Unraveling the Science and Myth Associated With Moisture Analysis— Part 1
The first task in moisture measurement is to purchase an instrument that is based on sound fundamentals. Then, before it goes into use, method development must be undertaken for all polymers that are going to be processed in the plant.
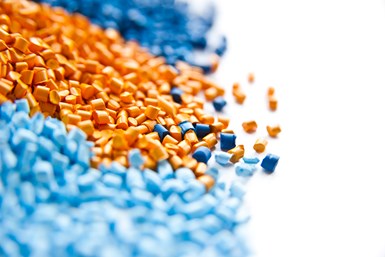
We have discussed the topic of moisture measurement in polymers a number of times over the years. But the subject keeps coming up, so it would seem appropriate to revisit the science and myth associated with this endeavor.
First, as we have pointed out a number of times, most processors who believe they are measuring moisture content are actually measuring volatiles, some combination of moisture, residuals and additives that are extracted when any plastic material is exposed to elevated temperatures. The weight loss that occurs when the sample is heated to some prescribed elevated temperature is interpreted as the moisture content.
This method is known as loss on drying. It is a technique that can work for materials where the target moisture contents are high (1-10%) and the amount of other volatile compounds that can interfere with the measurement constitutes a small percentage of the moisture that is present. Substances like foods, pharmaceuticals and hydrated minerals are good examples. However, this technique is fundamentally unsuitable for polymers where the target moisture contents are very low (0.02-0.10%) and the amount of other volatile compounds that can be driven off during the test represents 10-100 times the amount of moisture that is present. For these types of materials, a sensor-based instrument must be used.
Four Options for Measuring Moisture
So, what works? There are several options. The method that has the longest history, developed in the 1930s, is Karl-Fischer titration. This technique uses a mixture of liquid reagents. The electrical conductivity of this mixture is influenced by the introduction of water and this enables the change in this conductivity to be converted into the amount of introduced moisture. The equivalence is governed by Coulomb’s law.
An alternative method that uses a chemical approach involves a reaction between water and calcium hydride. This reaction produces hydrogen gas; one molecule of hydrogen is created for each molecule of water introduced. Boyle’s law governs the relationship between the volume of the hydrogen and its mass, enabling a direct calculation of the water that generated the hydrogen. While Karl-Fischer uses a mixture of liquid compounds, calcium hydride is a solid and therefore offers greater ease of use.
Another instrument, which employs a relative humidity sensor, is known commercially as the Vapor Pro XL from Brookfield Ametek. This device has been correlated through a number of studies with Karl-Fischer titration and has been improved over a period of time so that it now provides a reliable alternative to the chemical techniques. No chemicals are involved and the only consumable is a septum that seals the vial in which the sample being tested is contained. This septum typically can be used three to five times before it needs to be replaced. While this device is a sensor-based instrument, operationally it looks a lot like the loss-in-weight devices. The big difference is that because of the sensor it has the ability to distinguish between moisture and all the other volatiles that inevitably evolve from the sample when it is heated.
Finally, the fourth alternative is an instrument that capitalizes on an established relationship between the moisture content of polymers and their dielectric properties. Benchtop instruments that rely on this relationship were developed in the early 1980s, but the commercialization of this technique languished for many years. It was incorporated into an in-line measuring device that was introduced by Novatec at NPE2012.
All four of these techniques are embodied in instruments that are more costly than the loss-in-weight systems that are predominantly in use in manufacturing environments and they involve different learning curves. The Vapor Pro XL is the least challenging instrument to learn, while the Karl-Fischer titrator is the most demanding. In 1986, when the manufacturing facility I worked at first started molding PET, the requirement for measuring moisture content prior to starting up a mold could only be fulfilled by Karl-Fischer titration; the other three alternatives did not exist at that time. The general view of the Karl-Fischer approach was that it was too difficult for the production personnel in the molding facility. The glassware and the chemicals, so the narrative goes, would intimidate the staff to the point where they would be unable to use the equipment.
However, over the period of several months, we trained several people on all three shifts to effectively run tests using the Karl-Fischer titrator and it became an essential piece of equipment from that point forward. It was still operating around the clock when I left the company 20 years later. When we opened a plant in Mississippi in the 1990s, we installed the same device at that location and it was adopted there as well. While this demonstrates the feasibility of using this device in a production setting, it is true that the other techniques that have been developed to fulfill the role of accurately measuring moisture are simpler to learn.
The goal of moisture measurement involves efficient and complete removal of all the moisture in a sample without degrading the polymer.
But the experience of developing the Karl-Fischer technique for polymers taught us an important lesson. Method development is critical. These devices are not plug and play. We found that the people who build these instruments have great expertise in designing the equipment, but they know very little about polymers. However, the material suppliers, who know their polymers, know very little about these instruments. When we acquired our Karl-Fischer titrator, we were provided with a list of materials and recommended test conditions that came from the instrument manufacturer. Once we began to develop our methods internally, we found that this list was essentially useless.
Fooling the Instrument
We also found that as good as Karl-Fischer titration is, it was possible to fool the instrument. The fundamental goal of moisture measurement involves efficient and complete removal of all the moisture in a sample without degrading the polymer. We quickly discovered that this required that the carrier gas used to sweep the moisture from the sample into the titrator needed to be nitrogen or some inert gas that would prevent oxidation and provide a workable temperature window between the required temperature and the point at which degradation begins.
A good example involves one of the most critical polymers, PET. Heating a sample of PET in air to a temperature that enables rapid and complete extraction of moisture also produces a by-product known as acetaldehyde. One of the chemicals in the Karl Fischer titrator is methanol. It is well known in organic chemistry that aldehydes react with alcohols to produce water. So, evaluating a PET while using air results in a test that runs for a very long time and gives a drastically inflated value, because much of the water that is “measured” is actually produced during the test. Changing over to nitrogen solves this problem.
So, the first task in moisture measurement is to purchase an instrument that is based on sound fundamentals. But this is just the beginning. Once the instrument is taken out of the box and powered up, before it goes into use, method development must be undertaken for all polymers that are going to be processed in the plant. The importance of this will be demonstrated in the next installment on this topic.
ABOUT THE AUTHOR: Michael Sepe is an independent materials and processing consultant based in Sedona, Arizona, with clients throughout North America, Europe and Asia. He has more than 45 years of experience in the plastics industry and assists clients with material selection, designing for manufacturability, process optimization, troubleshooting and failure analysis. Contact: 928-203-0408 • mike@thematerialanalyst.com
Related Content
PBT and PET Polyester: The Difference Crystallinity Makes
To properly understand the differences in performance between PET and PBT we need to compare apples to apples—the semi-crystalline forms of each polymer.
Read MoreAre Your Sprue or Parts Sticking? Here Are Some Solutions
When a sprue or part sticks, the result of trying to unstick it is often more scratches or undercuts, making the problem worse and the fix more costly. Here’s how to set up a proper procedure for this sticky wicket.
Read MoreUnderstanding Strain-Rate Sensitivity In Polymers
Material behavior is fundamentally determined by the equivalence of time and temperature. But that principle tends to be lost on processors and designers. Here’s some guidance.
Read MoreWhy (and What) You Need to Dry
Other than polyolefins, almost every other polymer exhibits some level of polarity and therefore can absorb a certain amount of moisture from the atmosphere. Here’s a look at some of these materials, and what needs to be done to dry them.
Read MoreRead Next
Troubleshooting Screw and Barrel Wear in Extrusion
Extruder screws and barrels will wear over time. If you are seeing a reduction in specific rate and higher discharge temperatures, wear is the likely culprit.
Read MoreProcessor Turns to AI to Help Keep Machines Humming
At captive processor McConkey, a new generation of artificial intelligence models, highlighted by ChatGPT, is helping it wade through the shortage of skilled labor and keep its production lines churning out good parts.
Read MoreLead the Conversation, Change the Conversation
Coverage of single-use plastics can be both misleading and demoralizing. Here are 10 tips for changing the perception of the plastics industry at your company and in your community.
Read More