Try This Alternate Method for Heating Your Torque Rheometer
Rheometers are generally not on all the time. And most users have found that the first test run in the instrument after heating up is not very reliable and is usually discarded. Try this method instead.
The torque rheometer is a very valuable tool for examining the fusion characteristics of PVC and many other formulations. Many units are used for QC testing and so are left on around the clock to always be ready for the next test.
But most units are in the lab for evaluating new formulations, alternate raw materials, troubleshooting and formulation testing. Because these are only used as needed, they are only turned on and allowed to heat up when needed. Most users have found the first test run in the instrument after heating up is not very reliable and is usually discarded. Even though the instrument temperature controllers say the bowl is up to temperature in 20-30 minutes, experience shows that the temperatures are not stabilized for at least 2 hours and possibly longer. The main reason for this is that the rotors are not heated and have a long heat transfer path to get up to temperature.
Consider an alternate method for heating the unit that might also give you some valuable information. The unit should be turned on when it is intended to be used that day, but (instead of setting temperatures to the normal test temperature) set them to a low temperature, such as 40°C. Then program to ramp up in temperature to the normal test temperature over about 40-50 minutes. In the time that it takes to prepare a sample and get everything else ready — about 10 minutes — the bowl temperature will have stabilized at 40°C. Of course, the rotors are not up to temperature, but that doesn't matter for this test. The test is started and the sample loaded. Normally, the unit can be left unattended as the test runs just like when it is turned on to heat up.
When the test is completed in 40-50 minutes, the results will yield much more detail about the fusion characteristics of the material tested than obtained in the normal fusion test. And the bowl and rotors will be at the normal test temperature and ready for the first normal test!
An example of the results from this test method are shown in Figure 1. A typical rigid vinyl window compound was tested under three different conditions. All started at 40°C and ramped up to 175°C. The first two were ramped up in 50 minutes, while the third was ramped up in 40 minutes. The first and third were tested at 50 rpm while the second was tested at 75 rpm. Because the fusion time is affected by the process conditions, only the torque versus temperature graph is shown.
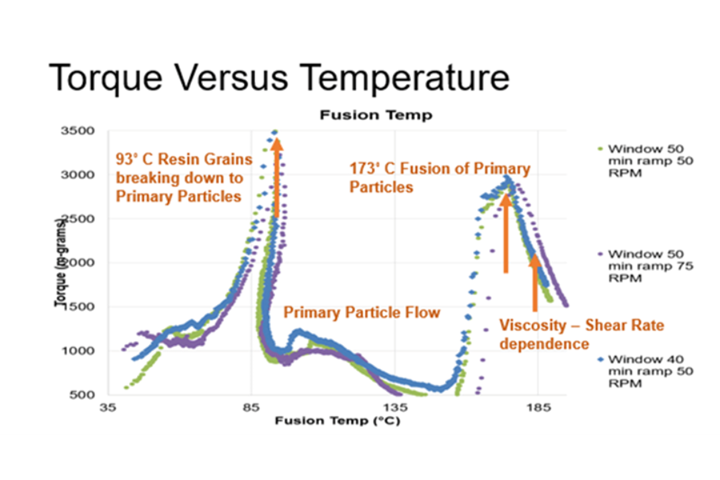
FIG1 Typical rigid vinyl window compound was tested under three different conditions. The maximum torque shown here, at about 173°C, is where all of the primary particles have fused into a true polymer melt. Above this temperature the result is a viscosity versus temperature plot. Photo Credits: Randy Brown
The torque begins to rise at about 65°C, which is the Tg of the resin and where the molecules begin to move and interact. The approximate 150-micron resin grains formed in the polymerization process are made up of bundles of 1- to 2-micron primary particles. It can be seen that all three show a peak torque at 93°C, where the resin grains are all broken apart and the primary particles become the flow units. This primary particle flow regime has a viscosity that can be measured in this region.
At a sufficiently high enough temperature, these primary particles begin to fuse, causing a rise in torque. The maximum torque shown here, at about 173°C, is where all of the primary particles have fused into a true polymer melt. Above this temperature the result is a viscosity versus temperature plot. Because viscosity is both a function of temperature and shear rate, it should not be surprising that the viscosity is the same for the two tests at 50 rpm but different at 75 rpm. Although these results show little difference between a ramp time of 40 versus 50 minutes, it is likely that there will be a minimum time needed for the temperatures to come up and yield reliable results.
Figure 2 shows the test results of three different molecular weight resins in a simple formulation. A 1% liquid tin stabilizer, along with 1% calcium stearate and 1% paraffin wax, were added to each resin. The results show a first peak in torque at 93°C for all three resins indicating that this is more a function of the polymerization than of molecular weight. There is very different torque (viscosity) in the primary particle region, which deserves more study. The primary particles begin fusing at about the same temperature, but final fusion is affected by molecular weight and, of course, viscosity of the melt is affected by molecular weight.
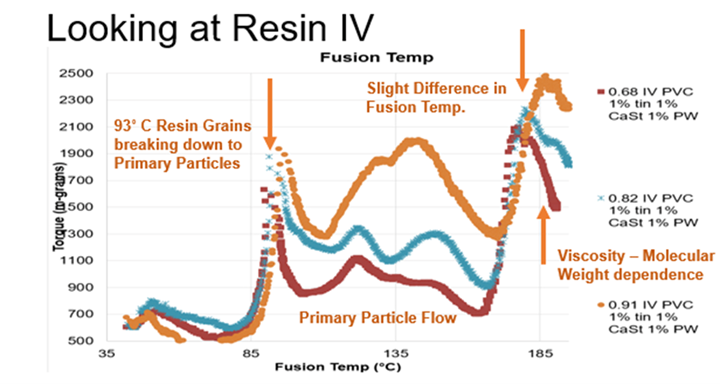
FIG 2 Test results of three different molecular weight resins in a simple formulation.The results show a first peak in torque at 93°C for all three resins indicating this is more a function of the polymerization than of molecular weight.
This room-temperature fusion test is too time consuming to be used as a primary test method. However, if used as the startup test every day the unit is used, it results in faster heat up time to give more efficient utilization of the torque rheometer and valuable fusion information that may be missed with a standard fusion test.
About the Author: Randy Brown is a plastics engineer with both a bachelor’s degree in chemical engineering and a master’s degree in polymer science from the University of Akron. He has more than 35 years of experience with various plastics processing companies. His entire career has been involved with developing new products, formulations and processing technology in the plastic extrusion industry. Although he has worked with practically every different thermoplastic, the majority of his work has been involved with PVC. He is a member of the Vinyl Division Board of SPE, holding various positions, including president and treasurer. Contact: 513-208-6651; iplasticpi@zoho.com
Related Content
X-Ray Vision Inside Parts Gets More Affordable for Processors
Shimadzu’s new benchtop x-ray CT scanner provides internal and external metrology and flaw detection at a fraction of the previous cost.
Read MoreHandheld NIR Instrument Distinguishes PET from PETG
Mobile spectroscopy from trinamiX detects more than 30 different plastics—and now PET vs. PETG as an aid to recycling.
Read MoreFast, Simple QC Method Directly Quantifies Recycled Content in Plastics
Novel fluorescence-based spin-out technology provides a rapid and reliable method to measure and certify recycled content in a wide range of plastics.
Read MoreMeasuring Technology Specialist Pixargus Acquired by CiTex Group
A global player in optical inline quality control, Pixargus is intensifying presence in U.S. & Asia under CiTex umbrella.
Read MoreRead Next
People 4.0 – How to Get Buy-In from Your Staff for Industry 4.0 Systems
Implementing a production monitoring system as the foundation of a ‘smart factory’ is about integrating people with new technology as much as it is about integrating machines and computers. Here are tips from a company that has gone through the process.
Read MoreHow Polymer Melts in Single-Screw Extruders
Understanding how polymer melts in a single-screw extruder could help you optimize your screw design to eliminate defect-causing solid polymer fragments.
Read MoreTroubleshooting Screw and Barrel Wear in Extrusion
Extruder screws and barrels will wear over time. If you are seeing a reduction in specific rate and higher discharge temperatures, wear is the likely culprit.
Read More