Education at NPE2024: 3D Printing Workshop
Learn about the emerging possibilities for part production via 3D printing/additive manufacturing.
The 3D Printing Workshop at NPE2024: The Plastics Show, is an immersive, half-day workshop focused on the emerging possibilities for part production via 3D printing/additive manufacturing. The workshop will take place Wednesday, May 8, at 1-5 p.m. in the Orange County Convention Center.
Attendees will benefit from a program focused on practical applications of 3D technologies related to plastics processing. This event will conclude with a 3D Printing Industry Reception sponsored by Additive Manufacturing Media, part of Gardner Business Media.
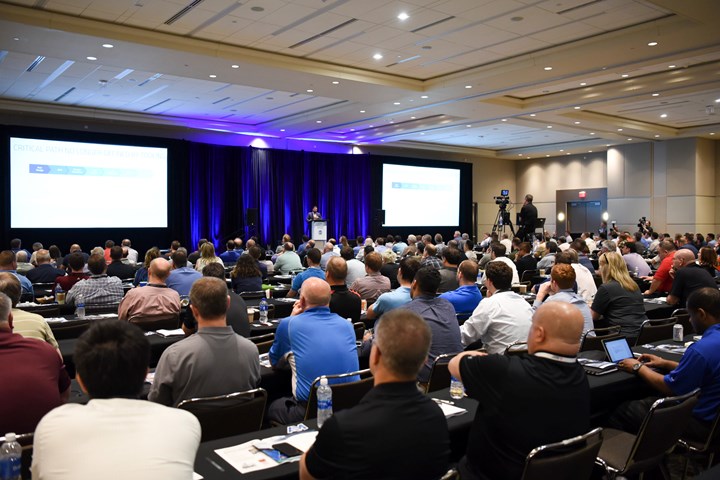
The program, put together by Additive Manufacturing, shapes up as follows:
- 1:15-1:45 p.m. — Plastic 3D Printing vs. Injection Molding: Making the Best Choice
Speaker: Greg Paulsen, Director, Applications Engineering and Marketing at Xometry
Greg Paulsen leads the Applications Engineering Team at Xometry, working directly with customers on unique projects and sharing the capabilities of Xometry's digital manufacturing platform. With 15 years of experience, he has served roles within product development, business leadership, factory operations, digital marketing and technology management.
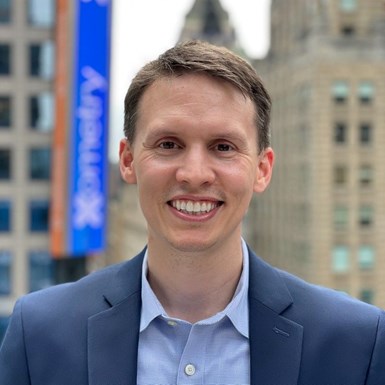
Greg Paulsen, Xometry
Session Description: This session will address the question of when to opt for plastic 3D printing over injection molding. The presentation aims to give attendees a comprehensive understanding of when and why to employ plastic 3D printing or injection molding, ensuring informed decision-making for efficient and innovative manufacturing solutions. The session will highlight the practical applications, benefits and limitations of additive manufacturing and injection molding, and how these decisions guide the journey of a product’s life cycle — from initial conceptualization and design sensitivity to end-of-life repair and replacement considerations.
During the session, popular additive manufacturing technologies will be reviewed in-depth, including SLS, HP MJF, FDM, SLA and production photopolymer technologies. Paulsen will identify the 'sweet spots' where additive manufacturing excels and situations where its limitations become apparent, including cost-effectiveness. Additionally, the session will touch upon emerging trends in advanced manufacturing, including hybrid approaches that utilize 3D printing for tooling. The presentation will conclude with a Q&A session with the audience.
- 1:45-2:15 p.m. — Qualification of B-Basis Design Allowables for FGF Process for Conducting PEKK for Large Aerospace Structure
Speaker: Si Chen, Senior Specialist Engineer, Eaton Research Labs
Si Chen is a senior specialist engineer at Eaton Research Labs at Eaton Corp. Her work focuses on polymer composite additive manufacturing and material development for aerospace and electrical applications. She holds a bachelor’s degree and a master’s degree from Cornell University, and a Ph.D. from Purdue University, all in chemical engineering. She has combined 15-plus years of industry experience in material development, semiconductor and manufacturing. She is also a Six Sigma Black Belt.
Speaker: Javed Mapkar, Senior Technology Manager, Eaton Research Labs
Javed Mapkar began his career with Eaton in 2008 after he earned his Doctor of Philosophy in chemical engineering from The University of Toledo. He is presently senior technology manager for the Advanced Materials & Processes group at Eaton’s Research Labs center located in Southfield, Michigan. The global team focuses on advancement in high-performance polymer composites for injection molding and additive manufacturing, printed electronics, and advanced metals and alloys. Mapkar has approximately 19 years of experience in the area of polymer nanocomposite and structural composites with primary focus on material & process development.
Session Description: Generation of design allowables are critical and required for risk reduction and successful qualification of potential aircraft components by the Federal Aviation Administration. Enabled by the increasing maturity of the fused granular deposition (FGF) process, this work describes the development and qualification process of such an allowable for the FGF process. The qualification methodology, test standards and specification documents will be discussed. With this process, Eaton is capable of producing large-scale (up to 6 feet tall), airtight, aerospace structures made with conducting nanocomposite-based PEKK.
- 2:15-2:45 p.m. — From 1 to 1 Million Parts: How Merit3D Is Helping Additive Manufacturing Evolve Into Mass Production
Speaker: Spencer Loveless, Founder/CEO, Merit3D
Spencer Loveless is the second-generation CEO/Owner of Dustless Technologies and founder/CEO of Merit3D. He is an entrepreneur at heart and loves growing businesses in rural Utah. Loveless joined the company full time after he graduated from Utah Valley State University with a degree in Technology Management and Aviation. Dustless Technologies is located in Price, Utah, and a manufacturer of industrial vacuums and dust collection attachments. They manufacture and sell to many big box stores throughout the world. Merit3D is an additive manufacturing (3D printing) service provider.
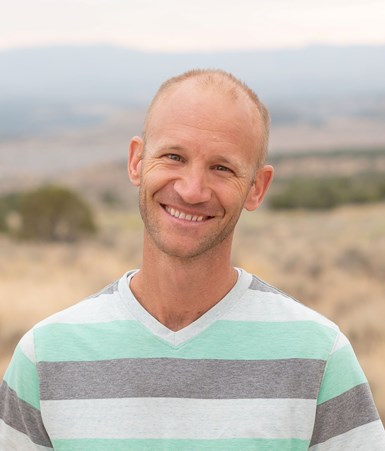
Spencer Loveless, Merit/3D
Session Description: 3D printing has been around for about 40 years now. Invented in the 1980s, it has always been a way to prototype parts. Three factors are changing to make this a viable solution for mass production: (1) Costs are coming way down. (2) Quality of parts is going up drastically. (3) Print speed is increasing exponentially. With these three metrics converging, mass production through 3D printing is now possible. Merit3D received the first order for over 1 million pieces of a single component, something that many people thought wouldn’t happen for 10 years. This presentation will discuss the landscape and what the plastic industry needs to do to aid in this evolution and continue to take part in it.
- 2:45-3:00 p.m — AFTERNOON BREAK
- 3:00-3:30 p.m. — From Part ID to Quality Mass Production
Speaker: Daniel Baker, Program Manager, Plastics, Endeavor 3D
Daniel Baker leads plastics manufacturing at Endeavor 3D, located just outside of Atlanta. In his role of program manager – plastics, Baker manages the workflow from part identification through end production. He is also heavily involved in the early sales cycle, helping educate and guide customers on application discovery and DfAM, and prepare parts for volume production. Prior to joining the team at Endeavor 3D, Daniel has been working in the additive industry for 8 years leading manufacturing engineering for a wide range of polymer technologies, including DLS, SLA, Binder Jetting, Multi Jet Fusion and FDM.
Session Description: Understanding the advantages of Additive Manufacturing enables organizations to better innovate and revolutionize current and future manufacturing processes. Being able to process parts from part identification all through part qualification after manufacturing is critical in ensuring confidence with end users and acceptance. Organizations today are utilizing lean manufacturing and transforming most production facilities into factories of tomorrow. By having additive manufacturing in their arsenal, companies will then be able to improve efficiency by cutting costs with just in time manufacturing and product innovation.
In this presentation, you will learn how to: evaluate multiple additive manufacturing technologies to validate appropriate production process; down select the most important part features and requirements for optimal results; ensure quality results using Endeavor engineering excellence and state-of-the-art QC lab; and prove the business case against injection molding for volume production.
- 3:30-4:00 p.m. — 3D Printed Tooling to Support Injection Molding/Moldmaking
Speaker: MJ Belmont, Westminster Tool
MJ Belmont has been with Westminster Tool for 9 years, establishing a long and diverse foundation in injection molding technical knowledge. His experience over the years includes exposure to almost every area of the moldmaking business, from marketing to operations, quoting to project management. Today, his focus lies on the customer experience, helping customers overcome their biggest molding problems with comprehensive project oversight.
- 4:00-4:30 p.m. — Understanding the Value of AM’s Bridge Production Opportunity
Speaker: Andrew Roderick, Senior Applications & Sales Engineer, Extol
Andrew currently works as the senior applications and sales engineer for Extol’s Additive Business Unit. He is passionate about design for additive and helping customers find new applications for 3D printing. Roderick has been involved in additive for the last 7 years and was a key driver in the launch of Extol’s Digital Development Center. In this role, he works closely with customers to find high-value applications as well as support them in functional prototyping needs. He has been with Extol for 9 years and has worked in various other roles, including tooling designer, custom assembly equipment designer and innovation engineer, where he converted a component designed for injection molding to an end-use additive part that increased the performance of the nanoSTAKE product. Roderick led the efforts of providing a customer with critical production-scale additive parts during the COVID-19 pandemic.
Session Description: Production applications for 3D printing get most of the attention, but bridge production applications deliver some of the highest value applications for additive manufacturing. Learn why using additive manufacturing for bridge production is so valuable and the keys to develop and launch successful applications.
You can register for this conference here.
Related Content
TAPPI to Provide Film Education Program at PTXPO 2023
Second-ever PTXPO will feature a robust education program on flexible film, with more technical programming in the works.
Read MoreTeaching Kids About the ‘Magic’ of Manufacturing
Making something out of (almost) nothing is an ‘eye opener’ for youngsters in their first exposure to plastics processing.
Read MoreKraussMaffei and NIAR Propel Injection Molded Thermoplastic Composites
The maker of plastics processing equipment has placed a machine and an injection molding expert in NIAR’s ATLAS lab in Wichita, Kansas, to help molding, composites and aerospace take off.
Read MoreThe Experience Curve and Well-Trained Process Technicians
Pairing external big picture training with internal job-specific instruction can help your process technicians meet quality expectations as well as production targets.
Read MoreRead Next
Advanced Recycling: Beyond Pyrolysis
Consumer-product brand owners increasingly see advanced chemical recycling as a necessary complement to mechanical recycling if they are to meet ambitious goals for a circular economy in the next decade. Dozens of technology providers are developing new technologies to overcome the limitations of existing pyrolysis methods and to commercialize various alternative approaches to chemical recycling of plastics.
Read MoreUnderstanding Melting in Single-Screw Extruders
You can better visualize the melting process by “flipping” the observation point so that the barrel appears to be turning clockwise around a stationary screw.
Read MorePeople 4.0 – How to Get Buy-In from Your Staff for Industry 4.0 Systems
Implementing a production monitoring system as the foundation of a ‘smart factory’ is about integrating people with new technology as much as it is about integrating machines and computers. Here are tips from a company that has gone through the process.
Read More