Evolving Opportunities for Ambitious Plastics Recycler
St. Joseph Plastics grew from a simple grinding operation and now pursues growing markets in recycled PP, food-grade recycled materials, and customized post-industrial and post-consumer compounds.
Consumer goods brands have set ambitious targets for incorporating recycled plastics into their products, in response to consumer preferences and regulatory mandates. If the targets are to be met in the near future, the industry will rely upon mechanical recyclers to reprocess a range of materials reclaimed from various points in the value chain into a variety of resin grades and compositions for a multitude of applications. An example is St. Joseph Plastics of St. Joseph, Mo., which has been building up this proficiency since the 1980s.
St. Joseph Plastics was founded in 1987 by Jerry Thacker, an injection molding machine operator who found a market for plastic scrap that was being discarded by his employer. By 1990, the business had moved from a garage to a 5-acre facility and grown to include two grinders and five full-time employee. Despite the success of the young venture, Thacker decided to sell. The new owners took over a business with an expanding customer base but plenty of space for growth, both literally and in terms of sophistication.
“We really wanted to make the processes better, hire good people, and differentiate through quality,” says Rob Starr, St. Joseph’s current owner and president. “At the time we were maybe a ’C’ level supplier, and our goal was to work our way up to ‘A’. We want to be our customers’ and suppliers’ Number 1, so that when market conditions are tough and the other guys are being knocked out, we’re the ones to supply that last piece of business.”

L-R: Leighton DeGarmo, Rob Starr, Dave Walker, and Ron Moore of St. Joseph Plastics, amidst the company’s eight-line grinding operation. (Photos: Matt Stonecash)
With a focus on building relationships and producing quality regrind, St. Joseph Plastics continued to expand throughout the 1990s and 2000s, engaging new customers and finding new sources of scrap .
Fundamentally, the focus of the business remained the same: buying, grinding and selling. Then, in 2009, the company decided to expand its offerings to include pellets and purchased its first extruder. From 2010 to 2012, further investments in a lab and additional extruders prepared St. Joseph Plastics for entry into the compounding business. “You really can’t do anything until you have a good lab, and it took some time to build that up. We then became a compounder and started to offer more resins to more customers, “ says Starr.
Recycled Materials Lost a Major Outlet
Around that same time, material recovery facilities (MRFs) had started to collect and provide the first bales of post-consumer PP. St. Joseph began tests with the material and soon developed and successfully marketed pellets of that versatile resin. For years, however, many MRFs did not collect PP or did not separate resin codes 3 to 7 (that is, a mix of plastic waste from which PET and HDPE have been removed). Around 2018 to 2020 the economics began to change.
China launched Operation National Sword in 2017, a program that implemented much more stringent review of that country’s imports of plastic waste. Abruptly, the global market for reclaimed plastic lost its number-one buyer. The West suddenly found itself without a market for low-value material it was producing in large quantities.
China’s new waste import restrictions affected prices across all reclaimed plastics, but particularly unsorted and contaminated mixed plastic bales. In the aftermath, more MRFs are looking to increase value by separating out higher-value products from their mixed-plastic bales, including PP.
PP bales from recovery facilities are one important feedstock for recycling operations at St. Joseph Plastics. As more MRFs add PP to their accepted items, and modernize to improve their sorting capability, availability and quality of these bales is likely to improve.
While post-consumer recycling is an important and growing part of St. Joseph Plastics’ business, the majority of the material it processes is post-industrial PP and PE from molding operations.
“It’s just as important as post-consumer,” says Starr. “Most molders have a scrap rate around 3-5%, and that doesn’t include obsoletes. There’s a lot of post-industrial material out there, and it all needs to be recycled.”
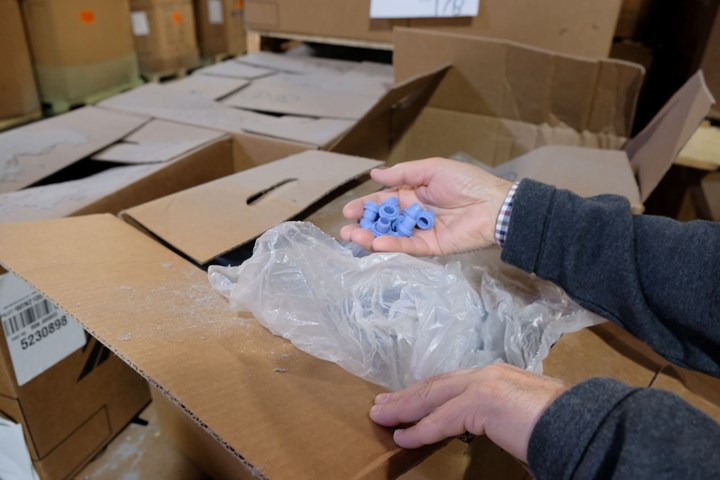
Injection molding scrap is a significant source of feedstock for St. Joseph Plastics.
Integrated Plastic Recycling
Today, St. Joseph Plastics is a sophisticated, full-service recycler with over 100 employees. Operations have expanded to three processing facilities, two in St. Joseph itself and one in the city of Sedalia, Mo., two hours to the east. Sedalia is the starting point for bales of post-consumer material. Bales are broken, material is fed through a trommel to remove contamination, then washed, aspirated, sorted, and dried before transport to St. Joseph for further processing.
“Most molders have a scrap rate around 3-5%. There’s a lot of post-industrial material out there, and it all needs to be recycled.”
The grinding operation now boasts eight lines and has moved to the company’s Easton Road facility, just a few miles from the original location. These lines are primarily fed scrap material purchased or tolled from a wide variety of injection molding operations. These come in all shapes, sizes and colors, ranging from purgings or simple parts to completed assemblies, which may require removal of contaminating materials such as metal. Molding rejects and other scrap are shredded and ground, then shipped to customers or passed to the compounding facility for further processing.
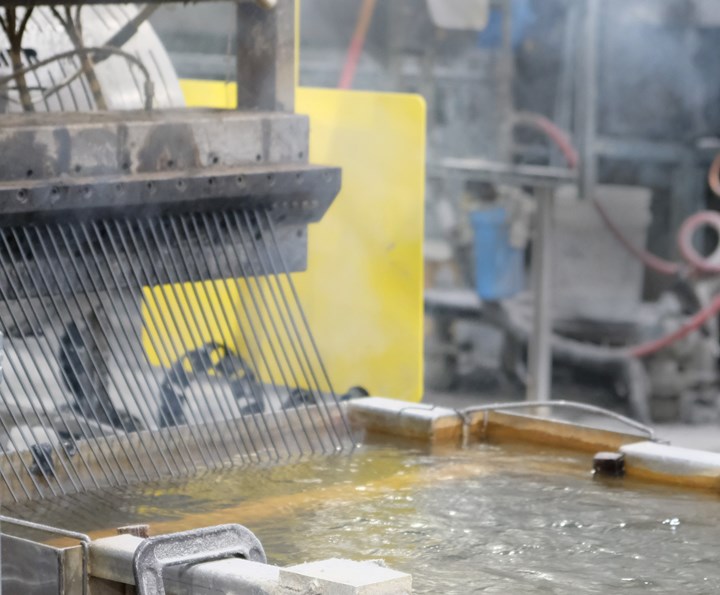
St. Joseph has built a thriving business in compounded and pelletized recyclate.
The original St. Joseph Plastics site now houses testing, compounding, sorting, and blending operations. Six extrusion lines melt, purify, and pelletize granules and other feed materials.
Silos with integrated blending provide homogeneity in addition to stabilization. “It’s really essential to have good blending capability,” says Starr. “Our goal is that the whole truckload be uniform, so when the molder gets the product, they set their machines once and run for 42,000 lb.”
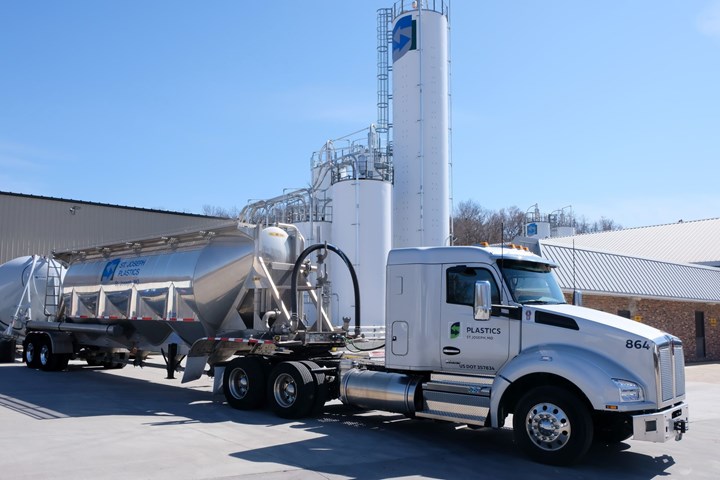
Storage and delivery systems are important to a recycler focused on supplying homogenous resin.
Material Testing Is Crucial
At any moment, post-consumer and post-industrial waste from a variety of suppliers is making its way through this manifold of processes, on its way to becoming a variety of blends bound for St. Joseph’s customers. Material traceability could not be more critical. “The challenge is getting consistency in our resins,” says Starr. “Each supplier may use several different resins themselves, so we have hundreds of different grades coming in here, and we have to figure out how that affects our end product”.
The analysis lab is critical to establishing and tracking the key characteristics of the recycled materials so that each lot can be managed and tracked, always with an eye to the needs of the customer for that product.
“Brand names are coming to the molders and saying, ‘You need to get recycled resin into our products, so we can have that benefit when we market them’.”
Materials are tested when received, throughout processing, and before shipping. The lab includes instruments for measuring melt-flow index, Izod and Gardner impact resistance, ash content, flexural and tensile properties, and more. The lab also has a small extruder for trials and other needs as they arise. The data builds St. Joseph’s knowledge of the interaction between processing steps and feedstock material properties, which guides production adjustments and blending.
The objective is to provide the customer, who may be reluctant to try out a recycled resin, with a product they can drop right into their process with minimal adjustment.
This is especially important for molders who may be new to recycled resins. Sometimes, spec agreements with manufacturers may be an obstacle. These agreements are meant to ensure consistent quality, but can end up restricting the resins a molder can use.
“We suggest people to talk to their customers about opening that up,” says Ron Moore, product v.p. at St. Joseph Plastics. “Now it’s starting to work the other way: Brand names are coming to the molders and saying, ‘You need to get recycled resin into our products, so we can have that benefit when we market them’.”
St. Joseph Plastics offers a variety of off-the-shelf resins for downstream processors, both in flake and pellet form. Offerings include 13 GreenCircle Certified resins. GreenCircle is a third-party certifier of post-consumer recycled resins, endorsed by the Association of Plastics Recyclers.
Knowledge of material properties and how they are changed by their processing steps has allowed St. Joseph not only to create a variety of blends for the market, but also to customize product for individual customers.
“Sometimes a customer may call us and say they need a certain resin specification, and we will design and produce a custom resin for them,” says Leighton DeGarmo, business development manager.
Future Directions in Recycled Resins
Converters can expect to see the expansion of St. Joseph’s product portfolio continue, as the company seeks to leverage its expertise in material management, compounding, and blending to offer higher value, more complex resins.
Recently, St. Joseph Plastics received a “letter of no objection” from the FDA, concerning the use of post-consumer PP for food-grade applications. This means the company has demonstrated it has the correct quality controls in place to begin selling recycled plastic for use in food packaging, a high-value and desirable market for plastic recyclers and packaging converters.
“We are getting more and more into the development of resins.” says Starr. “We have experience with a lot of different materials, and we know what it takes. That has given us the confidence to get into more complex formulations.”
Related Content
Reversing Logistics for Plastic Film Recycling
Learn how Mainetti built a circular supply chain for clear film packaging.
Read MoreCompatibilizers Aid Recycling & Upcycling of Mixed Resins
Compatibilizers are proving their worth in boosting critical properties such as impact/stiffness balance of PCR and PIR blends of polyolefins and other plastics.
Read MoreScaling Up Sustainable Solutions for Fiber Reinforced Composite Materials
Oak Ridge National Laboratory's Sustainable Manufacturing Technologies Group helps industrial partners tackle the sustainability challenges presented by fiber-reinforced composite materials.
Read MoreA Recycling Plant, Renewed
Reinvention is essential at Capital Polymers, a toll recycler that has completely transformed its operation in a short period of time.
Read MoreRead Next
Why (and What) You Need to Dry
Other than polyolefins, almost every other polymer exhibits some level of polarity and therefore can absorb a certain amount of moisture from the atmosphere. Here’s a look at some of these materials, and what needs to be done to dry them.
Read MoreProcessor Turns to AI to Help Keep Machines Humming
At captive processor McConkey, a new generation of artificial intelligence models, highlighted by ChatGPT, is helping it wade through the shortage of skilled labor and keep its production lines churning out good parts.
Read MoreAdvanced Recycling: Beyond Pyrolysis
Consumer-product brand owners increasingly see advanced chemical recycling as a necessary complement to mechanical recycling if they are to meet ambitious goals for a circular economy in the next decade. Dozens of technology providers are developing new technologies to overcome the limitations of existing pyrolysis methods and to commercialize various alternative approaches to chemical recycling of plastics.
Read More