Tracing the History of Polymeric Materials -- Part 30: Polyurethane
In the world of polymers, polyurethane chemistry is probably the most versatile. This a resulted in a wide range of products made from these materials and given the industry the flexibility to respond to the progressive march of regulatory concerns.
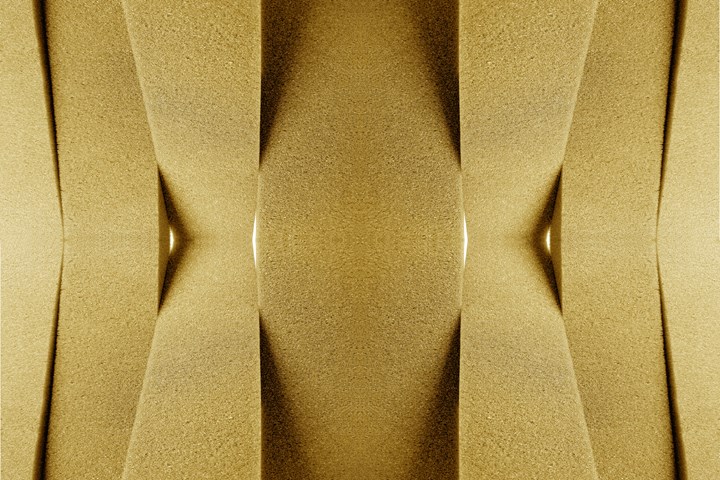
Polyurethanes show tremendous versatility, but are also subject to various regulatory requirements – such as for flame and smoke performance, environmentally safe blowing agents, and residual isocyanate emissions. (Photo: Getty Images/Akmad Bayuri)
We mentioned in our last installment that the investigation into polyurethane chemistry took place at the same time that polyesters and nylons were undergoing development. A look at the chemistry of the functional groups for these three polymers, provided in Fig. 1, shows the similarities of these three chemistries. This similarity in structure often results in discussions that treat PURs as sort of a hybrid between nylons and polyesters. While there are some similarities, there are also important differences.
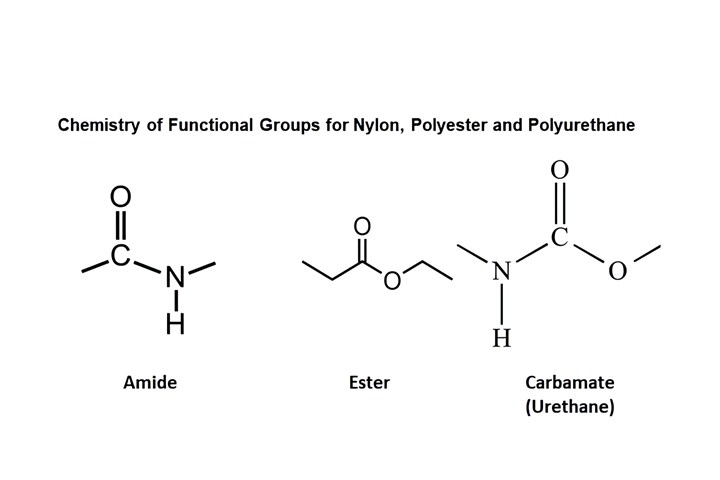
A look at the functional groups for these three polymers shows the similarities of these three chemistries, but also distinct differences. (Image: Mike Sepe)
First, PURs “grew up” as materials that are capable of functioning as elastomers, although rigid PURs are certainly an important part of the product mix. Over time, nylons and polyesters both developed into materials that were softer and more flexible. But their original introduction was as either a semi-rigid thermoplastic or as a fiber.
Another important difference can be observed in the chemical reaction that creates these three materials. The original nylon chemistry pioneered by Wallace Carothers at DuPont that became nylon 66 is characterized as a condensation reaction. This term refers to the fact that low-molecular-weight by-products are formed during polymerization that must be removed to promote the achievement of a satisfactory chain length. Polyesters also follow this chemical route.
At first glance, the reaction that produces PURs is similar, with the isocyanate reacting with either an ether or an ester. An important difference is that this reaction produces no unwanted by-products. This, combined with the very high reactivity of the isocyanate group, is the factor that made reaction injection molding (RIM) possible. RIM involves polymerizing the material and forming the part in the mold in a single step. If a chemical reaction produces low-molecular-weight volatile by-products, an in-mold process is not possible unless some method of devolatilization can be engineered. But in the case of polyurethanes, no such problem was encountered.
The options in creating PUR chemistry seem almost endless.
A distinctive detail of the chemical reaction that produces PURs is the use of an excess of isocyanate to ensure that the chain end groups are isocyanate groups. Typically, the ratio of isocyanate (NCO) to hydroxyl (OH) groups is about 1.01-1.1. If the ratio drops below 1.0 it results in a decline in mechanical strength and resilience and an increase in compression set of the polymer.
The Effect of Excess Isocyanate
The excess of isocyanate introduces another interesting and unique feature of PUR chemistry. The excess isocyanate present in the fabricated product is capable of reacting with the urethane group to form something known as an allophanate structure. This acts like a chemical crosslink that is not as stable as the physical crosslinks in true thermoset systems, but can still enhance mechanical performance. If a urea group is available, the excess isocyanate can react with it to form something called a biuret group, with similar consequences.
The significance of this chemistry is that it can be stimulated through an annealing process that can substantially improve the performance of molded polyurethane parts. We have addressed this phenomenon in a previous discussion on the effects of annealing polyurethanes.
The options in creating PUR chemistry seem almost endless. But one feature of the historical development of PURs is that it chronicles the interaction between technology and regulation. For many decades the preferred foaming agents for polyurethanes were CFCs. These were phased out in the mid-1990s in favor of HCFCs. These were, in turn phased out in the early 2000’s in favor of HFCs, with the EU leading the way in 2003. Today, ironically, the foaming agent of choice is CO2, which was the original agent given off when Bayer first created his foam materials. Pentane, a low-boiling-point hydrocarbon, is also used.
PUR Foams and Flame Retardants
Polyurethane foams were also impacted by considerations of flame retardancy. Because polyurethane foams find use in consumer items like mattresses and upholstered furniture, where concerns over flammability naturally arise, many of these products made use of flame-retardant chemicals. Until 2004, the flame retardant of choice was pentabromodiphenyl ether, or penta-BDE. This is one of a class of flame retardants that has effectively been banned due to concerns over the release of toxic by-products during combustion. So, the PUR foam industry was challenged with finding new systems that would still protect the consumer who chose to smoke in bed while continuing to meet the new regulatory mandates.
This has been, as one might imagine whenever the regulators get involved, a lengthy process that took almost a decade and involved multiple federal and state organizations. As noted consultant Glenn Beall has said, “When legislators legislate, industry innovates.” Since penta-BDE manufacturing in the United States was phased out in 2004, new introductions have included chemical routes using a variety of organophosphates, as well as incorporating graphite additives or surface treatments such as are used with natural fibers.
As noted consultant Glenn Beall has said, “When legislators legislate, industry innovates.”
A new challenge confronted the PUR industry in the middle of the last decade when new concerns were raised about levels of residual isocyanates in urethane polymers. As we have mentioned, polyurethane chemistry employs an excess of isocyanate when running the reaction between this constituent and the polyol. This means that after the polymer is produced, this excess isocyanate will be present in the polymer as a residual. The presence of this excess isocyanate can be beneficial in improving properties during annealing processes.
But in 2015 the EPA identified potential concerns with the toxic effects of residual isocyanates. This placed additional constraints on the polymerization process as well as a requirement for monitoring residual isocyanates in the materials.
More Monitoring, Testing
These new requirements led to a need for innovations in monitoring and quantitative testing for these residuals. Offline testing of isocyanate residuals results in a very long feedback loop to the production environment, making appropriate process control and adjustment problematic. The need for tighter control led to innovations in in-process monitoring using mid-infrared spectroscopy. The isocyanate functional group displays a distinctive peak in the mid-IR spectrum at 2270 cm-1. The intensity of this peak can be monitored during the polymerization reaction in real time, allowing for much greater control over this parameter and responding to the new regulatory pressures. This technology gives excellent agreement with traditional offline titration techniques.
Polyurethane chemistry is probably the most versatile in the entire world of polymers. It would require an entire book to do it justice. Hopefully, this review gives the reader a sense of how valuable the chemistry can be, how varied the types of products are that can be made from these materials, and how the industry has attempted to respond to the progressive march of regulatory concerns.
ABOUT THE AUTHOR: Michael Sepe is an independent materials and processing consultant based in Sedona, Ariz., with clients throughout North America, Europe, and Asia. He has more than 45 years of experience in the plastics industry and assists clients with material selection, designing for manufacturability, process optimization, troubleshooting and failure analysis. Contact: (928) 203-0408 • mike@thematerialanalyst.com
Related Content
Why (and What) You Need to Dry
Other than polyolefins, almost every other polymer exhibits some level of polarity and therefore can absorb a certain amount of moisture from the atmosphere. Here’s a look at some of these materials, and what needs to be done to dry them.
Read MoreThe Strain Rate Effect
The rate of loading for a plastic material is a key component of how we perceive its performance.
Read MoreTunnel Gates for Mold Designers, Part 1
Of all the gate types, tunnel gates are the most misunderstood. Here’s what you need to know to choose the best design for your application.
Read MoreA Simpler Way to Calculate Shot Size vs. Barrel Capacity
Let’s take another look at this seemingly dull but oh-so-crucial topic.
Read MoreRead Next
Tracing the History of Polymeric Materials, Part 28: Making LCP's Melt Processable
Liquid-crystal polymers based on a single monomer produces a polymer with a very high melting point.This presents two problems. Here’s how they were solved.
Read MoreTracing the History of Polymeric Materials -- Part 29: Polyurethane
This material family has unparalleled versatility, not only in terms of the forms the material can take, but in the different ways in which it can be processed.
Read MoreTracing the History of Polymeric Materials, Part 27: Liquid-Crystal Polymers
Liquid-crystal polymers debuted in the mid-1980s, but the history of the chemistry associated with this class of materials actually starts a century earlier.
Read More