Adaptive, Automatic Process Control for Injection Molding
Sumitomo (SHI) Demag says its activeMeltControl for all new IntElect 2 machines can automatically compensate for shot-weight variations.
At Fakuma 2023, Sumitomo (SHI) Demag introduced an adaptive process control, dubbed activeMeltControl (aMC), for its IntElect 2 all-electric injection molding machines. Integrated into the machine’s controller, aMC can compensate for shot-weight discrepancies caused by material batch fluctuations; running recycled or regrind materials; and resin variations due to drying differences, dosing deviations or the use of additives.
The company notes that more consistent part weights can lead to a rapid return on investment (ROI) because of better process consistency, longer machine uptime and reduced scrap. Sumitomo (SHI) Demag says molders can also benefit from greater manufacturing flexibility with the ability to run a wider range of materials, including PCR and PIR.
In development for four years, aMC came in response to customer interest and what the company describes as the changing quality of plastics with fewer virgin materials and more recyclable content in the market. The aMC is activated with a single click and runs fully automatically in the background, compensating for viscosity fluctuations and backflow barrier leaks, adjusting the pressure accordingly. Sumitomo (SHI) Demag says molders can tailor the program to their specific process needs and respond to the machine’s characteristics using an adjustment controller. Initially, aMC will be available for all IntElect 2 series fully-electric injection molding machines starting in the first quarter of 2024, with retrofits planned for the future.
Sumitomo (SHI) Demag has also optimized its myAssist software, which provides process transparency for molders by providing insights into process parameters. The company characterized the upgrade as transforming myAssist into a “digital process companion,” with optimized interfaces and improved data collection and visualization. The user interface is now customizable to individual customer preferences, enabling the representation of cycle- and time-based data. Users can create custom dashboards with material or consumption data, or define their own key performance indicators (KPIs).
Sumitomo (SHI) Demag adds that myAssist has improved process stability while reducing data volume for better transmission, offering more data exchange and analysis possibilities, as well as improved connectivity. The myAssist now includes a high-speed knowledge database with I/O interfaces for IoT 4.0. A Human Virtual Interface (HVI) and an expertise module provides options for manual process annotations, with the ability to connect all new IntElect machines.
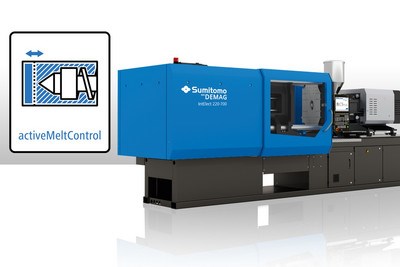
The new aMC will be available for all IntElect 2 series fully-electric injection molding machines starting in the first quarter of 2024, with retrofits planned for the future. Photo Credit: Sumitomo (SHI) Demag
Related Content
-
Slimmer All-Electric Press Debuts
A slimmed-down version of Engel’s all-electric, e-mac injection molding machine is among eight displays, which also include LSR micromolding, quick mold changes and a cube mold.
-
Word Games: What’s a ‘Hybrid’?
Any molder will tell you there’s a difference in working with electric vs. hydraulic drives. Servohydraulic is still hydraulic; a hybrid machine is something different. Imprecise use of terms causes needless confusion.
-
Injection Compression Molding as Alternative to Thermoforming
Arburg will show its all-electric Allrounder 720 A press utilizing injection compression molding to create thin-wall IML cups from PP.