Faster Neck Changes Add Flexibility to Aseptic PET Blow Molding
KHS machines now can change neck sizes and associated components in one-third the former time.
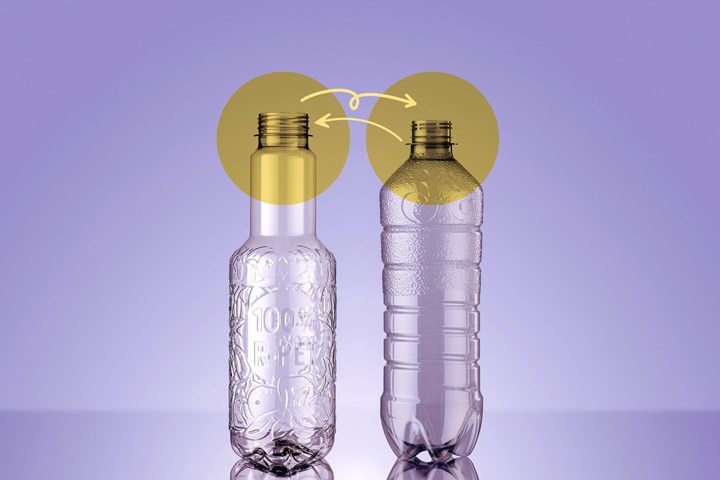
Quick changes of neck sizes allow flexible production of aseptically filled beverages and juice (38 mm) and carbonated soft drinks (28 mm) on the same blowing-filling-capping line. (Photo: Frank Reinhold)
If you wished to stretch-blow mold aseptically filled PET bottles for beverages and juices, which typically require 38-mm bottle necks, on the same line as bottles for carbonated soft drinks with 28-mm necks, you might have faced changeover times involving multiple workers for as long as 4 hr. Until now, that is.
KHS has addressed the need for more flexible production of multiple neck sizes on aseptic PET blowing-filling-capping lines by analyzing the ergonomics of every step of the process and introducing numerous modifications to components of its equipment in an integrated line like the InnoPET BlowFill.
For example, magazines were installed that stop the operator from having to leave the machine repeatedly to fetch change parts. KHS also replaced the grippers to reduce the number of screws to be loosened and tightened. Of particular importance, newly developed mandrel heads can be removed simply by pressing a release spring. With all these and other changes, the time needed for two operators to convert the KHS InnoPET Blowmax 16 stretch-blow molder — which has around 170 mandrel heads and shields to be replaced—has been cut by two-thirds to about 86 min, including the preform infeed.
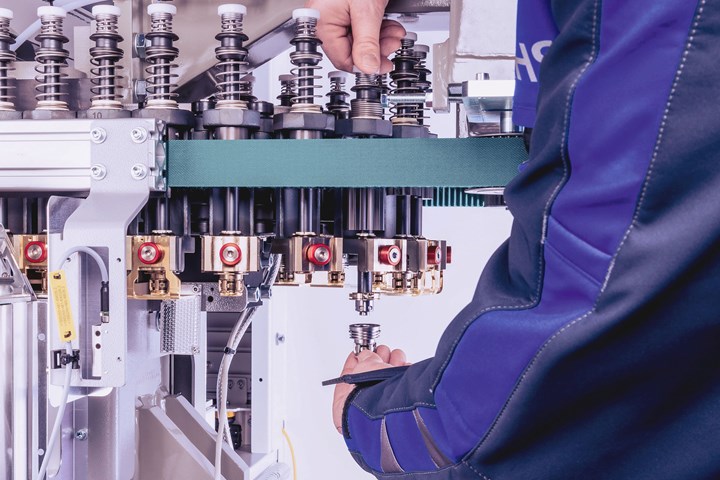
A new feature on KHS InnoPET Blowmax machines is mandrel heads that are released by simply pressing on a spring. (Photo: Jörg Schwalfenberg)
KHS also modified the filler and capper. For example, there are now two cap feeds, one for each neck diameter, so no conversion is required.
KHS says these modifications offer customers “totally new options in their production planning.” For example, they allow molders to produce smaller batches of different bottles on a single line much more efficiently. There are also new advantages for customers that produce just-in-time, loading finished containers straight onto the truck without any interim storage.
Related Content
-
50 Years of Headlines … Almost
I was lucky to get an early look at many of the past half-century’s exciting developments in plastics. Here’s a selection.
-
50 Years...600 Issues...and Still Counting
Matt Naitove marks his first half-century in plastics reporting, with a few of his favorite headlines.
-
Foam-Core Multilayer Blow Molding: How It’s Done
Learn here how to take advantage of new lightweighting and recycle utilization opportunities in consumer packaging, thanks to a collaboration of leaders in microcellular foaming and multilayer head design.