Conair: Going All In on AI
A dozen new products debut at NPE, but the company says new AI-based conveying technology is the true game changer.
With 12 new products about to be unveiled at its booth, there was plenty for Conair to talk about during its press conference the Sunday before NPE2024. But the auxiliary equipment innovator was most excited to tout its first-of-its-kind conveying system that utilizes artificial intelligence (AI) to manage changing conveying conditions.
“When Conair went to NPE2018, all the buzz was about Industry 4.0,” says Sam Rajkovich, vice president of sales and marketing. “We’re still installing Industry 4.0 solutions for customers, and we’re still refining that product. It’s still a very relevant technology, but there’s this new topic that is entered the manufacturing space, which is artificial intelligence. Since the pandemic, we’ve spent a lot of time developing products that make use of things like sensor technology and advanced controls, so that controls essentially take over the operation of the equipment and make informed decisions about how the equipment is going to operate without operator input. That way, the equipment is always maximizing its performance to the betterment of the plant operation.”
Conair calls its solution “Conveying with Optimizer.” It’s a patented AI-driven feature for material handling systems using the Conair SmartFLX conveying control. Now, a SmartFLX conveying control equipped with the Optimizer package automatically detects source-to-destination conditions (vacuum, receiver distance, material bulk density and other factors) then autonomously adjusts the conveying system in real time to move material under optimal conditions. This breakthrough AI-driven conveying system feature is fully operational in a live demonstration at the Conair booth.
Rajkovich continues, “We introduced Wave Conveying technology in 2016, but Conveying with Optimizer is a new spin on how customers could convey. It adds sensor technology and advanced controls technology to the conveying algorithm that we’ve developed, and essentially what it can do is it can use the sensor technology and control technology to do things that previously were unheard of. Let’s say that over time you develop a leak in your conveying line. This control technology will recognize the leak and self-adjust and give you the same rate and conveying output that you received with a leak in your conveying line that you received prior to having a leak in your conveying line. It'll still give you an alert, but it essentially will handle the leak as if it didn’t exist and allow you to continue to make the same rate.”
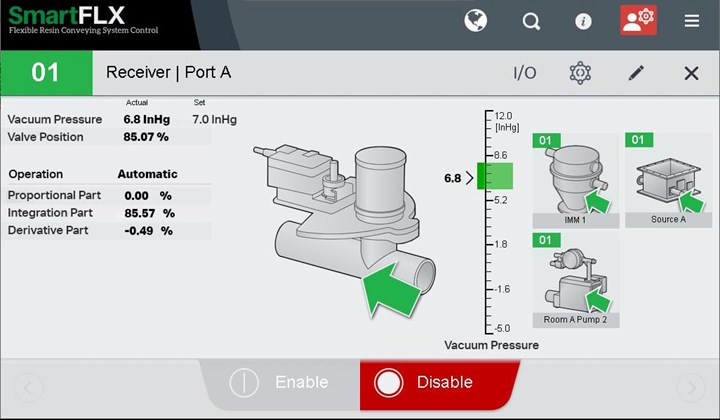
The autonomous capabilities of the Conveying with Optimizer feature were designed to overcome the trickiest, most labor-intensive part of conveying operations: the need to manually adjust air and material ratios (using manual air valves) from source to destination. In practical terms, that means operators must constantly change settings on distribution boxes, pickup boxes or gaylord wands to move material amid constantly changing system conditions.
When systems are properly tuned and when operators guesstimate right, material usually moves predictably. But an incorrect manual adjustment or any number of other changes — conveying distance, material bulk density/regrind ratio, relocated equipment or even a minor vacuum leak caused by a hose or coupling — can spell conveying problems that result in downtime: empty receivers, clogged lines, overloaded pumps, resin losses or excessive system wear.
The AI built into Conveying with Optimizer replaces error-prone human decisions, instead making autonomous system adjustments that move material while compensating for typical conveying system faults. The Optimizer package combines novel software, hardware, sensors and intelligence with the high-speed computing power of the SmartFLX control. Together, these elements sense, calculate and compensate for changing conditions far faster than a human could, while ensuring optimal air/material ratios and trouble-free conveying. And, the machine learning capability of the Optimizer feature enables it to continually refine and perfect each conveying cycle over time.
So, it’s no longer necessary for a processor to pay an operator to walk to the material distribution box, make a feed tube adjustment and then walk to the conveying control to issue a command. Now, the operator simply enters the command — locally on the SmartFLX control or remotely via Conair SmartServices on a connected device — and leaves the Conveying with Optimizer intelligence to figure it out and complete the conveying cycle.
The only prerequisite for Conveying with Optimizer is a conveying system equipped with a SmartFLX control. The Optimizer package may be ordered with a SmartFLX control from the factory or installed to an existing SmartFLX control in the field. Optimizer hardware, which is available in line sizes from 1.5 to 4 inches OD, is installed at material pickup points, while Optimizer software upgrade is loaded into the SmartFLX control
Related Content
Resin-Selection Station Conveys Material on Demand
NPE2024: Powerful, space- and labor-saving station makes the connections and conveys material automatically on command.
Read MoreHow to Effectively Reduce Costs with Smart Auxiliaries Technology
As drying, blending and conveying technologies grow more sophisticated, they offer processors great opportunities to reduce cost through better energy efficiency, smaller equipment footprints, reduced scrap and quicker changeovers. Increased throughput and better utilization of primary processing equipment and manpower are the results.
Read More‘Digitalization’ – Awkward Term for a Vital Concept
At K 2022, 85 machines from 40 companies showed off their Industry 4.0 capabilities via OPC-UA interface. A new universal interface for Material Supply Systems was revealed at the show.
Read MoreConveyor Controller Ideal for Expanding Plants
Billed as the most flexible and reliable discrete wired conveying controller on the market.
Read MoreRead Next
Why (and What) You Need to Dry
Other than polyolefins, almost every other polymer exhibits some level of polarity and therefore can absorb a certain amount of moisture from the atmosphere. Here’s a look at some of these materials, and what needs to be done to dry them.
Read MoreHow Polymer Melts in Single-Screw Extruders
Understanding how polymer melts in a single-screw extruder could help you optimize your screw design to eliminate defect-causing solid polymer fragments.
Read MoreLead the Conversation, Change the Conversation
Coverage of single-use plastics can be both misleading and demoralizing. Here are 10 tips for changing the perception of the plastics industry at your company and in your community.
Read More