PEEK for Monolayer E-Motor Magnet Wire Insulation
Solvay’s KetaSpire KT-857 PEEK extrusion compound eliminates adhesion and sustainability constraints of conventional PEEK or enamel insulation processes.
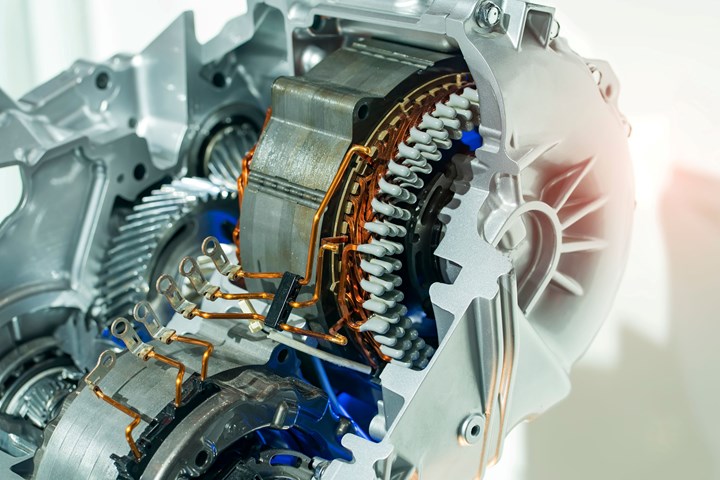
A new PEEK extrusion compound designed especially for copper magnet wire insulation in electric motors has been launched by Solvay. KetaSpire KT-857 is said to eliminate adhesion and sustainability constraints of conventional PEEK or enamel insulation processes. The development of the custom-engineered insulation material was driven by the move of OEMs towards higher density batteries and electric powertrains operating at 800V or above to address the range anxiety of consumers.
In addition to ensuring better adhesion in a faster and more cost-efficient monolayer process, Solvay’s new magnet wire PEEK insulation material also provides important sustainability benefits. The extrusion of a single insulation layer requires less energy, and in contrast to the enamel process there is no need for utilizing any volatile organic compounds. At the same time, KetaSpire KT-857 PEEK reportedly results in a more uniform insulation layer.
Said Brian Baleno, Solvay’s head of marketing for automotive, “Higher voltage e-motors typically require thicker magnet insulation up to 180 microns. In contrast to applying the insulation with a single PEEK extrusion layer, the polyimide process involves multiple application passes, which can potentially introduce defects that tend to magnify as the layers are added. On the other hand, one of the biggest challenges of standard PEEK extrusion is to obtain an adequate level of adhesion of the insulation to the copper magnet wire. Our KetaSpire PEEK KT-857 technology eliminates both of these constraints.”
KetaSpire KT-857 compliments Solvay’s portfolio of dedicated high-performance solutions for e-mobility which also include Aiedium PEEK film and Xydar LCP for slot liners, Amodel PPA and Ryton PPS resins for high-voltage connectors, connection rings and busbars, and Xencor long fiber thermoplastics for slot wedges.
Related Content
-
Prices for All Volume Resins Head Down at End of 2023
Flat-to-downward trajectory for at least this month.
-
Prices of Volume Resins Drop
Price relief is expected to continue through the fourth quarter for nine major commodity and engineering resins, driven by widespread supply/demand imbalances.
-
Resins & Additives for Sustainability in Vehicles, Electronics, Packaging & Medical
Material suppliers have been stepping up with resins and additives for the ‘circular economy,’ ranging from mechanically or chemically recycled to biobased content.