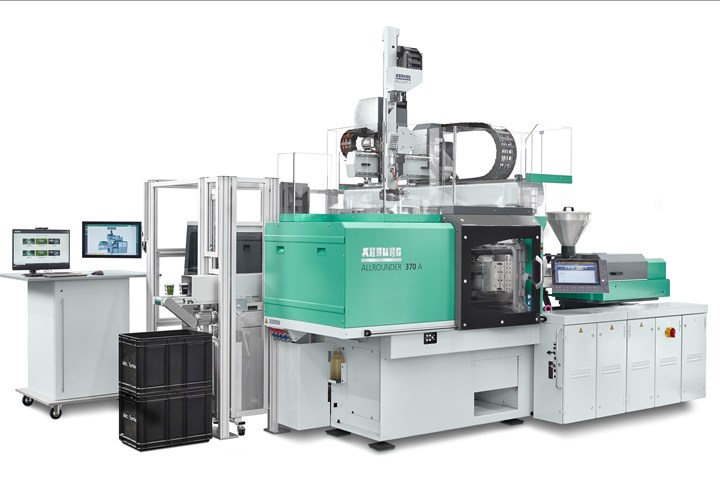
As part of the R-Cycle project, Arburg created a turnkey system based on an electric Allrounder 370 A molding inline-printed cups that are 100% traceable and can be separated by type.
Related Content
-
Recycled Material Prices Show Stability Heading into 2023
After summer's steep drop, most prices leveled off in the second half.
-
Film Extrusion: Boost Mechanical Properties and Rate of Composting by Blending Amorphous PHA into PLA
A unique amorphous PHA has been shown to enhance the mechanical performance and accelerate the biodegradation of other compostable polymers PLA in blown film.
-
Avoid Four Common Traps In Granulation
Today, more than ever, granulation is an important step in the total production process. Our expert explains a few of the many common traps to avoid when thinking about granulators