Joint Trial by Syensqo and Tomra Separates Multilayer PVDC Film From Polyolefins
Results apply to shrink film for consumer and food packaging.
Seynsqo, the product of multinational chemical company Solvay’s 2023 split, announced succesSful feasibility testing for sorting PVDC packaging waste, conducted with Tomra. The purpose of the testing was to demonstrate the technical and economic feasibility of separating and sorting multicomponent plastic structures in which polyvinylidene chloride (PVDC) serves as a barrier layer.
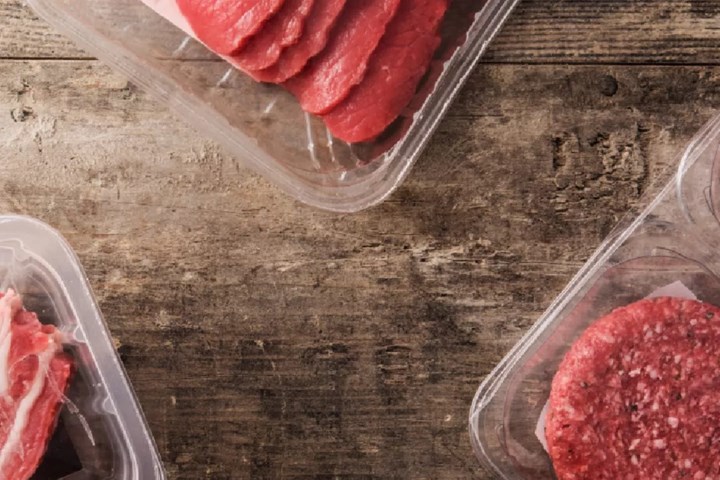
Barrier shrink films such as those used in food packaging are related applications. Source: Syensqo
The partners developed a joint set of experiments with multilayer samples of commercial packaging waste consisting of LDPE and Syensqo’s Ixan PVDC. According to Syensqo, results show that multilayer films containing PVDC can be separated from mixed plastic waste using industrial sorting equipment to achieve clean-grade polyolefin and PVDC recycling streams.
“The overall target of this project was to challenge major industry standards which claim that multilayer PVDC films cannot be sorted out of multilayer packaging structures,” explains Federico Baruffi, global marketing manager, specialty polymers, at Syensqo. “Our experiments have demonstrated the contrary and are sending a clear message to the packaging and recycling industry that it can be done, notably with good accuracy and repeatability using existing industrial technology.”
The positive results apply to markets that are currently generating multilayer mixed plastic waste containing PVDC, such as shrink films in consumer and food packaging.
“One of the concerns in the recycling industry was the reliable identification of polymeric waste with PVDC content,” adds Marco Gregori, area sales manager at Tomra Recycling Sorting. “By combining our advanced optical and near-infrared detection systems, we managed to achieve a selectivity rate of more than 80% when sorting from postconsumer plastic mix and more than 95% when sorting from LDPE monolayer stream. This is yet another example of what today's technology, in this case our Autosort, can already do.”
Related Content
-
Advanced Recycling: Beyond Pyrolysis
Consumer-product brand owners increasingly see advanced chemical recycling as a necessary complement to mechanical recycling if they are to meet ambitious goals for a circular economy in the next decade. Dozens of technology providers are developing new technologies to overcome the limitations of existing pyrolysis methods and to commercialize various alternative approaches to chemical recycling of plastics.
-
A Recycling Plant, Renewed
Reinvention is essential at Capital Polymers, a toll recycler that has completely transformed its operation in a short period of time.
-
SD Polymers: 'One-Stop Solution for Mechanical Recycling'
‘Passionate’ recycler invests in people and technology to meet commitment to innovative, sustainable solutions for its processor customers.