Dual Injection Units on a Smaller, Electric Press for 2K Medical Molding
Engel extends its combi M dual-injection unit technology to a smaller tonnage machine with a horizontal indexing table for the first time at K 2022.
Saying the cell displays maximum output from a minimum footprint in an energy efficient and cleanroom suitable manner, Engel is displaying an all-electric e-motion 160 injection molding machine that utilizes its combi M dual injection technology to mold 2K sample vessels for medical diagnostics at K 2022.
In a release, the company noted that where it had previously only offered the combi M design for larger molding machines, it would presenting the multimaterial molding platform on an injection machine with just 160 tons of clamp force and a horizontal indexing table for the first time.
The combi M’s indexing table divides the machine’s mold closing area in the center allowing two molds to operate in parallel. With this design, the combi M technology can perform two-component molding or double the output from identical molds. Equipped with two injection units as standard, combi M’s feature one injection unit on the stationary platen, with the auxiliary unit on the moving platen.
At the show, the primary cylindrical cavitiy parts of the diagnostic product are injected in the first shot using a polycarbonate with black dye. After the indexing table rotates 180°, the cylinders are sealed with lenticular covers molded from transparent PC in the second shot. While this is occurring, the next set of black barrels are molded on the other side. The two molds, with 32 cavities each, come from German moldmaker Hack Formenbau and will deploy its Moldlife intelligent mold software with direct integration into the press’s controller.
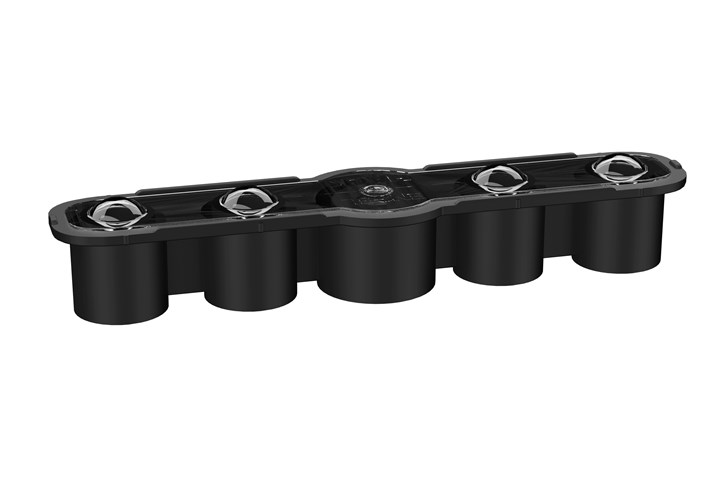
Featuring transparent and black polycarbonate, Engel will mold this medical diagnostic part at K 2022.
Photo Credit: Engel
In this instance, the total machine footprint is cut by more than 20%, with the combi M horizontal indexing table saving floor space where multiple-cavity molds are used. Engel notes that a comparable 32-cavity mold with a vertical rotary table would have needed an e-motion press with at least 280 tons of clamp force. Beyond saving valuable cleanroom space, the smaller machine consumes less energy.
Using a standardized design, Engel also built a compact automation cell around the press. At the show, two robots are work in tandem to manufacture the diagnostics products, with an Engel viper 20 linear robot removing and depositing the 2K parts in trays. Next, an Engel e‑pic pick-and-place robot covers filled trays with an intermediate layer so they can be stacked in boxes and discharged via an integrated tray server.
Dynamic Control
The cell will feature a number of Engel’s Inject 4.0 smart assistance programs, including the newly developed Parameter Limits feature as part of its iQ process observer. In medical and pharmaceutical molding, processors are required to validate a process and then show documentation that newly molded parts were produced under those validated process conditions. Engel notes that not only do its smart assistance systems optimize individual molding steps, but they also keep track of the entire process, analyzing several hundred parameters simultaneously, displaying any deviations that impact quality. Engel says that it considers its iQ process observer to be one of the first applications of artificial intelligence in injection molding and notes that even validated processes can be dynamically controlled—making real-time changes to the process without moving beyond critical, validated setpoints. Engel says key to such dynamic yet validated control is the definition of process windows instead of setting concrete values for parameters to be retroactively adjusted.
To that end, Engel says it developed the new Parameter Limits feature in order to keep all preset values constant with a defined process window. With the help of the new software, a process window can be defined for up to 150 individually selectable process parameters using the machine’s CC300 controller. This allows tolerance limits to be directly available on the press when production starts and ensures they are reliably met.
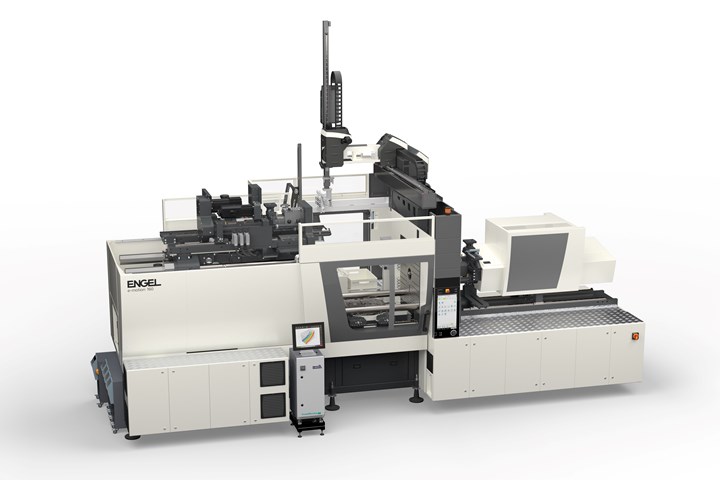
At K 2022, Engel will extend its 2K combi M technology to a smaller tonnage—160—press for the first time for a multicomponent medical part molded from a small footprint.
Photo Credit: Engel
Related Content
Use Cavity Pressure Measurement to Simplify GMP-Compliant Medical Molding
Cavity-pressure monitoring describes precisely what’s taking place inside the mold, providing a transparent view of the conditions under which a part is created and ensuring conformance with GMP and ISO 13485 in medical injection molding.
Read MoreKrones Acquires Netstal
Krones adds PET preform injection molding to its bottle blowing and filling capabilities, as well as cap molding and expansion into medical, food and other markets.
Read MoreNew Cap for Child-Resistant Pill Bottles Is Senior-Friendly & Saves Resin
Exclusive lightweight cap design can be removed simply pushing down on the center. No gripping or twisting needed.
Read MoreMedical Manufacturer Innovates with Additive Manufacturing and Extrusion Technology Hubs
Spectrum Plastics Group offers customers two technology hubs — one for extrusion, the other for additive manufacturing — to help bring ground-breaking products to market faster.
Read MoreRead Next
K 2022 Preview: Injection Molding Closes the Circle, Digitally
Because the market requires sustainability—and important component of which is the circular economy—and sustainability requires digitization, all three will be major themes at injection molding booths at K 2022.
Read MoreEngel Introduces iQ hold Control
New smart assistant and part of the iQ suite of technologies automatically determines the optimum holding-pressure time in injection molding.
Read MoreAnswering the Sustainability Challenge with Digitalization
Attendees in the molding halls of K can count on exhibits that address two main themes: digitalization and sustainability. Digitalization in the form of smarter pieces of equipment communicating with each other and with plant personnel; and sustainability in the form of greater energy efficiency and the ability to process recycled and renewable resins.
Read More