The widespread use of hot-runner systems has resulted in significant benefits for injection molders, allowing for more efficient part manufacturing due to better machine optimization and reduced material waste. Molders can further increase the efficiency of their hot-runner operations if a strategic approach is developed to address the need for resin and color changes that may be required. Following a planned purging procedure will result in shorter material changeover times, can reduce material waste, and over time can reduce the need for reactive maintenance on the entire molding system.
Commercial purging compounds (CPCs) have proven to be most effective at removing color and contamination from hot runners, but it is critically important that the correct purging product is selected and correct procedure is followed for the desired outcome. There are a wide range of CPCs available that can address several variables, including the base resin to be purged, additives, color or modifiers being used, and the temperature and injection capabilities of the machine to be purged. Some CPCs have fillers that may not melt completely during the purging process, which can result in blockages in smaller gates or melt channels or can potentially damage hot-runner components.
Raising nozzle temperature while purging may help remove buildup of material to be purged (a) when the manifold extension nozzle does not match the machine nozzle tip (b).
Chemically active CPCs can be an excellent choice for fast color changes but may not be aggressive enough to thoroughly purge highly contaminated injection systems or highly filled resins. In such cases a purge formulation with a higher viscosity may be required to successfully dislodge a highly filled resin. Additionally, purging a hot-runner system requires consideration of the size of the manifold, gates, and melt channels. There is no “one-size-fits-all” purging compound; a CPC supplier is your best resource to help identify the correct purging formulation and procedure for your needs.
There is no “one-size-fits-all” purging compound.
Two-Step Procedure
In some cases, an injection molder may require a purge cycle to address molding problems resulting from degraded resin in the screw and barrel, or other contamination issues. In these cases, is important to think of the purging process as a two-step procedure where the injection system is purged first, then the hot-runner system. This decoupled approach can help avoid the unintended introduction of contaminants into the hot runner, a situation where purging may not be sufficient to fully clear any undesired material from the melt path. Avoiding this is critical to ensuring a return to production as quickly as possible.
A typical hot-runner purging process may consist of some or all the following steps, though several variables may require more or less time to successfully complete a purging cycle. Again, molders should consider that in all cases it is advisable to first purge the injection system to clear out any contaminants in the screw, barrel, and nozzle, in order to avoid transferring them to the hot-runner system. Once the injection unit has been fully purged, the entire molding system, including the hot-runner, can be purged to complete the material change. In all cases it is critical that the instructions provided by the commercial purging compound supplier are followed carefully.
In general, these steps should be taken:
1. The molding machine’s material-handling equipment should be cleaned of all resins or additives.
2. The cooling system should be turned off on the injection side of the mold, taking care to monitor the mold to avoid overheating.
3. Setpoint temperatures for the manifold, nozzles and hot-runner system should be increased, with caution being taken to not exceed the resin’s maximum temperature specifications.
4. Commercial purging compound is then introduced to the material-handling system, following the supplier’s instructions for purging a hot-runner system.
At this point the hopper or material-handling equipment can be cleaned of CPC and the post-purging phase can begin. Using only screw rotation and backpressure, run the new material through the barrel and hot-runner system for a minimum of 60 sec, or begin running full molding system shots. Once a clean flow of new material is visible at the gates, or several injection cycles have been completed, proceed as follows:
1. Set the machine and hot-runner parameters back to the desired molding conditions. Follow the supplier’s instructions, if required.
2. Run the new material through the entire molding system, including the hot runner for 60 sec, or cycle multiple shots until material looks clean.
3. Begin molding, and inspect parts until the material change is verified and all quality-control requirements are met.
A significant consideration when purging a hot-runner system is the design of the mold itself. Since polymer flow in a hot-runner system is laminar, the time to complete a purge cycle is dependent on the number of drops, melt flow and shear rate. In general, faster purge times and fewer purge cycles can be expected for hot-runner systems that have smaller flow diameters.
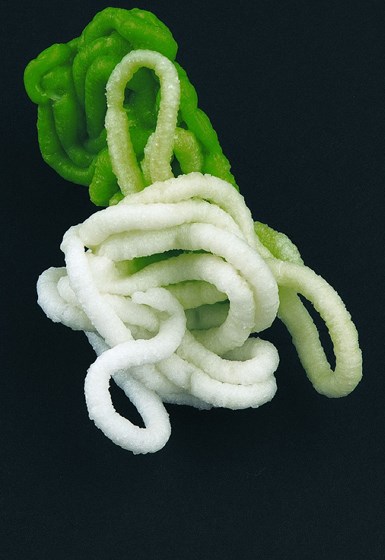
Closely following the instructions provided by your commercial purging compound supplier will help you speed up the purging process while improving your bottom line.
Keep in mind that hot-runner systems are optimized for the intended resin type to be molded, and not for commercial purging compound formulations. The hot runner and the entire molding system will react differently as the system material flow changes from resin, to CPC, and back to resin again.
Again, the preceeding steps are provided as a general guide to the procedures that may be needed to successfully purge an injection molding machine utilizing a hot-runner system. Many variables can affect the time and steps needed to conduct a purge cycle, including the material to be purged, machine operating temperature, age, and condition of the molding system, shot size, screw and barrel dimensions, and the specific characteristics of the hot-runner system.
Faster purge times and fewer purge cycles can be expected for hot-runner systems that have smaller flow diameters.
Any purging regimen will likely need to be adjusted for one or more of these variables. Carefully following the instructions from the CPC supplier will help you complete a purge cycle using the minimum amount of material while reducing downtime.
Molders that implement a consistent purging regimen, including operator training and performance measurement, can expect to achieve significant improvements in their manufacturing performance. Consistently following proper purging procedure and using the correct purge formulation for the application can result in significant cost savings in the form of reduced changeover times and less scrap or wasted resin. Your CPC and hot-runner supplier can be valuable partners in helping you establish a purging strategy and training your workforce on how to purge your hot-runner molding systems most efficiently.
ABOUT THE AUTHORS: Jim Bott is new-business-development manager for automotive at Incoe Corp., and has more than 36 years of experience in hot-runner sales. Contact: 248-616-0220; jim.bott@incoe.com. incoe.com.
Robert Grzegorek is global technical services manager for the Dyna-Purge div. of Shuman Plastics, and has more than 30 years of molding and plant operations experience. Contact: 317-600-9861; rgrzegorek@dynapurge.com; shuman-plastics.com.
Related Content
Best Methods of Molding Undercuts
Producing plastics parts with undercuts presents distinct challenges for molders.
Read MoreHot Runners: A View from the Bottom Up
Addressing hot-runner benefits, improvements, and everyday issues from the perspective of decades of experience with probably every brand on the market. Part 1 of 2.
Read MoreWhy Shoulder Bolts Are Too Important to Ignore (Part 1)
These humble but essential fasteners used in injection molds are known by various names and used for a number of purposes.
Read MoreBack to Basics on Mold Venting (Part 2: Shape, Dimensions, Details)
Here’s how to get the most out of your stationary mold vents.
Read MoreRead Next
Tips and Techniques: Break the Taboo On Purging Hot Runners!
It’s safe to say that the concept of using a commercial purging compound (CPC) has largely been embraced by the plastics processing community.
Read MoreAdd Some Science To Your Purging Practices
Applying scientific methodology to purging techniques is safer and more beneficial than operating ‘on-the-fly’ or using home-made remedies.
Read MoreFollow These Purging and Preventive Maintenance Tips for Your Screws and Barrels
Processors can extend the life of equipment and improve productivity by coupling a preventive-maintenance program for their screws and barrels with routine use of chemical purging compounds..
Read More