Tracing the History of Polymeric Materials, Part 25: Silicones
The long road to the development of silicone resulted in a chemistry that is remarkably versatile.
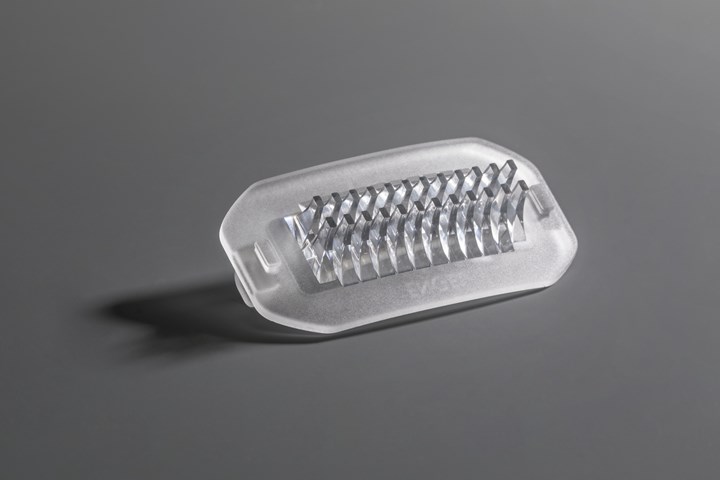
High clarity and heat resistance, plus easy moldability, have made silicones (LSR in this case) attractive in lens applications. (Photo: Engel)
After the 1938 meeting between General Electric and Corning Glass Works discussed in last month’s column, two parallel paths developed that led to the creation of commercial silicones. At Corning, J. Franklin Hyde continued his work using the Grignard reaction approach. By 1942, his work had reached a point where additional resources were needed to support the research. Corning entered into a joint venture with Dow Chemical early in 1943 and the Dow Corning plant was established in Midland, Mich., near the Dow Chemical plant. Those familiar with organic chemistry know that the Grignard reagent utilizes magnesium, and Dow Chemical was the sole domestic producer of magnesium at that time.
But in the meantime, Dr. Eugene Rochow at GE had begun experimenting with silicones and investigated a practical approach to producing the methyl silicones that constitute the basis for modern silicone chemistry, shown in the accompanying figure. In May of 1940, Rochow invented a method for direct synthesis of methyl chlorosilanes by reacting methyl chloride with elemental silicon using copper as a catalyst. This bypassed the dependence on the Grignard process, effectively breaking Dow’s monopoly and opening the door to GE’s entry into the commercial silicone business. This happened officially in November of 1944.
In Germany, Dr. Siegfried Nitzsche published a report in 1947 on silicon-containing plastics, which formed the basis for the entry of Wacker into the industry in 1949. Bayer entered the market in 1952 and later formed a joint venture with GE. Early development began at the same time in China, which is now the world’s largest producer and consumer of organosilicon compounds. In Japan, Shin-Etsu Chemical Co. began making silicones in 1953. The manufacturing landscape has evolved over time, and today GE is not in the silicone business (which was sold to Momentive), and the Dow Corning joint venture was dissolved when Dow took over the silicones business.

The long road to development created a chemistry that was remarkably versatile. The first commercial silicone product introduced at Dow Corning was called DC 4 Compound. It was used successfully to coat the Allied aircraft ignition wire harnesses during World War II to prevent arcing at high altitudes. In 1949, GE engineer James Wright mixed silicone oil with boric acid to form the product that has become known as Silly Putty, every polymer scientist’s favorite material for demonstrating the property of viscoelasticity. In 1950, a silicone product was developed to treat leather. In 1969, Neil Armstrong stepped onto the lunar surface wearing boots with soles made from silicone. In 1970, adhesive tape made from a silicone base was used to produce what became known as the “Post It” note.
Silicones do not require the use of plasticizers to achieve their balance of properties.
At the same time, liquid silicone rubber (LSR) was being developed. Fifty years later, this class of materials continues to undergo innovation with lower-temperature curing systems. By the early 1980s silicones were being adopted as protection for microprocessor components from damage due to overheating. Contact lenses produced from silicones were developed in the early 1990s. Today, silicone chemistry is found in food and cosmetics, tubing and hoses, gaskets, sealants and caulks, lubricants and greases, coatings for textiles and paper, electronic keypads, potting compounds, cookware and elastomeric components. Silicone polymers can be incorporated into other polymers to improve flame resistance, environmental stress-crack resistance (ESCR), impact performance and UV stability.
The ability of silicone to fulfill a wide range of requirements comes from its unusual chemistry. The siloxane (Si-O) bond is quite non-reactive and at the same time is over 20% stronger than the C-O bond, making the resulting polymer backbone resistant to chain scission. Consider that silicone polymers can perform at temperatures as high as 250-300°C (482-572°F) and are inherently flame retardant. The analogous carbon-based polymer is POM, which degrades at temperatures above 220-230°C (428-446°F) and burns rapidly.
While the siloxane bond strength is very high, the combination of the bond angle and its length, coupled with the mobility of the pendant groups (usually methyl groups), provide for a high degree of molecular mobility that results in a very low glass-transition temperature and therefore good flexibility even at extremely low temperatures. This also contributes to relatively low viscosities that change little with temperature. This high degree of mobility also results in very low surface energies, lower than everything except fluoropolymers.
The ability of silicone to fulfill a wide range of requirements comes from its unusual chemistry.
Despite the fact that the Si-O bond is quite polar, silicones tend to be non-polar due to shielding from the side groups, which are usually hydrocarbons like methyl groups or phenyl rings. This allows silicone coatings to be water repellent. Polarity can be introduced by plasma treatment or by incorporating amine or alkoxy groups in place of the methyl groups. This can allow a material that is normally considered to be a lubricating agent to act as an adhesive. The well-known relationship between viscosity and molecular weight accounts for the variety of forms that silicone can take, with the high-molecular-weight end of the spectrum accounting for polymeric silicone, mostly in the form of silicone rubber. The linear polymer takes the form of a high-viscosity gum.
Crosslinking by vulcanization provides for the performance that is familiar to users of these materials. Various catalysts are available for promoting crosslinking, including tin catalysts used in room-temperature vulcanizing (RTV) systems, peroxides, and platinum-based systems that provide for rapid crosslinking. The curing process provided by platinum-based systems can be inhibited by contact with some plastics and metals, and the catalysts can be poisoned by substances that contain sulfur, phosphorus, or amines. Properties are tailored by varying molecular weight, degree of crosslinking, and the chemistry of the organic pendant groups. Optimal performance typically requires a post-cure routine and most data sheets for silicone polymers indicate that the published properties assume such a post-cure process that consists of 2-4 hr at 175-200°C (347-392°F).
Silicones do not require the use of plasticizers to achieve their balance of properties. This makes them attractive for applications where biocompatibility is required. It is also a benefit in situations where the elastomer will be in direct contact with rigid thermoplastics such as polycarbonate that can be susceptible to stress cracking. In addition to superior thermal stability at very high temperatures and flexibility at very low temperatures, silicones have excellent electrical properties and are resistant to ozone and ultraviolet radiation.
Because of the high degree of molecular mobility in the polymer backbone, the mechanical properties of silicones tend to be relatively poor compared with carbon-based rubber compounds. Fillers can be used to compensate for the mechanical shortcomings. These include silica, carbon black, and boron nitride. Tear strength, in particular, is relatively low; and while high-tear-strength grades are available, these materials typically succeed in just matching typical tear strengths for other rubber compounds. Silicones are also more permeable to gases than most of the carbon-based elastomers.
In addition, silicone rubber tends to have poor resistance to oils and solvents. They swell in a variety of solvents, including chloroform, tetrahydrofuran and hexane. While they are more resistant to polar solvents, they have poor resistance to hot water, steam and concentrated acids, although fluorinated compounds can provide improved performance in this area. Finally, silicones tend to be more costly than many carbon-based elastomers. Despite these shortcomings, silicones have a long history of fulfilling requirements that could not have been met by any other chemistry.
Innovations in cure chemistry continue, and a special class of materials known as silsesquioxanes remain largely uninvestigated and may have application in improving the processability of other polymers. A pilot program in adding small amounts of these materials to polyphenylene oxide (PPO) showed that the material could be molded in pure form without the addition of HIPS, thus realizing the original promise of the PPO polymer. But more work is needed to confirm the viability of this approach.
ABOUT THE AUTHOR: Michael Sepe is an independent materials and processing consultant based in Sedona, Ariz., with clients throughout North America, Europe, and Asia. He has more than 45 years of experience in the plastics industry and assists clients with material selection, designing for manufacturability, process optimization, troubleshooting and failure analysis. Contact: (928) 203-0408 • mike@thematerialanalyst.com
Related Content
Biobased TPU for Broad Range of Applications
BASF’s Elastollan N contains 50% renewable raw material.
Read MoreAdvanced Plastomers for Production of PE-Based Sealant Resins
Nova Chemicals’ new Astute products are suitable for a broad range of applications including food packaging, heavy-duty sacks and e-commerce.
Read MoreGEON Performance Solutions Buys PolymaxTPE
Combined company aims to be global leader in thermoplastic elastomers.
Read MoreKraiburg TPE Expands Range of TPEs with ISCC PLUS Certification
The expanded range supports customers in the consumer and medical sectors in next steps toward a circular economy.
Read MoreRead Next
Tracing the History of Polymeric Materials: Polyphenylene Oxide
Behind the scenes of the discovery of PPO.
Read MoreTracing the History of Polymeric Materials: Silicones
More properly known as siloxanes, silicones are a class of materials where no carbon is present in the polymer backbone.
Read MoreTracing the History of Polymeric Materials: Polyphenylene Oxide Blends
PPO was a promising new high-performance thermoplastic, but it could be made useful only by mixing it with a humble commodity resin.
Read More