New PET Stretch-Blow System Saves Energy & Downtime, Aids rPET Use
New-generation Contiform PET stretch-blow molding machine from Krones is designed for sustainability throughout.
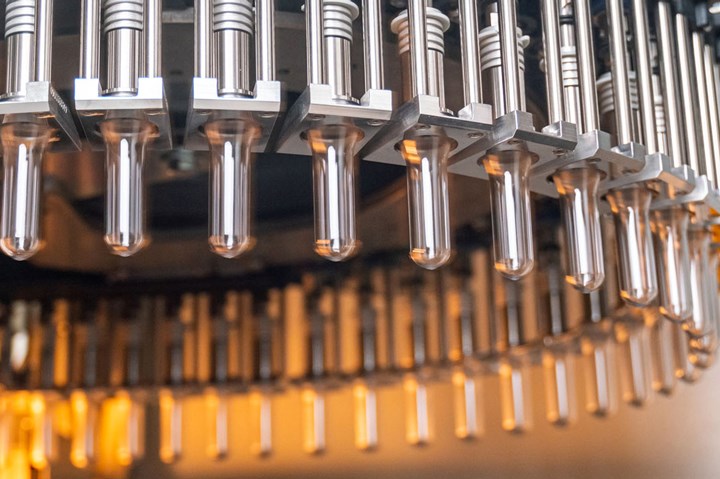
Krones’ Fourth-generation Contiform PET container machine reduces energy for heating and blowing, reduces scrap and downtime, and automatically compensates for rPET variations. (Photo: Krones)
The new fourth-generation Contiform rotary stretch-blow molder from Krones is said to be more efficient, more operator-friendly and more environmentally compatible than ever before. Firstly, it addresses two key factors in energy consumption: heating and compressed-air usage in blowing. The oven has been made more compact, spacing the heaters closer together, and the heaters have been redesigned with parabolic reflectors. The result is 11% lower energy consumption in heating compared with the previous Contiform generation, Krones says.
In addition, the new Air Wizard Triple air-recycling system is a three-stage system that reportedly cuts compressed-air consumption by up to 20%.
And Krones’ new Contiloop AI is an automatic process-control system that uses artificial-intelligence software and newly developed hardware to detect even the slightest variation in material distribution in PET containers and automatically adjusts processing parameters in real time to maintain bottle quality. These capabilities are especially valuable in compensating for variability in rPET raw materials, according to the company.
To top off the “green” features of this machine, the protective panels are made of recycled plastic.
The new Contiform is friendly not only to the environment but also to operating personnel. It features a large-screen interface with the latest touch technology and improved visualization software. Virtual assistants guide operators through setup, even making automatic suggestions.
New “skip-and-run” technology monitors the mold-hanger locking device and allows a blowing station that is not locked—such as because of a defective preform—to pass along the main cam (e.g., to eject the bad preform) without triggering an emergency stop of the entire machine. That considerably reduces scrap, downtime and labor costs.
Related Content
-
50 Years...600 Issues...and Still Counting
Matt Naitove marks his first half-century in plastics reporting, with a few of his favorite headlines.
-
Solve Four Common Problems in PET Stretch-Blow Molding
Here’s a quick guide to fixing four nettlesome problems in processing PET bottles.
-
50 Years of Headlines … Almost
I was lucky to get an early look at many of the past half-century’s exciting developments in plastics. Here’s a selection.