Injection Molder Changes Up Color Changes
An injection molder of trash cans, pallets, totes and other plus-size components, Rehrig Pacific’s machine fleet is composed of larger tonnage presses whose size makes material changes at the feed throat a potentially dizzying exercise.
Reid Devitt, presently the national purchasing specialist at Rehrig Pacific Co. in Los Angeles, was a plant engineer at the company’s Atlanta operation when he reached out to material blender and loader supplier Plastrac seeking a better means to change color on the company’s “cart” molding machines. The carts in question are roll-out trashcans that range up to 95 gal, and Devitt was specifically concerned with the carts being molded on a 3200-ton injection press with a feed throat 15 ft off the ground.
Rehrig’s Pacific’s injection molded carts range in size up to 95 gal and come in a variety of colors.
Photos: Rehrig Pacific
“We dabble in a lot of different industries,” Devitt says, “but most of our machines are really big. We’re not making tiny plastic parts.” For the company’s select few smaller injection molding machines, Rehrig had successfully utilized Plastrac’s smaller feeding and dosing units. Devitt reached out to Plastrac’s Eric Bullivant in the hopes that the success experienced on the smaller applications could be scaled up.
“One of the big concerns we had was that the original units were throat-mounted, so we’d have to have someone go up into the mezzanine next to our machines, which is pretty high up, and do our color change way off the ground,” Devitt says. “Rehrig is a safety-first company, and we thought, ‘Is there anyway of getting around this?’”
The potential solution from Bullivant was Plastrac’s newly patented ColorStream system, which moves blending from atop the machine to beside the press in a unit located on the floor, feeding colors and additives from there to the machine throat to blend with the main resin being flood-fed from a central loading system. Rehrig would be one of two companies pilot testing the new ColorStream technology.
In addition to the enhanced safety aspect, the Atlanta facility was able to use the ColorStream to reduce the number of shots between color changes from 20 to just six to eight, and increase the amount of regrind it coinjected into each cart . Two factors were key to those gains. First, in the prior setup, the blenders were located roughly 300 yards from the molding machines in a separate room. Over that distance, a once homogenous mix could separate out by the time it reached the machine.
“Rehrig is a safety-first company, and we thought, ‘Is there anyway of getting around this?’”
“Blending is inconsistent once it has to travel that distance,” Devitt says, leading to issues with how much regrind the company could utilize. “We saw that the blend with the ColorStream covered the coinjected recycled material much better than our older blenders. The problems we had with streaking on some of our problem colors just went away.”
In the prior setup, Rehrig had to pause the blenders out of sight of the molding machine before attempting a color change. If they failed to, the company had a hopper-full of scrap. “Color changes were more seamless because we weren’t having to pause a blender in a different room,” Devitt says. “If we missed a blender pause with ColorStream, we didn’t have to dump out a bunch of material and reuse it as regrind when it’s perfectly good material that’s been colored with the wrong additive.” Given the size of the hoppers, that good material/wrong additive batch could weigh up to 150 lb. ColorStream utilizes continuous blending with a very small inventory inside the blending chamber.
Rehrig normally performs anywhere from three to eight color changes a day, running them in a “wheel” progressing from lightest to darkest color. “We were able to make a dark-blue to lighter-brown color change happen between six and eight shots,” Devitt says. “That exact color change could take up to 20 shots before.”
Two years after first reaching out, Devitt is in a new position and ColorStream units are fully integrated into Rehrig’s operations after being added in Wisconsin, Pennsylvania and Florida. “We’ve made this a national initiative for our cart molding machines,” Devitt says. “Everyone’s more standardized now on how they’re doing changeover, versus what we were doing in the past.”
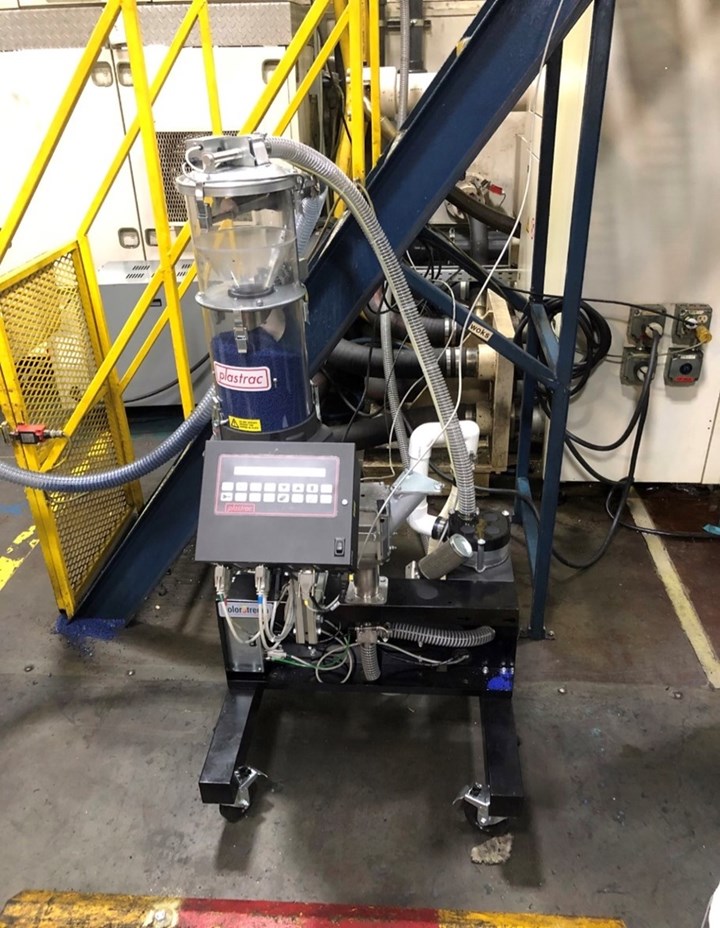
Plastrac’s ColorStream allowed Rehrig to move color changes to beside the press, keeping workers from making changes above the machine.
Related Content
DSM Launches an AI Powered Color & Mechanical Properties Prediction Tool
Called Lucidiris, this prediction tool can reduce time to market when developing colors of high-performance materials for a variety of applications.
Read More'Dual Action' Purging Compound Accelerates Color Changes
Shuman Plastics’ Dyna-Purge Division launches Dyna-Purge L, extending its “3X technology.”
Read MoreHow to Start a Hot-Runner Mold That Has No Tip Insulators
Here's a method to assist with efficient dark-to-light color changes on hot-runner systems that are hot-tipped.
Read MoreUnderstanding the ‘Science’ of Color
And as with all sciences, there are fundamentals that must be considered to do color right. Here’s a helpful start.
Read MoreRead Next
Understanding the ‘Science’ of Color
And as with all sciences, there are fundamentals that must be considered to do color right. Here’s a helpful start.
Read MoreCart-Mounted Blending Systems Updated
Updates to Plastrac's cart-mounted blended systems which debuted at NPE2015 include a new touch-screen control.
Read MorePlastrac Promotes Flexibility With Upgraded Cart Blending
Building off a concept launched at last NPE, Plastrac has a revamped version of its cart-based blending system in Orlando that stresses flexibility.
Read More